Mit PTFE verändern wir unsere Mobility und Energieversorgung, digitalisieren unser Leben und retten es in der Medizintechnik. Nicht nur in der Raumfahrt erkunden wir auf Basis dieses Werkstoffes das Universum, auf der Erde verändern wir die Grenzen des Machbaren. PTFE als Hauptgruppe der Fluorpolymere – ob in Standard Form, modifiziert oder als Compound – ist ein Werkstoff, der ungeachtet der aktuellen PFAS-Diskussion bleiben wird und für optimalen Einsatz vertieftes Know-how erfordert. Hier ist es.
Weitere Veranstaltungen
18. Bondexpo
Internationale Fachmesse für Klebtechnologie
Datum: 07.10.2025 - 09.10.2025
Veranstalter: P. E. Schall GmbH & Co. KG
Ort: Messe Stuttgart
DIAM & DDM 2025
Der größte nationale Branchentreff für Industriearmaturen & Dichtungstechnik
Datum: 12.11.2025 - 13.11.2025
Veranstalter: HuT - Messe & Event GmbH
Ort: Jahrhunderthalle Bochum
Services
Expertenmeinungen
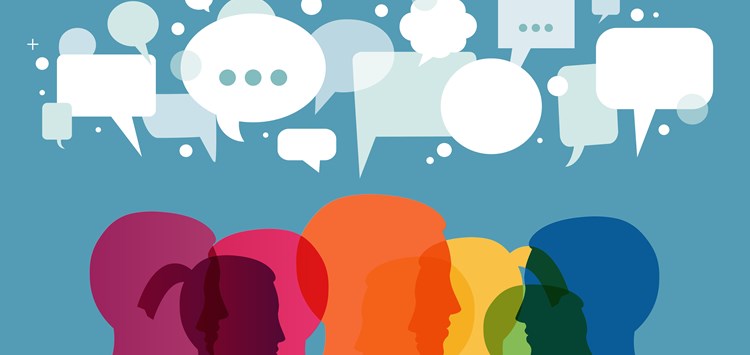
(Bild: Adobestock_Julien Eichinger)
Die Umfrageergebnisse der ISGATEC-Umfragen und "Im Fokus–Statements" zu Dichtungsthemen liefern Impulse für alle Spezialist:innen.
Stand der Technik
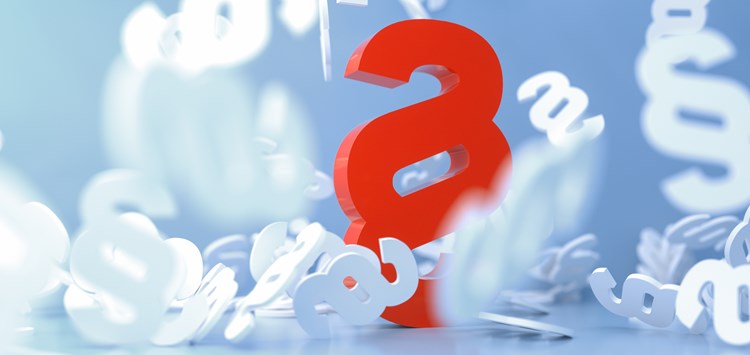
(Bild: AdobeStock_Studio_East)
Anhand von Beiträgen und Praxisbeispielen zeigen Experten, was bei verschiedenen Lösungen in diesem Kontext zu beachten ist bzw. war.
Schadensanalyse
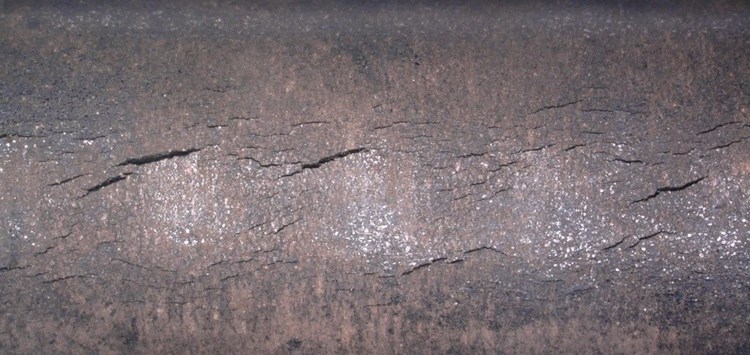
(Bild: OPR Group GmbH)
In Zusammenarbeit mit der OPR Group sind hier die unterschiedlichsten Schadensmechanismen (inkl. Praxistipps) beschrieben.
