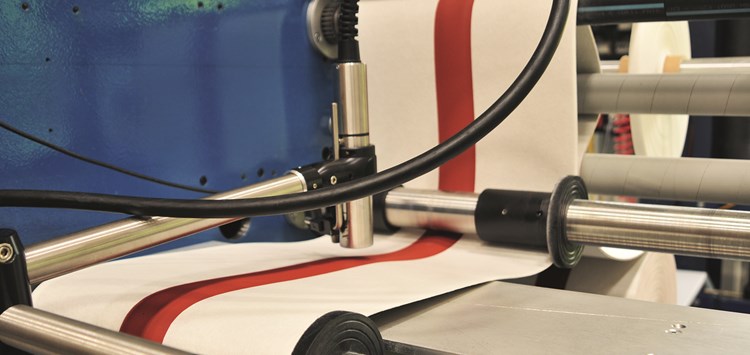
Fertigung von Elastomerfolien für die Prozessindustrie (Bild: Tec-Joint AG)
04.06.2018 Der schmale Grat
Wirtschaftliche Dichtungslösungen aus Elastomerplatten und -folien
Mit den wachsenden Anforderungen in der Chemie, Lebensmittelverarbeitung und Pharmaindustrie können für Dichtungslösungen immer weniger Standardelastomere eingesetzt werden. Das ist allerdings kein allzu großes Problem, da sich Anbieter auf diesen Lösungsbedarf eingestellt haben.
Steigende Anforderungen sind ein Thema, das heute quer durch alle Branchen gilt. Für Lösungssuchende in den Prozessindustrien kommt erschwerend hinzu, dass der Mengenbedarf an Material für Dichtungen beileibe nicht mit dem anderer Branchen, z.B. der Automobilindustrie, vergleichbar ist. Dies führt zwangsläufig zu einem eingeschränkten Angebot an Lösungsanbietern und somit geeigneten Lieferanten, die nur schwer zu finden sind. Dazu kommt, dass einerseits der Aufwand für die optimale Lösung der gleiche ist wie der für Großprojekte, andererseits die Kosten nicht explodieren dürfen. Die Tec Joint AG hat sich auf diesen schmalen Grat spezialisiert und analysiert bei jedem Projekt die Einsatzbedingungen sorgfältig und erarbeitet dann in enger Zusammenarbeit mit den Kunden passgenaue Lösungen. Eine Lösung auf Basis der Rohstoffgruppe EPDM (Ethylen-Propylen-Dien-Kautschuk) verdeutlicht die Vorgehensweise.
Wenn Standard keine Lösung ist
EPDM ist nicht gleich EPDM und Dichtungen und Folien aus diesem Werkstoff können sich je nach Einsatzbedingungen sehr unterschiedlich verhalten. So haben handelsübliche EPDM einen Ethylengehalt zwischen 45 und 75 Gew.%, wobei die Polymere mit einem Ethylengehalt von 45 bis 55% die beste Kälteflexibilität und gute kautschuktechnologische Eigenschaften haben. Bei Kautschuktypen mit höherem Ethylengehalt nimmt der Druckverformungsrest in Kälte zu. Ein höherer Dien-Gehalt bewirkt eine höhere Vernetzungsgeschwindigkeit, Vernetzungsdichte und Festigkeit sowie eine geringere bleibende Verformung. Die Alterungs-, Witterungs-, und Ozonbeständigkeit nimmt dagegen mit steigendem Diengehalt ab.
EPDM kann sowohl mit Schwefel als auch peroxidisch vernetzt werden. Bei peroxidischer Vernetzung muss der Ethylengehalt mindestens 60 Gew.% betragen. Üblicherweise ist EPDM bei Temperaturen von -40 bis +135 °C, kurzfristig bis 170 °C einsetzbar, per-
oxidische Vernetzungen können bis ca. 150 °C belastet werden. Allein diese „Variablen“ zeigen die Notwendigkeit der Feinabstimmung für den Einsatzfall.
