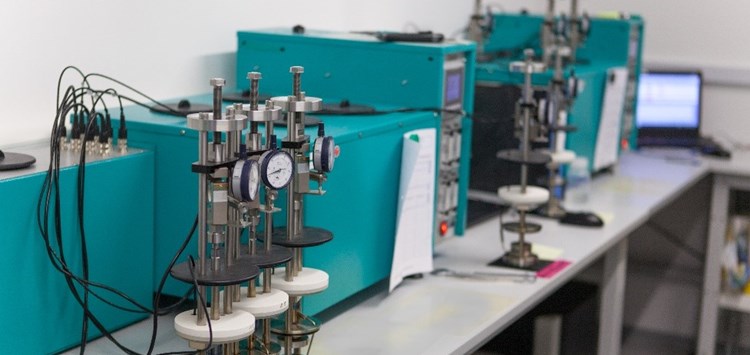
(Bild: O-Ring Prüflabor Richter)
05.09.2022 Prüfverfahren praxisgerecht anwenden – Teil 2b
Die Druckspannungsrelaxation – das kontinuierliche Messen der Dichtkraft
Ohne die richtigen Mess-und Prüfverfahren sind Entwicklungen im Bereich der Dichtungstechnik schwierig oder unnötig teuer. Diese Serie zeigt, wie man anhand klassischer und innovativer Verfahren zu relevanten und/oder hilfreichen Daten kommt.
Sowohl die Prüfung des Druckverformungsrestes (DVR) als auch der Druckspannungsrelaxation (DSR) bewerten das Rückstellverhalten eines Elastomers bei einer Spaltbeanspruchung (= Beanspruchung der Dichtung durch eine Spaltänderung bzw. eine Spaltbildung). Beim DVR ist die gemessene Größe ein Weg, während die DSR immer Kräfte anzeigt. Aus Sicht der funktionellen Beanspruchung einer Dichtung bildet eine DVR-Prüfung eine Dichtungsanwendung besser ab als eine DSR-Prüfung. Der Vorteil der kontinuierlichen DSRPrüfung ist aber die fortlaufende Durchführung, also die kontinuierliche Messung des Verlustes der Rückstellkraft. Sie ist damit materialtechnisch betrachtet eine höherwertigere und apparativ anspruchsvollere Prüfung als die Druckverformungsrestprüfung.
Das Verfahren in Kürze: Bei der Prüfung der Druckspannungsrelaxation wird eine Gummiprobe – üblicherweise 25 % – verformt. Die vom Probekörper erzeugte Rückstellkraft wird dann kontinuierlich gemessen, wobei als Referenzwert die Ausgangskraft (= Kraft 30 min. nach Prüfungsbeginn) genommen wird. Infolge von physikalischer Relaxation (zeitverzögerte Neuorientierung des Netzwerkes bzw. der Molekülketten) baut sich die Verformungskraft direkt nach der Montage bzw. Verpressung ab. Da diese Neuorientierung bei Raumtemperatur durch die Nähe zum Glasübergangspunkt wegen reduzierter Mobilität der Molekülketten gehemmt wird, braucht es eine gewisse Zeit, bis annähernd ein Gleichgewichtszustand bzgl. der Verformungskraft erreicht ist. Jeder weitere Verlust der Dichtkraft nach diesen ersten 30 min. kann dann fast vollständig der Alterung zugeordnet werden. Dies gilt für DSR-Prüfungen nach dem Verfahren A in der ISO 3384-1 (Verformung und Messung bei Prüftemperatur). Dabei wird ausschließlich der irreversible Rückstellbereich erfasst. Das Verfahren B (Messung nach Abkühlung auf Raumtemperatur) enthält auch reversible Anteile infolge von Einfriereffekten (Nähe zur Glasübergangstemperatur) und kristallinen Sequenzen (z.B. bei manchen HNBRoder EPDM-Elastomeren). Im Vergleich zur DVR-Prüfung wird die DSRPrüfung ausschließlich für die Materialqualifizierung, also für eine Beurteilung der Rezepturqualität, verwendet. Diese Methode eignet sich nicht als Fertigteilprüfung, da sie genormte Probekörper, verbunden mit langen Prüfzeiten, erfordert und preislich aufgrund des hohen apparativen Aufwandes nicht für Reihenprüfungen geeignet ist. Typische Prüfzeiten für die DSR betragen zwischen 6 Wochen (1.008 h) und 18 Wochen (ca. 3.024 h). In Ausnahmefällen beträgt die kürzeste Prüfzeit eine Woche. Die typischen Prüftemperaturen sind werkstoffabhängig und liegen zwischen 125 °C und 200 °C, für DVGW-Zulassungsprüfungen nach DIN EN 682 liegen sie teilweise auch bei 23 °C. Die Ergebnisse aus der DSR-Prüfung werden gerne als Datengrundlage zu Lebensdauerberechnungen nach dem Ansatz von Arrhenius verwendet (Bild 1). Als Ergebnis erhält man einen relativen Abfall der Dichtkraft in Prozent, bezogen auf den Ausgangswert. Bei der diskontinuierlichen DSR-Prüfung werden die Probekörper in speziellen Vorrichtungen zwischen zwei Druckplatten eingespannt, sodass diese durch eine Öffnung im Deckel mithilfe eines Stempels im verformten Zustand zusätzlich verpresst werden können. Dies geschieht dann vor und nach einer durchgeführten Alterung bzw. Medieneinlagerung mithilfe einer Zugprüfmaschine jeweils bei Raumtemperatur. Dabei werden die verpressten Probekörper zusätzlich um 0,1 mm verformt. Diese dazu erforderlichen Kräfte stellen dann die Messwerte dar. Die diskontinuierliche DSR erfordert damit keinen hohen apparativen Aufwand, die Messergebnisse sind aber stark von der Sorgfalt des/r Prüfenden abhängig. Zudem ist dieses Verfahren nur nach dem Verfahren B möglich. Die DSR wird auch teilweise in Medien gemessen (z.B. in Ölen oder Kühlflüssigkeiten). Erfolgt dies oberhalb des Siedepunktes der Medien, kann es nur mittels diskontinuierlicher DSR durchgeführt werden. Unterhalb des Siedepunktes wird aufgrund der besseren Reproduzierbarkeit die kontinuierliche Prüfmethode bevorzugt angewendet.
