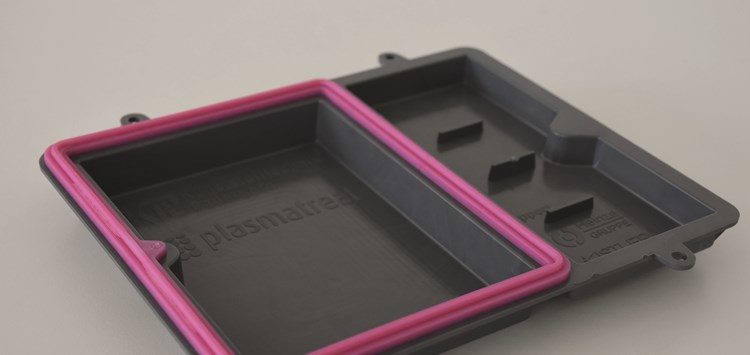
Bessere Verbundhaftung mit neuer Oberflächenbehandlung (Bild: Plasmatreat GmbH)
21.10.2019 Mediendichte Metall-Kunststoff-Verbindungen
Die Plasma-SealTight®-Oberflächenbehandlung von Plasmatreat ermöglicht eine wesentlich stärkere Verbundhaftung zwischen Kunststoffcompound und Metallen als herkömmliche Verfahren.
Mit der innovativen Technologie ist die Produktion mediendichter, haftungsstarker Hybrid-Bauteile innerhalb einer Spritzgusslinie möglich. Die Verbundfestigkeit von Kunststoff und Metall ist aber nicht der einzige Vorteil der Technologie, die Plasmatreat gemeinsam mit dem Kunststoff-Compound-Hersteller AKRO-PLASTIC GmbH entwickelt hat. Ein weiterer Pluspunkt ist die Tatsache, dass sich das Verfahren ganz einfach in bestehende Spritzgusslinien integrieren lässt. Das Verfahren trägt darüber hinaus auch zur Kostensenkung bei, denn teure und umweltschädigende Primer werden nicht mehr benötigt. Das Beschichtungsverfahren eignet sich nicht nur zur Fertigung mediendichter Stecker, sondern auch zur Herstellung hybrider Bauteile mit hohen Anforderungen an die Mechanik, wie z.B. hinterspritzte Embleme oder Strukturbauteile. Die beim Plasma-SealTight® Verfahren erzielten Zugscherfestigkeiten erreichen Werte von über 50 MPa, während Standard-Verfahren lediglich Werte von maximal 20 MPa aufweisen.
Auf der K Messe 2019 demonstrierte man die Wirksamkeit des Verfahrens an der Fertigung eines zweireihigen Steckers. Dabei wurden Vorspritzlinge mit jeweils drei Kontakten am ARBURG-Stand aus CuSn6-Stanzgittern hergestellt, in Magazinen zu einer Fertigungszelle am Plasmatreat-Stand geliefert und dort weiterverarbeitet. Ein Handling-Roboter nahm den ersten Vorspritzling aus dem Magazin und platzierte ihn unter eine Openair-Plasma®-Düse, die eine Feinstreinigung durchführte. Im Anschluss führte der Handling-Roboter den Vorspritzling unter eine PlasmaPlus®-Düse: Hier wurde der Vorspritzling mit einer Plasma-SealTight®-Beschichtung versehen. Der gereinigte und beschichtete Vorspritzling wurde dann in eine Vorrichtung zur Vormontage der Kontakte abgelegt. Nun wurde der Prozess aus Feinstreinigung und Beschichtung mit einem weiteren Vorspritzling wiederholt. In der Vormontagestation wurden dann der erste und der zweite Vorspritzling vom Handling-Roboter montiert. Der Roboter entnahm anschließend den vormontierten, jetzt zweireihigen Vorspritzling aus der Montagestation und legte ihn in das Spritzgusswerkzeug ein. Die eingelegten Kontakte wurden durch eine im Spritzgusswerkzeug integrierte Induktionsheizung auf Prozesstemperatur erwärmt, bevor das Werkzeug zufuhr und der Spritzgussprozess startete. Nach Abschluss des Prozesses fuhr das Spritzgusswerkzeug auf und entformte den fertigen Stecker, der auf einem Förderband abgelegt wurde.