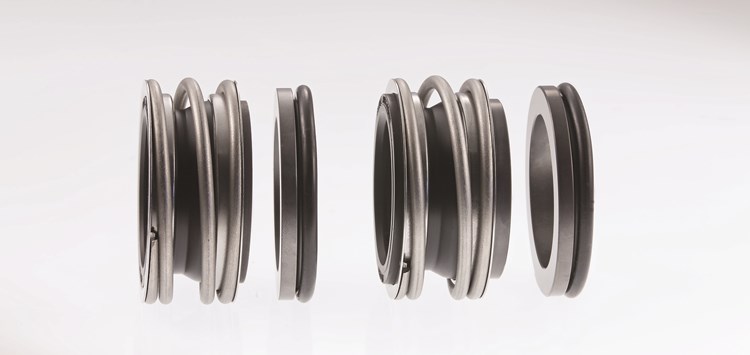
Neue Generation von Pumpendichtungen – eMG1 und eMG (Bild: EagleBurgmann Germany GmbH & Co. KG)
27.03.2017 SYSTEM-Lösungen
Moderne dynamische Dichtsysteme liefern Antworten für viele aktuelle Fragestellungen
Bei dynamischen Dichtungen ist das Systemdenken entscheidend. In Kombination mit fast allen aktuellen Trends sind quer durch alle Branchen komplexe Herausforderungen zu meistern – heute und morgen. Der Überblick der Experten zeigt interessante Aspekte.
2016 war der gesamte Markt der dynamischen Dichtsysteme geprägt durch die teilweise drastischen Preiseinbrüche im Öl- und Gasgeschäft. Die dadurch verursachte fehlende Nachfrage nach hochwertigen Pumpsystemen für Exploration, Transport und Aufbereitung hat auch den Markt für Dichtsysteme wie Gleitringdichtungen belastet. Neben dem klassischen Neugeschäft wurden die Investitionen für Service und Instandhaltung ebenfalls auf den Prüfstand gestellt und teilweise deutlich reduziert. Dieser Markttrend konnte auch durch stabile Nachfrage im Wasser- und Kraftwerksmarkt nicht kompensiert werden. Die Nachfrageschwäche wird in Zukunft durch leicht gestiegene Öl- und Gaspreise nur teilweise behoben werden. Daher werden in der Dichtungstechnik stärker differenzierte und spezialisierte Entwicklungen stattfinden. Die Forderung nach robusten Systemen mit noch längeren Laufzeiten wird weiter anhalten und damit den Trend zu hochwertigen Gleitmaterialien und Beschichtungen wie DiamondFace® verstärken. Die Diamantschichten haben ihre Praxistauglichkeit und hervorragenden Eigenschaften wie Verschleißschutz, Reibleistungsreduzierung, partielle Trockenlauffähigkeit und chemischen Korrosionsschutz längst bewiesen und werden verstarkt nachgefragt.
Darüber hinaus wird die Einführung von überwachten Dichtsystemen durch die Industrie 4.0-Initiative weiter befeuert werden, wobei der Kosten-Nutzen-Aufwand von vielen Anwendern immer noch kritisch beurteilt wird. In der Nachfrage zeichnet sich hier die Erwartung ab, noch schneller kundenspezifische Lösungen bereitzustellen. Flexibilisierung und reduzierte Lieferzeiten werden gefordert.
Schwierige Marktverhältnisse erzeugen den erkennbaren Trend, Pumpen- und Dichtungslösungen im High-End-Bereich in neue Anwendungsgebiete auszuweiten. Noch höhere Drücke und Geschwindigkeiten werden im Bereich der Tiefseeanwendungen und Multiphasentechnik gefordert. Wasserpumpen fur Energiespeicher und Pipeline-Anwendungen werden immer größer. In all diesen Märkten sind wir als renommierter Problemlöser mit hoher Qualität, ingenieurtechnischem Dichtungswissen und klarer Kundenorientierung gefragt.
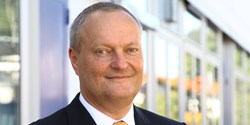
„Die wirtschaftlichen Rahmenbedingungen und Trends wie Industrie 4.0 führen zu immer spezialisierteren Dichtungsentwicklungen, die großes Know-how in allen Bereichen erfordern.“ Dr. Bernhard Jenisch, Vice President, Engineering & Innovation, EagleBurgmann Germany GmbH & Co. KG