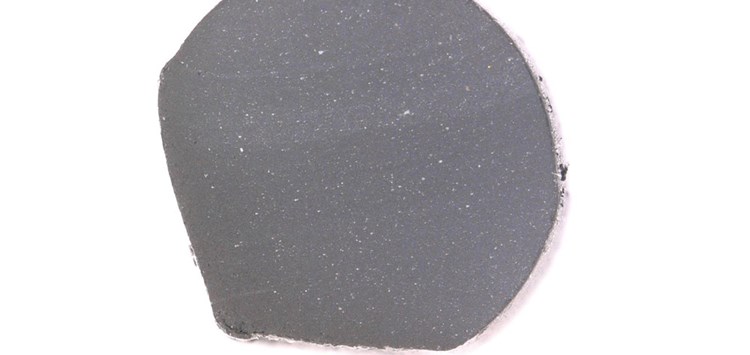
Querschnitt eines geschädigten O-Rings: Kurzzeitige Überhitzung führt zu lokalen Abflachungen im Bereich des Wärmeeintrags (Bild: O-Ring Prüflabor Richter GmbH)
16.09.2019 Schäden erkennen und vermeiden
Hohe bleibende Verformung
Dichtungen werden aus den verschiedensten Gründen in der Praxis geschädigt. Neben dem Erkennen der Schadensursache werden dann mögliche Abhilfemaßnahmen wichtig – für die Instandhaltung, aber auch bereits bei der Erstausrüstung von Anlagen mit Dichtungen.
Eine hohe bleibende Verformung als Ausfallursache liegt dann vor, wenn eine Dichtung durch eine fehlende elastische Rückverformung deutlich vor ihrer alterungsbedingten Lebensdauergrenze bzw. erheblich vor der Lebensdauererwartung des Anwenders ausfällt.
Ein häufiger Grund dafür ist eine Untervulkanisation, d.h. ein Fertigungsmangel infolge von fehlerhafter Prozessführung. Besonders häufig davon betroffen sind in der Praxis peroxidisch vernetzte EPDM- und HNBR-Werkstoffe, weil sich hier der Vernetzungsgrad durch ein Nachtempern nicht mehr signifikant verbessern lässt. Darüber hinaus kann es einen erheblichen Einfluss durch das Polymer in der Rezeptur geben, wenn dieses entweder eine zu hohe Glasübergangstemperatur (TG) hat oder sich kristalline Sequenzen im Polymergefüge bilden können. Davon betroffen sind vor allem FFKM- und FEPM- sowie spezielle FKM-Werkstoffe (hohe TG) oder HNBR- und EPDM-Werkstoffe (kristalline Sequenzen). Zu erkennen ist das relativ einfach und zwar dadurch, dass man einen Druckverformungsrest bei erhöhten Temperaturen nach ISO 815-1 (z.B. 150 °C) sowohl nach Verfahren A (Entspannung bei Prüftemperatur) als auch nach Verfahren B (Entspannung bei Raumtemperatur) durchführt. Unterscheiden sich die Ergebnisse um mehr als 20 bis 30 %-Punkte, kann das kritisch werden.
Eine weitere Ursache kann in der Rezeptur liegen, wenn diese hohe Weichmachergehalte aufweist (häufig bei EPDM). Wenn die Weichmacher aus einer Dichtung durch Umgebungsfluide ausgewaschen werden oder ausgasen, kann dies ebenso zu einer hohen bleibenden Verformung führen.
Ein schlechter Einbauraum kann ebenfalls einen Ausfall durch hohe bleibende Verformung verursachen, wenn infolge einer zu großen Nuttiefe oder einer fehlerhaften Dichtungsauslegung der Verformungsgrad der Dichtung zu gering ist. Typisch für diese Schadensursache ist eine bleibende Verformung (Resthöhe der Dichtung = Nuttiefe) ohne signifikante Härtezunahme.
Bei einer unzulässigen thermischen oder chemischen Einwirkung zeigt sich neben der bleibenden Verformung häufig eine signifikante Härtezunahme. Zudem bricht die Dichtung bereits bei einer leichten Biegebeanspruchung oder sie zeigt Rissbildungen.
Schadensbild und problematische Bereiche: Dass sich eine Elastomerdichtung durch Temperatur- und Medieneinwirkung bleibend verformt, ist normal. Die Schadensanalyse muss feststellen, ob diese Verformung der Grund für eine Leckage war (Bild 1, 2, 3). Wichtige zu untersuchende Merkmale an der Schadensdichtung sind:
- die verbliebene Dichtungshöhe im Verhältnis zum Einbauraum,
- Gummielastizität,
- signifikante Härte- oder Volumenänderung.
