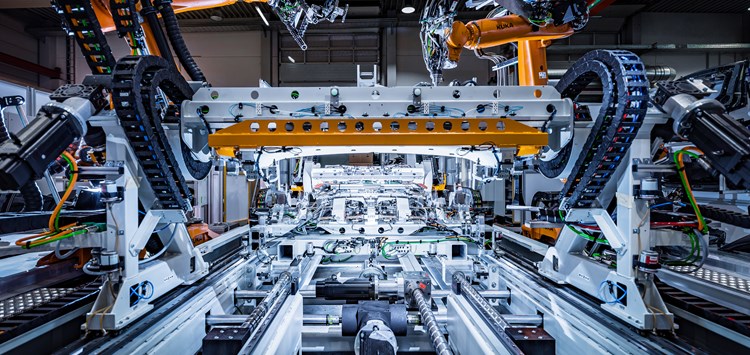
Für die Fügung der Heckklappe des VW ID.3 wurden drei vollautomatisierte Anlagen konstruiert. Diese beinhalten fünf Fügewerkzeuge, zwei siebenachsige Roboter, umfangreiche Werkzeug-Achssysteme sowie eine aufwändige Vor- und Nachbehandlung der Bauteile (Bild: RAMPF Production Systems)
21.03.2022 New Mobility nimmt Fahrt auf
Einschätzungen und Entwicklungen zur Entwicklung einer deutschen Schlüsselbranche
Bei einem derart umfassenden Wandel unserer Mobilität gibt es natürlich noch viele Unsicherheiten – doch eines wird sich vorerst nicht ändern: der Individualverkehr mit seinen hohen Stückzahlen. Und dieser wird elektrisch angetrieben, ob Hybrid, rein elektrisch oder via Brennstoffzelle.
Darüber hinaus werden immer mehr Assistenzsysteme eingesetzt – bis hin zum vollständig autonomen Fahren. Diesen Herausforderungen stellen sich die deutschen Automobilhersteller mit Erfolg, und gerade in der aktuell angespannten Liefersituation wird die Verlagerung von Produktionen ins nahe und ferne Ausland stärker hinterfragt. Folglich sehe ich großes Potenzial für den Standort Deutschland.
Im Pkw-Bereich, als einem Segment von New Mobility, stellen die Batteriepacks besondere Anforderungen hinsichtlich wärmeleitfähiger Materialien für das Verfüllen der Zellen sowie Abdichten der meist sehr großen Gehäuse. In diesem Bereich ist der Entwicklungsprozess voll im Gang – und das ist eine Chance für jene Lösungsanbieter, die die Entwicklungen eng begleiten und schnell auf neue Marktanforderungen reagieren. Ein Beispiel ist das Abdichten der Batteriewannendeckel: Diese sind bis zu 2mx1,5 m groß, meist aus Blech – und je nach Anforderung wird als Dichtung ein Polyurethan- oder Silikonschaum eingesetzt. Die Querschnitte der Dichtraupen variieren und die Haftung auf dem Trägermaterial muss i.d.R. durch entsprechende Vorbehandlungen wie Plasma oder Primer erzeugt werden. Nach anfänglichen Unsicherheiten über die jährlichen Stückzahlen ist inzwischen klar, dass die geplanten Mengen nur mit vollumfänglichen Automatisierungssystemen realisiert werden können. Unser Fokus liegt folglich auf der Entwicklung von Gesamtanlagenkonzepten zur Montage der Batteriepacks mit unterschiedlichen Einzelschritten wie Handling, Kleb-, Verguss- und Dichtschaumapplikationen sowie Fügen, Montieren und Prüfen.
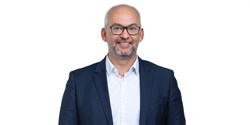
„Gesamtanlagenkonzepte mit hohem Automatisierungsgrad werden auch für Fertigungen in Deutschland und Europa zunehmend nachgefragt.“ Alexander Huttenlocher, Director of Sales & Marketing, RAMPF Production Systems