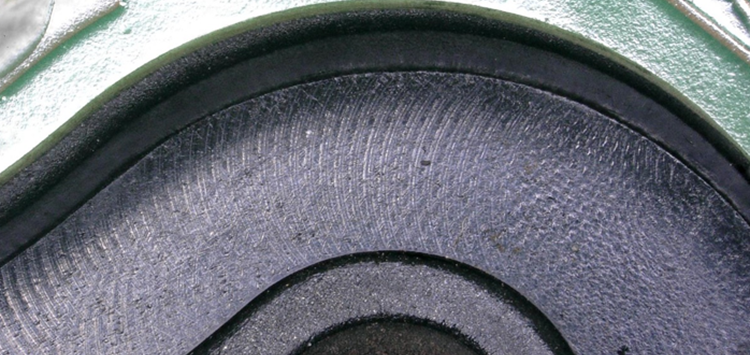
Ungünstige Oberflächenstruktur an der Dichtfläche eines Kunststoffbauteiles – durch die Riefen kann es zu einer verfrühten Leckage (Unterwanderung der Dichtung) in der Kälte kommen (Bild: O-Ring Prüflabor Richter GmbH)
09.09.2021 Schäden erkennen und vermeiden
Dichtungsversagen bei tiefen Temperaturen – es liegt nicht immer am Werkstoff
Dichtungen werden aus den verschiedensten Gründen in der Praxis geschädigt. Neben dem Erkennen der Schadensursache werden dann mögliche Abhilfemaßnahmen wichtig – für die Instandhaltung, aber auch bereits bei der Erstausrüstung von Anlagen mit Dichtungen.
Dichtungsausfälle bei tiefen Temperaturen sind für Anwender ein sehr häufiges Problem bzw. eine permanente Herausforderung. Kühlt man Elastomere stetig ab, kann man feststellen, dass das Material von einem elastischen in einen zähen, lederartigen und schließlich in einen glasartigen Zustand wechselt. Man spricht von einem „Einfrieren“ des Materials. Oberhalb dieser Glastemperatur kann es darüber hinaus durch Kristallisationseffekte zu einer weiteren Hemmung der Dichtungsrückstellung in der Kälte kommen, wovon immer wieder Anwender von EPDM- und HNBR-Elastomeren überrascht werden. Am gutmütigsten reagieren Elastomerdichtungen, wenn sie im druckbeaufschlagten Zustand eingefroren werden. Auch drucklos eingefrorene O-Ringe verhalten sich noch sehr gutmütig, solange keine Spalt- oder Druckbeanspruchungen bei tiefen Temperaturen auftreten. Ist dies aber der Fall, kann dadurch die Tieftemperaturgrenze um bis zu 20 K erhöht, also verschlechtert werden. Die zuverlässige Funktion einer Dichtung in der Kälte ist vom Zusammenspiel vieler Faktoren abhängig:
- Positiv wirken sich eine eher hohe Verpressung oder eine leichte Quellung durch das umgebende Medium aus.
- Negativ wirken sich eine schlechte Oberflächenstruktur (Bild 1) der Dichtflächen quer zur Umfangsrichtung, ein Schwund der Dichtung durch die Extraktion von Weichmachern oder auch eine vorausgehende starke Wärmealterung aus. Ebenso steigt das Risiko einer Leckage mit zunehmenden Spalten im Einbauraum.
Eine große Herausforderung ist für Anwendende auch der starke Einfluss der Rezeptur innerhalb einer Polymerfamilie. So kann die Glasübergangstemperatur bei NBR-Werkstoffen zwischen -19 °C und -73 °C liegen, bei FKM von -5 °C bis -45 °C variieren oder bei HNBR zwischen -13 °C und -46 °C liegen. Diese Werte beziehen sich auf DSC-Messungen im O-Ring Prüflabor.
Schadensbild und problematische Bereiche: Kommt es durch mangelhafte Kälteflexibilität zu einer Leckage, sind normalerweise keine Schädigungen an der Dichtung erkennbar. Der Schadensfall wird nur durch Anwendende bemerkt – sei es durch sichtbare Flüssigkeitsleckagen, durch gemessene Gasleckraten oder durch einen Druckabfall.
Abgrenzung zu ähnlichen Schadensbildern: Findet man nach einer Undichtheit keine Schädigungen an der Dichtung, kann das auch auf einen schlechten Einbauraum hindeuten. Das bedeutet, bevor man die Qualität der Dichtung bezüglich Kälteflexibilität hinterfragt, sollte man den Einbauraum kritisch prüfen, insbesondere bezüglich Verformungsgrad, Spaltmaßen und Oberflächenausführung.
Präventionsmaßnahmen: Zunächst einmal sollte die geforderte Kälteflexibilität mit einem Prüfverfahren spezifiziert werden, welches auch Kristallisationseffekte aufzeigt, z.B. mittels TR10-Wert nach ISO 2921 (siehe z.B. ISO 3601-5) oder mittels Druckverformungsrest bei tiefen Temperaturen nach ISO 815-2 (siehe z.B. DIN EN 549). Darüber hinaus sollten auch die Oberflächenstruktur bzw. das Herstellverfahren von Dichtflächen definiert werden, um Querstrukturen zu vermeiden.
Bei signifikanten Druck- oder Spaltänderungen bei tiefen Temperaturen wird eine FEA-Simulation empfohlen, bei der über DMA-Multifrequenzanalysen das dynamische Verhalten einer Elastomerrezeptur über das gesamte betrachtete Temperaturfenster abgebildet wird. Die zusätzlichen Kosten können sich schnell bezahlt machen, indem man bereits in der frühen Entwicklungsphase eventuelle Probleme erkennen kann.
