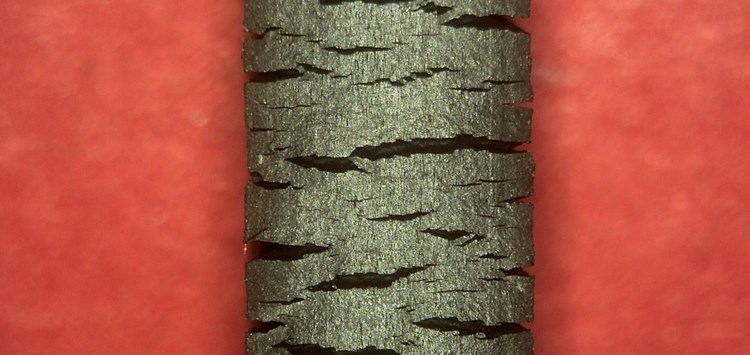
Risse nach einer Ozonprüfung an einem Abschnitt eines neuen Referenzmusters (Serienzustand) (Bild: O-Ring Prüflabor Richter GmbH)
31.10.2017 Integraler Ansatz
Der beste Weg zur wirklichen Ausfallursache
Dichtungsausfälle verursachen jedes Jahr durch direkte und indirekte Folgekos-ten sicherlich zwei- bis dreistellige Millionenbeträge an volkswirtschaftlichem Schaden – sei es durch Maschinenstillstandskosten, durch Rückrufaktionen oder Umweltschäden. Noch schlimmer als der direkte Schaden können die daraus erwachsenden Imageprobleme am Markt für die betroffenen Unternehmen werden.
Daher ist es natürlich sehr wichtig, bei Schadensfällen die wirkliche Ursache für den Ausfall schnell zu erkennen, um den Fehler auch abstellen zu können. Die Durchführung einer Schadensanalyse wird allerdings oft nur auf eine werkstoffliche Untersuchung des Schadensmusters zusammen mit einer mikroskopischen, eventuell auch mit einer rasterelektronenmikroskopischen Untersuchung bzw. einer anderen analytischen Prüfung reduziert. Solche Untersuchungen allein können aber leicht in die Irre führen, da sich an ausgefallenen Gummidichtungen fast immer werkstoffliche Inhomogenitäten, Fremdstoffe, Spuren einer stattgefundenen Alterung und leichte herstellungsbedingte Mängel finden lassen. Die „Kunst“ besteht nun darin, die vorhandenen Spuren richtig zu interpretieren. Das ist letztlich aber nur mit einem integralen Ansatz möglich, das heißt, man muss alle verfügbaren Information zum Schadensfall in die Bewertung des Schadensbildes mit einbinden, damit die Logik des Ausfalls auch klar zu erkennen ist.
Wie bei vielen komplexen Aufgabenstellungen hilft auch bei der Schadensanalyse eine systematische Vorgehensweise. Auf Basis von mehr als 2.000 durchgeführten Untersuchungen entstand eine Systematik – die 5 Schritte einer belastbaren Schadensanalyse, die sich in der Praxis bewährt hat:
1. Schritt: Identifikation der Probe
Dieser besteht darin, das (hoffentlich auch) vorliegende Schadensmuster dahingehend zu untersuchen, ob dieses bezüglich Werkstoff den Vorgaben entspricht. Als einfachste Identitätsprüfung kann die Härte und Dichteprüfung erste Klarheit verschaffen (Übereinstimmung mit der Bestellvorschrift bzw. den Lieferantenangaben), darüber hinaus kann man sich ggf. mit einer FTIR-Analyse absichern, ob auch das richtige Polymer (z.B. FKM oder EPDM) vorliegt. In ca. 1 bis 2% der Schadensfälle ist damit die Schadensanalyse abgeschlossen, wenn sich nämlich herausstellt, dass der falsche Werkstoff verwendet wurde. Es wird empfohlen, parallel zur Untersuchung des Schadensmusters ein aktuell verwendetes Serienmuster im Vergleich zum Schadensmuster zu untersuchen. Das zeigt einerseits schnell die stattgefundenen Veränderungen auf, zum anderen lassen sich dann im weiteren Verlauf der Untersuchung eventuell als Schadensursache angenommene Mängel in der Qualität überprüfen. Zur Identifikation der Probe gehört neben dem Werkstoff natürlich auch die Abmessung der Probe. Hier sollten die wesentlichen Funktionsmaße des Schadensmusters mit denen des Serienmusters verglichen werden. Bei O-Ringen z.B. die Schnurstärke und der Innendurchmesser, bei Lippendichtungen oder Radialwellendichtringen Innen- und Außendurchmesser.
Damit wird im ersten Schritt nachgewiesen, ob der richtige Werkstoff und die richtige Abmessung vorliegen und mögliche stattgefundene werkstoffliche und maßliche Veränderungen werden dokumentiert.