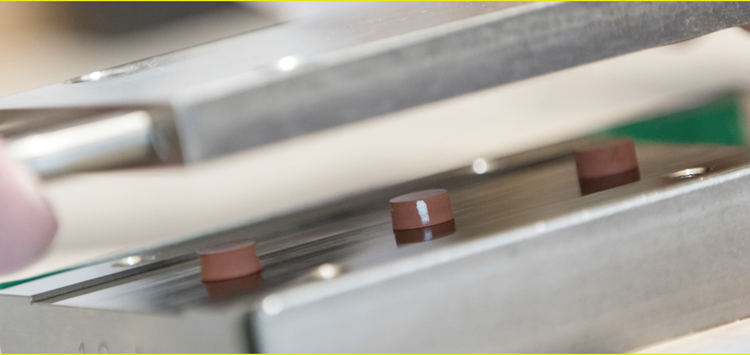
(Bild: O-Ring Prüflabor Richter GmbH)
08.06.2022 Prüfverfahren praxisgerecht anwenden – Teil 2a
Druck- und Zugverformungsrestprüfung (DVR/ZVR) in Luft und Medien – eine einfache Prüfmethode mit hoher Aussagekraft
Ohne die richtigen Mess- und Prüfverfahren sind Entwicklungen im Bereich der Dichtungstechnik schwierig oder unnötig teuer. Diese Serie zeigt, wie man anhand klassischer und innovativer Verfahren zu relevanten und/oder hilfreichen Daten kommt.
Neben der Härte- und Dichtemessung ist die Prüfung des Druck- bzw. Zugverformungsrestes ein wichtiger Baustein einer Wareneingangsprüfung, da sie Auskunft über die Verarbeitungsqualität eines Elastomerbauteiles gibt. Darüber hinaus kann diese Methode dem Anwender noch einige andere Fragen beantworten.
Das Verfahren in Kürze: Es ist allgemein bekannt, dass eine Dichtung nach einer langen Belastung dazu neigt „sitzen zu bleiben“, d.h. einer Spaltänderung nicht mehr in vollem Maße folgen zu können. Leckagen bzw. Dichtungsausfall sind eine häufige Folge. Will man den Verlust des Rückstellvermögens bzw. des Spaltüberbrückungsvermögen eines Werkstoffes oder einer Dichtung in Abhängigkeit der Temperatur und der Zeit ermitteln, ist die Druckverformungsrest-Prüfung die einfachste und am häufigsten angewendete Methode. Bei dieser Prüfung werden ein Normprobekörper oder ein Fertigteil i.d.R. um 25% verpresst und dann im verpressten Zustand über einen bestimmten Zeitraum (24 h bis zu mehreren Wochen) in Luft oder Flüssigkeiten bei erhöhter Temperatur gealtert. Nach Aufhebung der Verpressung wird gemessen, wie weit sich der Probekörper wieder in seine ursprüngliche Höhe rückverformt. So bekommt man eine direkte Aussage über das verlorene Rückstellvermögen der Probe – absolut (in mm) sowie relativ (in % der Verformung).
Der Zugverformungsrest wird u.a. für Fertigteile verwendet, wenn dies geometriebedingt eine bessere Messbarkeit im Vergleich zur Druckverformungsrestprüfung ergibt. So werden bspw. Lippendichtungen über einen Dorn gedehnt, dann in Heißluft oder Medien gealtert und schließlich wird gemessen, inwieweit sich diese wieder rückverformen.