Dichtungstechnische Grenzen
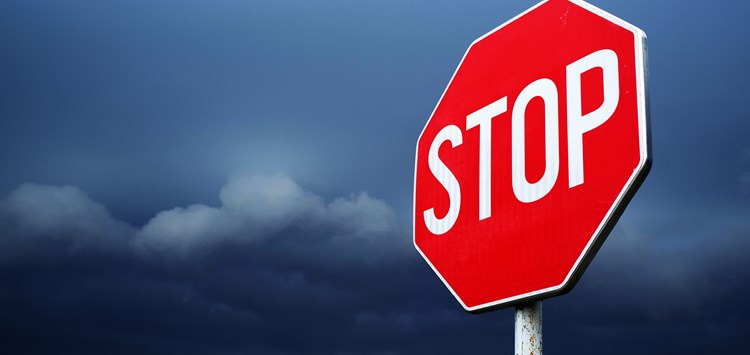
(Bild: AdobeStock_Rechitan Sorin)
Dichtungen und ihre Materialien können systembedingte Grenzen haben – Peter Thomsen beschreibt solche Fälle und gibt Tipps zur Vermeidung von Problemen.
Checklisten
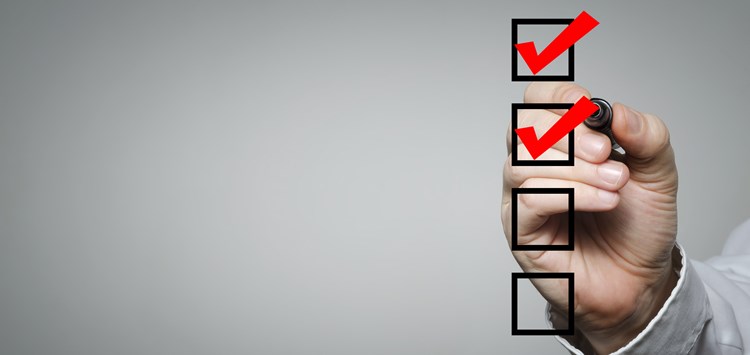
(Bild: Adobestock_NatasaAdzic)
Diese Checklisten für Lastenhefte sollen eine Hilfe für ein systematisches Vorgehen und die projektbezogen richtige Auswahl einer Dichtungslösung sein.
Basics der Dichtungstechnik
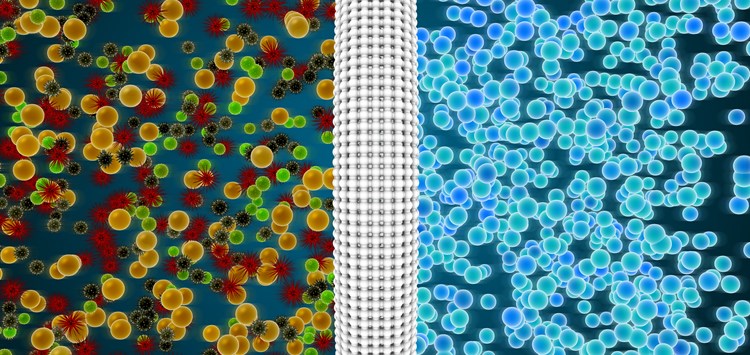
(Bild: Adobestock_begiz)
Für den richtigen Einsatz von systemrelevanten Dichtungen brauchen alle Beteiligten entlang der Wertschöpfungskette fundiertes dichtungstechnisches Grundwissen.
KI/Simulation
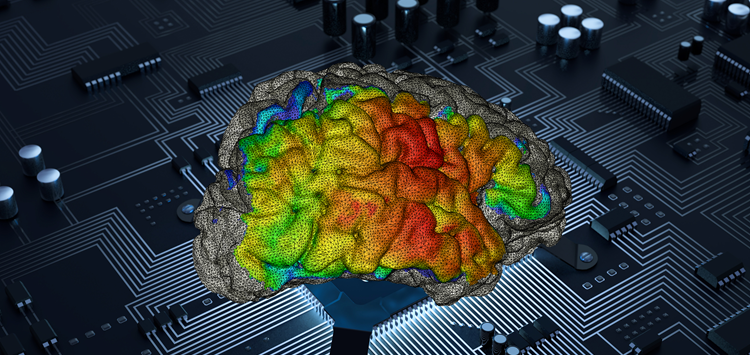
(Bild: AdobeStock_ fotomek,SimpaTec)
Dr.-Ing. Michael Bosse begleitet die Entwicklung und zeigt technische Felder auf, die unter KI-Gesichtspunkten betrachtet werden könnten und sollten.
Dichtelemente für Flansche
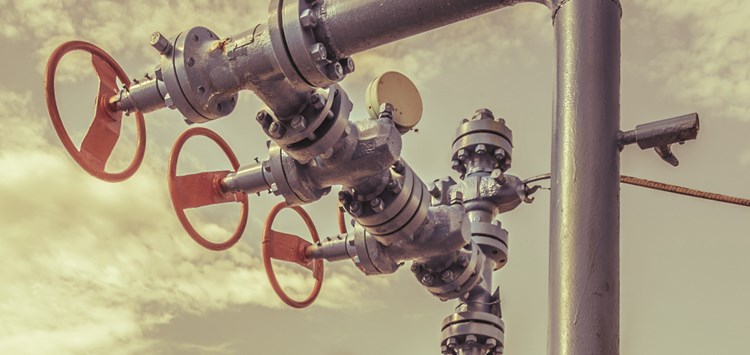
(Bild: AdobeStock_Ded Pixto)
Statische Dichtelemente kennen und in der Praxis richtig einsetzen.