Praxistipps (Prüfmöglichkeiten/Normempfehlungen): Das bewährteste Kälteprüfverfahren für Dichtungsanwendungen ist zweifelsfrei der TR10-Wert (nach ISO 2921) (Bild 2). Dieser ist eine realistische Grenztemperatur für Dichtungen, welche an der unteren Grenztemperatur – typische Einbauräume vorausgesetzt (z.B. nach ISO 3601-2 für O-Ringe) – noch verformbar sein müssen. Ohne Druck- und Spaltbeanspruchung ist bis zu 15 K unterhalb dieser Grenztemperatur noch Dichtheit erreichbar, in den Sonderfällen einer konstanten Druckbeanspruchung sind sogar noch tiefere Temperaturen möglich. Darüber hinaus liefert eine DSC-Analyse (z.B. nach ISO 11357-2) gut reproduzierbar die thermodynamische Glasübergangstemperatur, welche am besten mit einem Druckverformungsrest bei tiefen Temperaturen abgesichert werden sollte, um Kristallisationseffekte aufzuzeigen.
Zur Langversion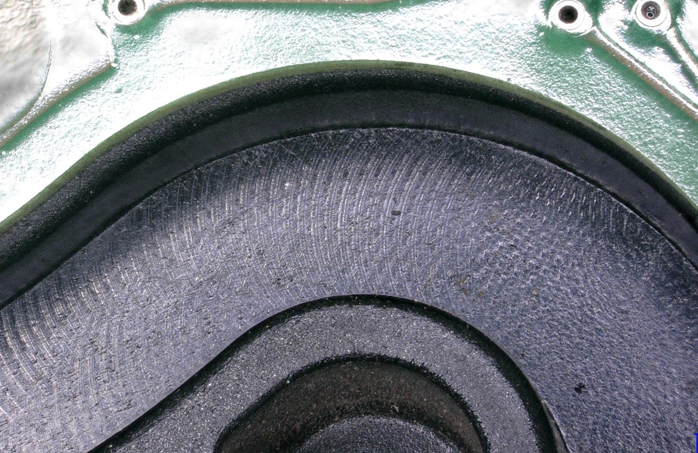
Bild 1: Ungünstige Oberflächenstruktur an der Dichtfläche eines Kunststoffbauteiles – durch die Riefen kann es zu einer verfrühten Leckage (Unterwanderung der Dichtung) in der Kälte kommen (Bild: O-Ring Prüflabor Richter GmbH)
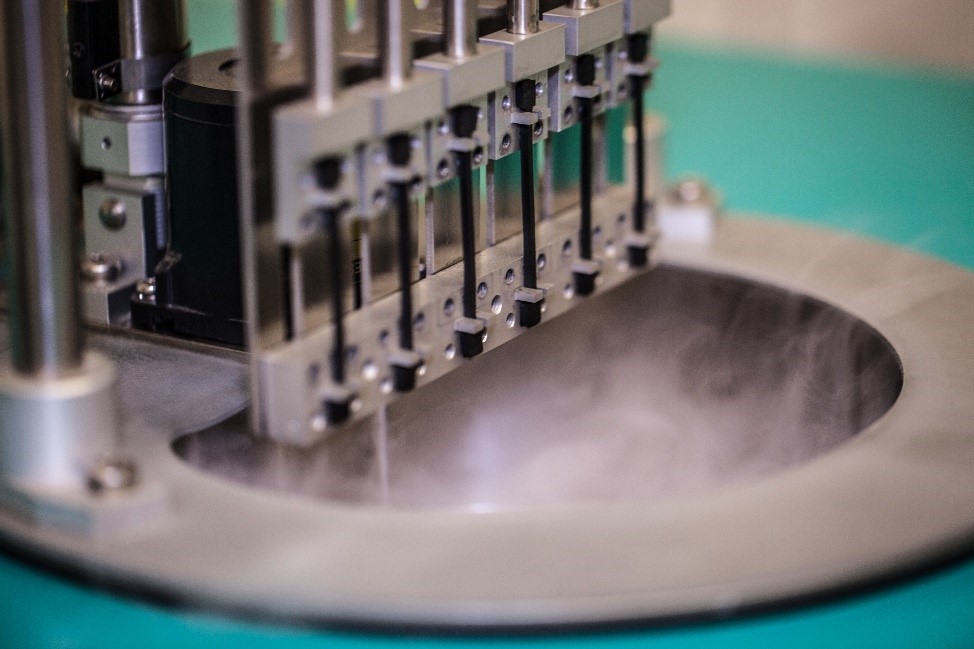
Bild 2: TR 10-Prüfung: Einfahren der gedehnten Probekörper in das Kältebad (Bild: O-Ring Prüflabor Richter GmbH)
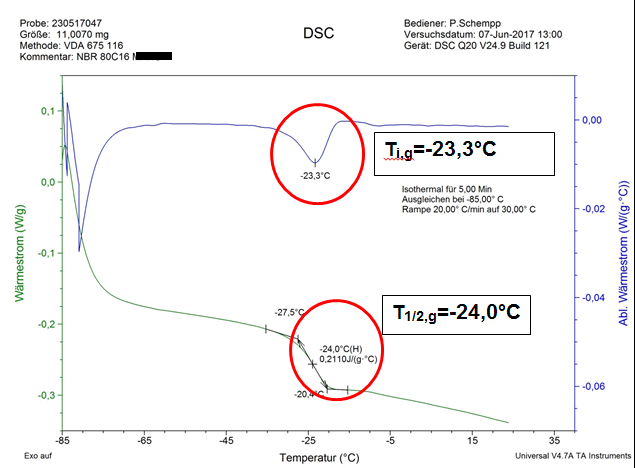
Ergebniskurven einer DSC- Prüfung zur Bestimmung des Glasübergangs (Bild: O-Ring Prüflabor Richter GmbH)