Wichtigste Prüfnormen: Die am häufigsten angewandte Norm für den DVR bei erhöhten Temperaturen ist die ISO 815-1, welche große Ähnlichkeiten zur ASTM D395 aufweist. Für den ZVR kommen die ISO 2285, die ASTM D412 (chapter Determination of Tensile Test) und die ASTM D1414 (für Fertigteile: chapter Tension Set Test) zur Anwendung. [1]
Interpretation der Messergebnisse bzw. Bewertung des Verfahrens: Nach der ISO 815-1 wird der DVR wie folgt berechnet:
DVR= [(h0-h1)/(h0- hS)] × 100
Dabei sind:
- h0 = ursprüngliche Höhe des Probekörpers in mm
- h1 = Höhe des Probekörpers nach Entspannung in mm
- hs = Höhe des Abstandshalters zwischen den Prüfplatten = verpresste Höhe in mm
- DVR = Druckverformungsrest in %
Ein Druckverformungsrest von 0% bedeutet, dass es sich um einen idealelastischen Körper handelt, während 100% bedeuten, dass die Dichtung vollkommen „sitzen geblieben ist“. Es ist also keine Rückformung nach Entlastung erfolgt.
Mit der DVR-Prüfung können unterschiedliche Gummirezepturen gut miteinander verglichen werden. Die ISO 815-1 bietet die drei Verfahren A, B und C, welche sich u.a. in der Art der Abkühlung und Rückmessung unterscheiden.
Als Fertigteilprüfung hat sich der DVR besonders bewährt. Die DVR-Messung an Fertigteilen ist eine einfache Methode, Aussagen über die Verarbeitungsqualität (ausreichende Vulkanisation = guter DVR-Wert) zu erhalten.
Die DVR-Prüfung kann auch als Lebensdauernachweis eingesetzt werden. Ist das Lebensdauer-Temperaturkollektiv der Anwendung bekannt, lässt sich daraus über vereinfachte Arrheniusmultiplikatoren (Faustregel: 10 K Temperaturerhöhung = Verdoppelung der Reaktionsgeschwindigkeit der Alterung) eine isotherme Ersatzbeanspruchung (Zeit/Temperatur) ermitteln, nach welcher im Labor geprüft werden kann. Ist das nicht ausreichend genau, kann dies über eine DVR-Messung bei mindestens drei verschiedenen Prüfungen weiter verbessert werden.
Zukunft des Verfahrens: Bei der DVR-Prüfung handelt es sich um ein klassisches Standardprüfverfahren, das weit eingeführt ist und mit einem Minimum an Laborausstattung (DVR-Form, Umluftofen, Höhentaster) durchgeführt werden kann. In naher Zukunft sind keine Prüfverfahren erkennbar, die diese Methode voll umfänglich ersetzen werden. Dennoch gibt es Verfahren mit einer verbesserten Aussagekraft, wie z.B. die Druckspannungsrelaxation, welche im nächsten Teil der Serie behandelt wird.
Praktische Hinweise für eine Auftragsvergabe:
Wenn der Werkstoffkennwert einer Rezeptur geprüft werden soll, sollten Prüfplatten mit einer Stärke von 6 mm an das Labor gesandt werden, welches dann Normprobekörper daraus stanzen kann. In Ausnahmefällen können auch 2 mm dicke Prüfplatten dreifach geschichtet werden. Bei kleinen Fertigteilen werden mindestens drei Stück benötigt. Bei größeren Fertigteilen können drei Probestücke herausgeschnitten werden. Die Prüfung dauert je nach Vorgabe mindestens 24 h. Die Standarddurchlaufzeit im Labor (Ankunft der Probekörper bis Versand des Ergebnisberichts an den Kunden) beträgt ca. drei bis fünf Arbeitstage plus der vorgegebenen Prüfzeit.
Literatur
[1] Weitere Informationen – https://www.din.de/de/ueber-normen-und-standards
Alle Beiträge der Serie lesen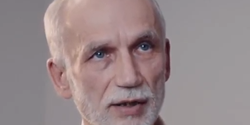
„Je mehr man sich mit dieser einfachen Prüfmethode befasst, desto hilfreichere Aussagen kann sie für die Praxis liefern.“ Bernhard Richter, Geschäftsführer, O-Ring Prüflabor Richter GmbH