Wichtigste Prüfnormen: Die ursprüngliche DIN 53537 zur DSR wurde im Jahr 2004 durch die ISO 3384 ersetzt. DSR-Prüfungen erfolgen heutzutage fast ausschließlich nach der (DIN) ISO 3384-1 [1]. Die Entsprechung aus dem USamerikanischen Normenkreis ist die ASTM D 6147: 1997 [2]. In seltenen Fällen wird auch eine DSR-Prüfung nach der SAE J2979 (2012- 05) [3] gefordert. Diese Prüfvorschrift versteht sich als eine Ergänzung zu den beiden oben genannten Normen.
Interpretation der Messergebnisse bzw. Bewertung des Verfahrens: Der Verlust der Dichtkraft durch Alterungseinwirkung zeigt an, wieviel elastisches Rückstellpotenzial noch vorhanden ist, und kann damit als Gradmesser der Alterung herangezogen werden, vergleichbar zum Druckverformungsrestverhalten (Verfahren A). Bei der Prüfung nach dem Verfahren B ist sehr gut zu erkennen, wieviel von der ursprünglichen Dichtkraft am Ende – nach Abkühlung auf Raumtemperatur – für die Anwendung noch übrigbleibt. Allerdings muss bei der Interpretation beachtet werden, dass ein kompletter Verlust der Dichtkraft nicht zwingend eine Leckage bedeutet. Für konservative Lebensdauerabschätzungen von Dichtungswerkstoffen sind Lebensdauerkriterien von 50 % bis 90 % Verlust der Dichtkraft üblich. Besonders wertvoll ist dieses Verfahren für Elastomerdichtungen, die im Krafthauptschluss eingesetzt werden, weil dort zum Abdichten noch eine erhebliche Restkraft erforderlich ist, was mit einer Druckverformungsrestprüfung nicht abgebildet werden kann.
Zukunft des Verfahrens: Es ist zu erwarten, dass die DSR als Instrument zur Prüfung im Bereich der Werkstoffentwicklung weiter an Bedeutung gewinnen wird, weil damit die Veränderungen im Werkstoff (Abfall der Rückstellkraft) kontinuierlich dargestellt werden können und weil ohne Änderung der Verformung der Alterungsgrad des Werkstoffes über die Zeit beschrieben werden kann. Mit diesen Informationen ist das Verhalten eines Gummiwerkstoffes einfacher als mithilfe der FEA zu modellieren.
Praktische Hinweise für eine Auftragsvergabe: Geprüft wird mit Probekörpern wie dem Druckknopf B beim DVR, also mit einem Durchmesser von ca. 13 mm und einer Höhe von ca. 6 mm. Das Schichten von 2 mm starken Probekörpern ist im Gegensatz zur DVR-Prüfung wegen der Rutschgefahr unbedingt zuvermeiden. Das Labor benötigt also 6 mm starke Prüfplatten, aus welchen die Probekörper ausgestanzt werden können. Die Standarddurchlaufzeit im Labor (Ankunft der Probekörper bis Versand des Ergebnisberichts an den Kunden) beträgt ca. zwei Wochen zzgl. der vorgegebenen Prüfzeit.
Literatur
[1] DIN ISO 3384-1: 2022-04: Elastomere oder thermoplastische Elastomere – Bestimmung der Spannungsrelaxation unter Druck – Teil 1: Prüfung bei konstanter Temperatur (ISO 3384-1:2019)
[2] ASTM D 6147:1997 (reapproved 2020): Standard Test Method for Vulcanized Rubber and Thermoplastic Elastomer-Determination of Force Decay (Stress Relaxation) in Compression
[3] SAE J2979 MAY2012: Test Method for Vulcanized Rubber and Thermoplastic Elastomer Determination of Compressive Stress Relaxation (CSR) Response
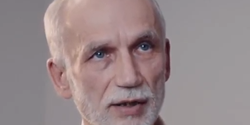
„Die Prüfung der Druckspannungsrelaxation ist „State of the Art“ für die Darstellung des Langzeitverhaltens einer Gummirezeptur für Dichtungen.“ Bernhard Richter, Geschäftsführer, O-Ring Prüflabor Richter GmbH