Abgrenzung zu ähnlichen Schadensbildern: Der Querschnitt eines durch übermäßigen Abrieb ausgefallenen O-Rings kann auf den ersten Blick mit einer hohen bleibenden Verformung verwechselt werden.
Präventionsmaßnahmen: Um diesen Schaden zu vermeiden, genügt es in den meisten Fällen, sich bei der Auslegung einer Dichtung mit vier Punkten auseinanderzusetzen:
- Temperatur-/Zeitbeanspruchung der Dichtung,
- Verformungsgrad,
- Werkstoff und
- Verarbeitungsqualität.
Bei der Gestaltung des Einbauraumes ist zu beachten, dass gewisse Mindestverformungsgrade sichergestellt sind, bei O-Ringen mindestens
10 %. Außerdem können die Vorgaben für Rezeptureigenschaften der ISO 3601-5 weiterhelfen, den Stand der Technik einzuhalten.
Praxistipps (Prüfmöglichkeiten/Normempfehlungen): Die Druckverformungsrestprüfung (ISO 815-1) ist sehr einfach auszuführen und liefert gute Aussagen, ob ein Werkstoff zu einer hohen bleibenden Verformung neigt oder nicht. Darüber hinaus sollten immer auch Grenzwerte für Druckverformungsrestmessungen an Fertigteilen definiert werden, und zwar sowohl nach Verfahren A als auch nach Verfahren B.
Langversion des BeitragesLink zum ISGATEC-Werkstoffkompass
Seminar Tipp: Schäden an elastomeren Dichtungen – Ursachen und deren Vermeidung
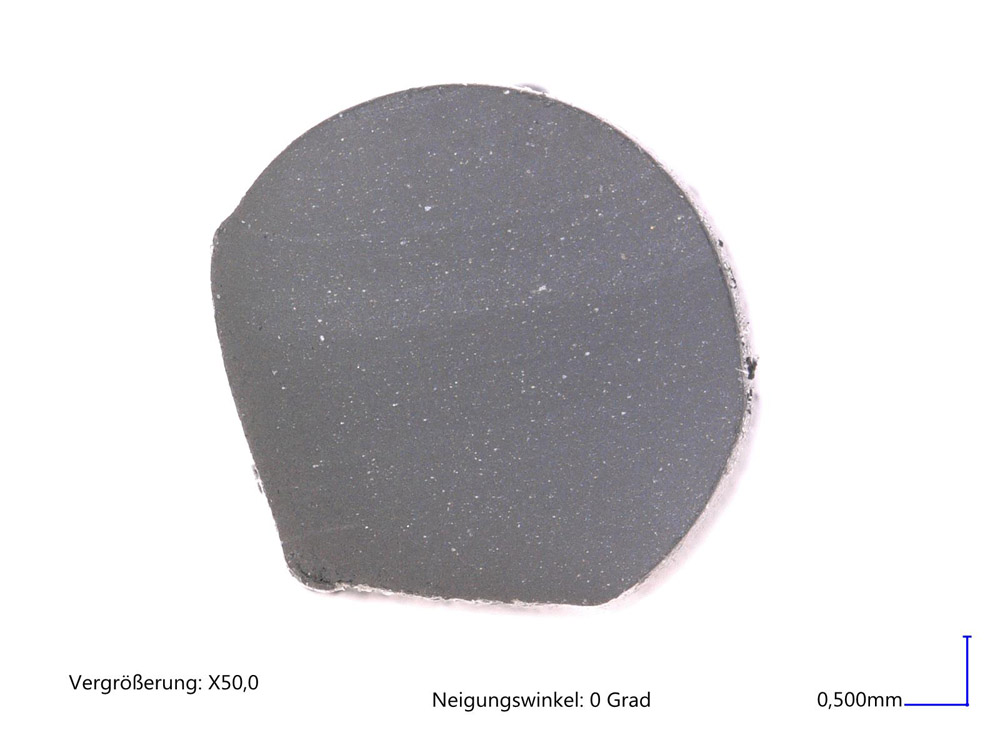
Bild 1: Querschnitt eines geschädigten O-Rings: Kurzzeitige Überhitzung führt zu lokalen Abflachungen im Bereich des Wärmeeintrags (Bild: O-Ring Prüflabor Richter GmbH)
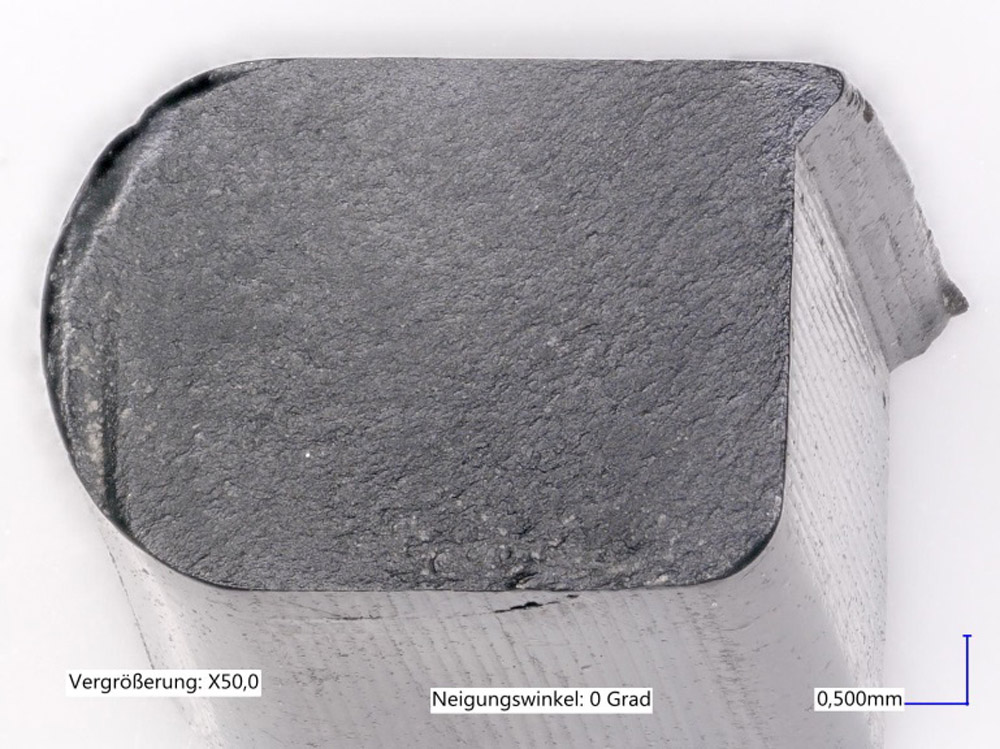
Bild 2: Bleibende Verformung und komplette Versprödung (siehe Schnittflächenstruktur) eines O-Rings durch thermische Überbeanspruchung (Bild: O-Ring Prüflabor Richter GmbH)
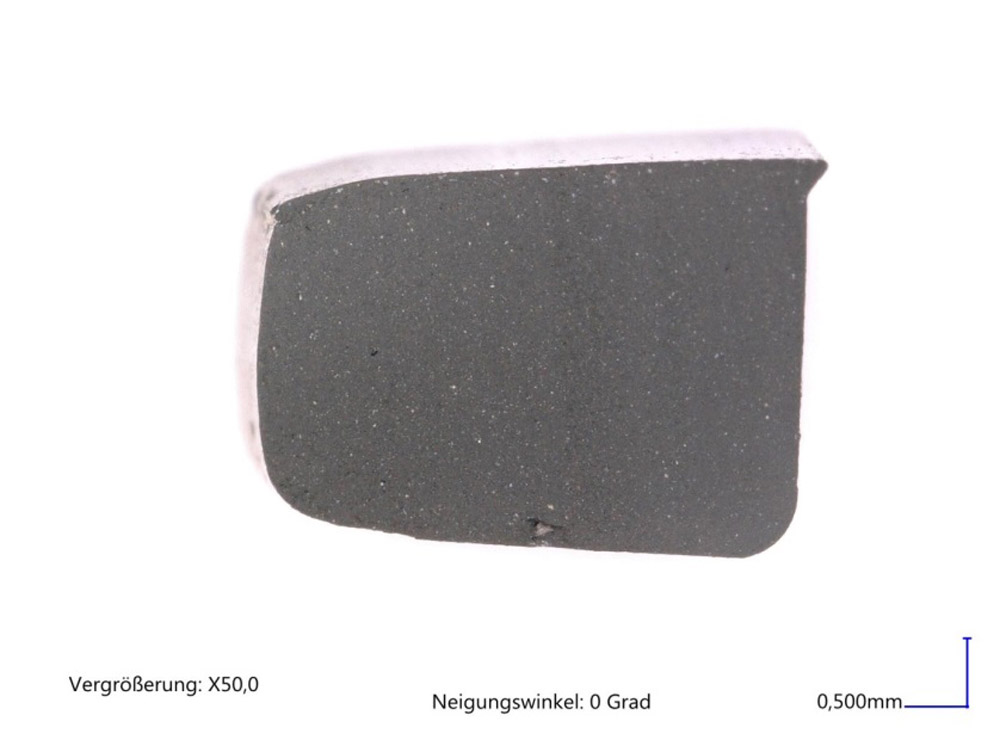
Bild 3: Bleibende Verformung eines O-Rings durch chemischen Angriff – deutlich zu erkennen der stärkere Verformungsgrad im linken Bereich (Mediumseite) (Bild: O-Ring Prüflabor Richter GmbH)