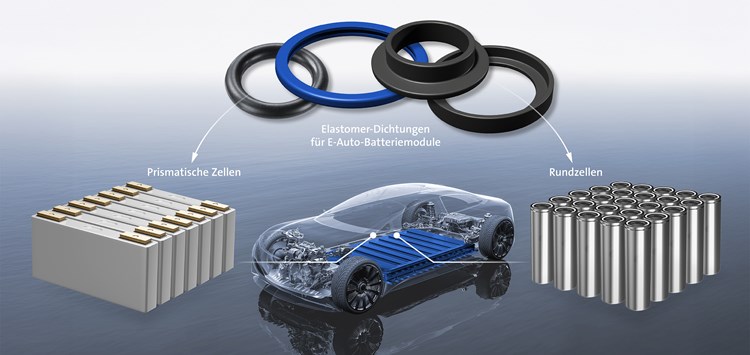
Der neue Werkstoff bietet gegenüber Thermoplasten relevante Vorteile im Fall eines Thermal Runaway (Bild: Freudenberg Sealing Technologies)
10.04.2025 Neues Dichtungsmaterial für sichere Batteriezellen
Mit einem optimierten Dichtungswerkstoff bietet Freudenberg eine Alternative zu PFAS-haltigen Thermoplast- und FKM-Dichtungen für den Einsatz in der E-Mobilität. Die neue Materialreihe wird im Spritzgießverfahren verarbeitet, bietet eine höhere Dichtungsleistung, stellt die Batterielebensdauer sicher und erfüllt steigende Umweltauflagen.
Bei den traditionell für Batteriedichtungen eingesetzten Thermoplasten ist die langkettige Molekülstruktur der Makromoleküle untereinander nicht chemisch vernetzt, sondern nur über schwache zwischenmolekulare Kräfte miteinander verbunden. Zwar lassen sich Thermoplaste ein Stück weit elastisch verformen, jedoch erfahren sie beim kontinuierlichen Laden und Entladen der Batteriezelle auch einen funktionsrelevanten Anteil an plastischer Verformung. Anders die Elastomere, deren Molekülketten chemisch miteinander vernetzt sind. Im Grundzustand liegen die Polymerketten in einem Knäuel vor, das bei Zug- und Druckbelastungen gezogen oder gestaucht wird. Aufgrund der Entropieelastizität reagieren diese vernetzten Werkstoffe elastisch-reversibel und halten während der zyklischen Volumenänderung der Batteriezellen unter Last herausragend ihre Form.
O-Ringe aus dem neuen Elastomer verhindern somit, dass Elektrolyt aus der Batteriezelle austritt oder Verunreinigungen in die Zelle eintreten. Eine Batteriezelle lässt sich nicht als ein steifes Konstrukt vorstellen – sie „atmet“. Wenn die Batteriezelle einen Temperaturanstieg von der Umgebungstemperatur auf Bereiche von i.d.R. bis zu 60°C durchläuft, dehnt sie sich aus und zieht sich beim Abkühlen gleichermaßen zusammen. Elastomere zeigen bei dieser Dauerbelastung wesentliche Vorteile gegenüber Thermoplasten.
Bei der Entwicklung neuer Werkstoffe für Batterieanwendungen steht neben ökonomischen Aspekten die Nachhaltigkeit im Fokus. Grundsätzlich werden elektrische Fahrzeuge umso nachhaltiger, je länger die Batterie genutzt werden kann. Hierzu leistet das neue Dichtungsmaterial einen Beitrag. So konnte beim Einsatz des neuen Werkstoffes in Kundenprojekten die Performance-relevante Leckagerate der Batteriezellen um eine Größenordnung verbessert werden, also um das Zehnfache gegenüber konventionellen Thermoplast-Dichtungen.
Ein weiterer essenzieller Aspekt ist, dass die Elektrochemie der Batteriezellen äußerst empfindlich auf potenzielle Verunreinigungen reagiert. Ein verfrühter Kapazitätsverlust, der bei einer mit herkömmlichen Elastomeren gedichteten Zelle beobachtet wird, kann aus den minimalen, aber dennoch vorhandenen Verunreinigungen des Dichtungsmaterials resultieren. Einen ähnlichen Effekt hat ein Feuchtigkeitseintrag in die Zelle, da er eine Zersetzung von Elektrolytkomponenten herbeiführen kann. Diese Aspekte wurden in der Entwicklung des neuen Werkstoffes berücksichtigt. Darüber hinaus hat die Verfahrenstechnik die Herstellungsprozesse dahingehend optimiert, dass diese Batterie-Zell-Dichtungen in Großserie produziert werden können.