Was zeichnet EPDM für die Prozessindustrie aus? Das sind zunächst seine hervorragende Beständigkeit gegen Wärme, Ozon, Sauerstoff und andere atmosphärische Einflüsse und damit die ausgezeichnete Beständigkeit gegen Alterung. Er ist gut beständig gegen Wasser, verdünnte Säuren, Laugen, Alkalien und Alkohole, Ketone, Glykole und besitzt sehr gute elektrische Isoliereigenschaften. Er hat eine sehr geringe Wasseraufnahme und gute Dampfbeständigkeit, eine hohe Elastizität und gute Kälteflexibilität, ist aber unbeständig gegen Fette, Mineralöle, Kraftstoffe, Kohlenwasserstoffe. Ist dieses Leistungsprofil nicht mit den Anforderungen kompatibel, haben sich in der Praxis z. B. Lösungen auf Basis von FKM- oder FFKM-Werkstoffen bewährt.
Die relevanten Normen erfüllen
Die Erfüllung der relevanten Normen ist in der Prozessindustrie ein zentrales Thema. Da ist es teilweise hilfreich, mit Spezialisten zusammenzuarbeiten, die die teils undurchsichtige Normenlage in Kombination mit dem Stand der Technik in Materiallösungen übertragen können. Das geht auch zunehmend über klassische Standardanfragen hinaus. In einem konkreten Fall für die Prozessindustrie wurden z.B. in enger Zusammenarbeit mit Mischereien spezielle Mischungen erarbeitet, die zahlreichen internationalen Normen entsprechen mussten. Da die Dichtungen in der Trinkwasseraufbereitung eingesetzt werden sollten, waren EN 681-1, D KTW D1 und D2 bzw. neu UBA* Elastomerleitlinie, D DVGW W-270, F ACS -NF XP P 41-250-1/-2/-3, GB WRC BS 6920 (WRAS), A Ö-Norm B5014-1 D und E und die USA NSF ANSI 61 Konformität zu erfüllen.
Bei einem anderen Projekt musste eine EPDM-Mischung die Brandschutzklassen EN 45545-2, D DIN 5510-2, F NFF 16-101 (Grille 6), USA ASTM C1166 (C542), USA ASTM 662, GB, CH BS 6853, Table7, VKF-Brandkennziffer, USA Bombardier SMP 800-C, E UNE 23-773, I UNI CEI 11170 erfüllen.
Bei einem weiteren Projekt wurde eine Mischung benötigt, die nach PK Klasse 1 zertifiziert ist. In einigen Fällen müssen – bedingt durch die Einsatzbedingungen – die Elastomerplatten bzw. -folien zusätzlich mit PEEK oder PTFE beschichtet werden. Soll ein unterschiedliches Zug- oder Druckverhalten erzeugt werden, beschichtet man z.B. PES-, Polyamid-, Glas-, Aramidgewebe mit den betriebsbedingt notwendigen Elastomeren. Zudem realisiert man auch Verbindungen mit Stahl- und Aluminiumgeflechten.
Fazit
Diese Beispiele zeigen, dass, wenn Standards keine Lösung bieten, Partner hilfreich sind, die – basierend auf jahrzehntelanger Erfahrung – Lösungen für die vielfältigen Anforderungen in der Prozessindustrie haben oder entwickeln.
Fakten für Konstrukteure
• Bei schwierigen Rahmenbedingungen und vielen zu erfüllenden Normen – jenseits des Standards – lohnt sich der frühe Kontakt mit Experten
Fakten für Einkäufer
• Auch jenseits des Standards und bei nicht so großen Abnahmemengen lassen sich heute wirtschaftliche Lösungen realieren
Fakten für Qualitätsmanager
• Mit modernen Elastomerplatten und -folien lassen sich heute Dichtungslösungen realisieren, die ein breites Normenspektum abdecken