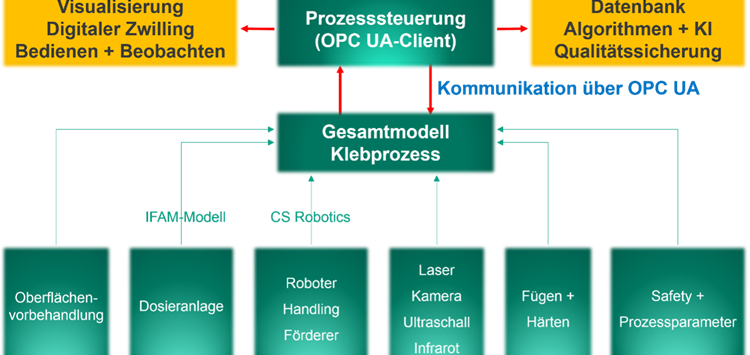
Bild 3: Zusammenarbeit zwischen OPCUA-Server und zentralem OPCUA-Client (Bild: Fraunhofer IFAM)
11.03.2025 Digitale Transformation: die Modellierung von Klebprozessen ist ein zentraler Aspekt
Die Digitalisierung von Klebprozessen (Bild 1) ist nicht mehr nur ein Zukunftsthema, sondern eine konkrete Realität, die zunehmend das industrielle Umfeld prägt.
Dabei geht es nicht nur um vollautomatisierte Klebprozesse in hochmodernen Fertigungsanlagen, wie sie z.B. in der Automobilproduktion zu finden sind, sondern auch um die Teildigitalisierung von manuell oder teilautomatisiert ausgeführten Prozessen. Als entscheidender Fortschritt haben sich dabei kostengünstige Sensoren und Aktoren erwiesen, die eine intelligente Integration in bestehende Systeme ermöglichen. In der Vergangenheit waren universelle Austauschformate nur über Bussysteme wie „Profinet“ zugänglich. Mittlerweile ermöglichen universelle Kommunikationsstandards wie OPCUA oder MQTT eine einfache und effiziente Vernetzung zwischen Maschinen und den zugehörigen Bedienenden.
Ein entscheidender Schritt für die weitere Digitalisierung der Klebprozesse ist die Einführung eines durchgängigen Gesamtmodells, das alle Material- und Prozessdaten in einem digitalen Rahmen zusammenführt. Für eine reibungslose Kommunikation zwischen den verschiedenen Maschinen und Geräten ist es notwendig, standardisierte Datenmodelle auf Basis des Kommunikationsstandards
OPC UA zu entwickeln. Im Rahmen des Projekts „Kleben 4.0“ und dessen Nachfolgeprojekts „DigiKleb“ wurde ein OPC UA-Datenmodell für Dosiersysteme entwickelt, das alle Parameter und Funktionen eines Dosiersystems umfasst (Bild 2). Diese Datenmodelle werden nun um die Bereiche Sensorik, Aktorik und Qualitätssicherung erweitert, sodass eine vollständige digitale Abbildung der gesamten Klebprozesskette entsteht (Bild 3).
In der Praxis fungieren die Geräte der Feldebene als OPCUA-Server, die alle relevanten Prozessdaten zur Verfügung stellen. Ein zentraler OPCUA-Client übernimmt die Kommunikation zwischen den Maschinen und sorgt für den Datenfluss innerhalb des Gesamtsystems. Dabei werden nur die für die interne Kommunikation notwendigen Parameter übertragen, um den Datenverkehr zu minimieren. Übergeordnete Systeme wie SCADA oder MES können sich der kompletten Prozessdaten zur Analyse bedienen. Darüber hinaus ermöglichen diese Modelle eine einfache Archivierung in Zeitreihen-Datenbanken und die Auswertung der Daten mittels Algorithmen und stochastischen Methoden, die zur Qualitätssicherung und Dokumentation des Prozesses genutzt werden. Visualisierungen in Form von digitalen Zwillingen (virtuelle 3D-Mockups) und interaktiven Bedienerschnittstellen (HMI) ermöglichen die Überwachung und Steuerung der aktuellen Prozessparameter in Echtzeit.
Ein Arbeitspaket im Projekt „DigiKleb“ beschäftigt sich mit der generischen Beschreibung von klebtechnischen Prozessketten. Hier werden die verschiedenen Produktionsprozesse in der Automobilfertigung kategorisiert und standardisiert. Weitere Arbeitspakete befassen sich mit der Erarbeitung konkreter Anwendungsfälle und der Entwicklung von Variablen und Datenmodellen, die eine umfassende Datenbasis für den gesamten Klebprozess bilden. In späteren Phasen wird die Prozessüberwachung optimiert, indem Abweichungen von Sollwerten erfasst werden, um eine effiziente Prozessführung und Fehlerbehebung zu gewährleisten.
Diese Entwicklungen markieren einen wichtigen Schritt in der Weiterentwicklung der Klebtechnik und ihrer digitalen Transformation. Die Möglichkeiten zur Effizienzsteigerung und Optimierung der Produktionsqualität durch den Einsatz digitaler Zwillinge und die umfassende Vernetzung der Produktionssysteme sind enorm.
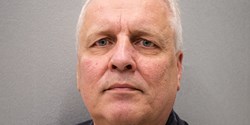
„In den kommenden Jahren werden diese Technologien die Industrie revolutionieren und neue Standards in der Qualitätssicherung und Produktionsplanung setzen.“ Frank Mohr, DVS®-EWF-European Adhesive Engineer, Fraunhofer IFAM