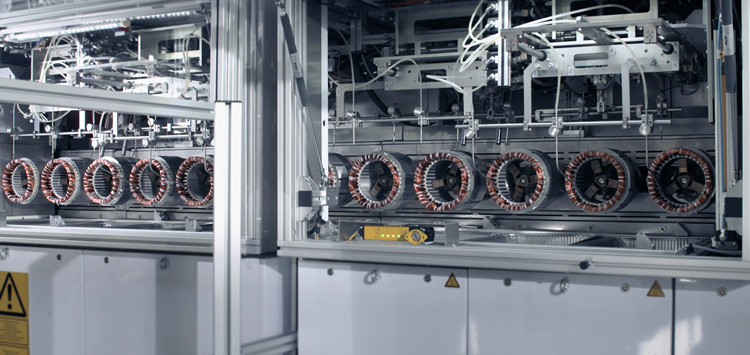
Moderne Imprägnieranlage (Bild: bdtronic GmbH)
17.11.2020 Elektromotoren effizient imprägnieren
Aus Prozesskombinationen weitere Vorteile ziehen
Das effiziente Imprägnieren von E-Motoren hat einen Einfluss auf die Langzeitnutzung der Fahrzeuge und damit auf die Akzeptanz der Technologie. Die Wahl des Verfahrens, der reibungslose Übergang vom Testcenter in die Serie und die Betrachtung des Imprägnierens im gesamten Produktionsprozess sind dabei zentrale Stellschrauben für eine hohe Effektivität.
Elektromobilität ist die Antriebstechnologie der Zukunft. Der Anteil an Elektroautos bei den EU-Neuzulassungen hat sich innerhalb eines Jahres verdreifacht. Während im August 2020 mehr als 16.000 E-Autos erstmals in Deutschland zugelassen wurden, waren es noch im August des Vorjahres lediglich 5.000 rein elektrische angetriebene Fahrzeuge. Diese rasante Entwicklung stellt die Automobilhersteller und ihre Zulieferer vor große Herausforderungen. In kürzester Zeit müssen Produktionslinien für die Serienfertigung neu aufgebaut werden, um die am Markt geforderten Stückzahlen liefern zu können. Die vorgegebenen Taktzeiten werden dabei immer kürzer.
Die Imprägniertechnologie wird bei der Produktion elektrischer Antriebe benötigt – sowohl für die Hybridtechnologie als auch für voll-elektrische Antriebe für Pkw und Lkw. Beim Imprägnieren werden die Hohlräume zwischen Drähten geschlossen und abgedichtet. Dies sorgt für bessere elektrische Isolierung und verhindert Vibrationen. Imprägnieren steigert die Wärmeleitfähigkeit und trägt zu einer besseren Umweltbilanz bei.
Die Entwicklung der Imprägniertechnologie
bdtronic baute bereits 2008 erste Imprägniersysteme für Automobilhersteller und Zulieferer für den europäischen und asiatischen Markt. Mit einer Taktzeit von 45 s pro Elektromotor und einem jährlichen Output von 500.000 Stück wurde 2017 die weltweit größte und schnellste Anlage an einen Elektroauto-Hersteller aus den USA geliefert und in Betrieb genommen. Diese Anlage gewann auf der Branchenleitmesse für E-Mobilität CWIEME Berlin den Global Award in der Kategorie „Produkt des Jahres“. Seitdem wurden pro Jahr zwischen zehn und fünfzehn Imprägnieranlagen an Automobilhersteller und -zulieferer geliefert. Dabei wurden die Prozessschritte ständig weiterentwickelt und verbessert.