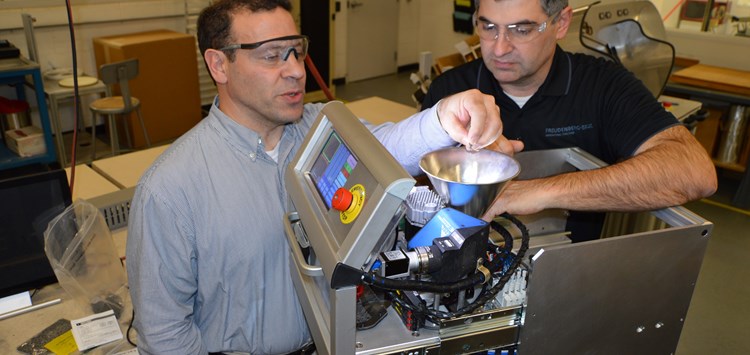
Neue Anlage zur automatischen Sichtkontrolle (Bild: Freudenberg Sealing Technologies GmbH & Co. KG)
14.08.2019 Neue Wege bei der Qualitätsprüfung
Beim Qualitätscheck sehr kleiner Teile setzt Freudenberg Sealing Technologies mit einer neuen Anlage zur automatischen Sichtkontrolle, die eine selbst entwickelte Technologie für die optische Prüfung mit den Vorteilen der additiven Fertigung kombiniert, neue Maßstäbe.
Die neue Inspektionseinheit ist gerade einmal so groß ist wie eine haushaltsübliche Mikrowelle: Sie prüft pro Sekunde vier Schlauchfedern mit einem Durchmesser von 6 bis 12 mm auf Fehler wie Knicke, Lücken, abweichende Durchmesser und mangelhaft geschlossene Enden. Die Maschine sortiert automatisch defekte Teile aus einer typischen Charge von 10.000 Federn aus und verpackt und etikettiert den Rest für den Versand an den Kunden. Eine einzelne Feder kostet nur wenige Cent. Dennoch hat die erste Inspektionseinheit im Freudenberg-Werk in Bristol (USA) bereits spürbar zur Kostensenkung beigetragen: Die Ausschussquote ging ebenso zurück wie Abweichungen beim Prüfprozess und die Produktionszeit. Für die Mitarbeiter haben sich die Arbeitsbedingungen deutlich verbessert. Bevor die Inspektionseinheit installiert wurde, mussten die Mitarbeiter Tausende der winzigen Federn auf dem Leuchttisch mithilfe einer Lupe visuell prüfen. Stellten sie dabei eine bestimmte Anzahl von fehlerhaften Teilen in einem Fertigungslos fest, musste die gesamte Charge verschrottet werden.
Dank der neuen Prüfanlage sind teure Kundenrückrufe deutlich zurückgegangen. Während die Einheit Fehler identifiziert und analysiert, meldet die zugehörige Software diese Informationen direkt an die Fertigungsmaschine zurück. Werden zu viele Fehler erkannt, stoppt die Inspektionseinheit die Fertigung automatisch, sodass die Maschinenparameter korrigiert und mögliche weitere Probleme behoben werden können. Gleichzeitig mit den Inspektionseinheiten entwickelte man ein Dashboard zur Erfassung der Daten. Der Bediener kann auf einem Bildschirm sehen, welche Maschinen korrekt funktionieren und wo Anpassungen notwendig sind. Herzstück ist das selbst entwickelte flexible Bildverarbeitungssystem. Es untersucht ein Bauteil mit einer Reihe von Algorithmen in < 50 ms auf Fehler – die neue automatische Sichtkontrolle (ASK) prüft acht verschiedene Maß- und Oberflächenfehler. Bei der Prototyp-Entwicklung der Inspektionseinheit musste eine umfangreiche Anforderungsliste aus der Fertigung abgearbeitet werden. So sollte die Einheit klein und kompakt sein, damit sie unter die Produktionsmaschinen passt. Außerdem musste sie netzwerkfähig sein, damit die Bediener das System sowohl auf einem großen Bildschirm an der Anlage als auch auf ihren Smartphones überwachen können. Ebenso sollte das elektronische Dashboard integriert werden, mit dem sich Statistiken und Daten anzeigen lassen. Nicht zuletzt war auch eine mechanische Ausschleusung erforderlich, die die Produkte schnell und reibungslos durch den Inspektionsprozess in separate Behälter steuert. Die auf Basis dieser Anforderungen entwickelte Ausschleusung besteht aus komplexen Führungen und extrem dünnen Teilen, um die winzigen Teile problemlos durch den Inspektionsprozess zu bewegen. Um perfekte Ergebnisse zu erzielen, griff man auf die additive Fertigung zurück. Da die Entwicklung dieser kleinen Inline-Federinspektionseinheit so erfolgreich war, sollen nun größere Prüfeinheiten für den Einsatz in anderen Fertigungsbereichen folgen. Hierzu will Freudenberg ebenfalls das flexible Bildverarbeitungssystem und additiv gefertigte Komponenten nutzen.