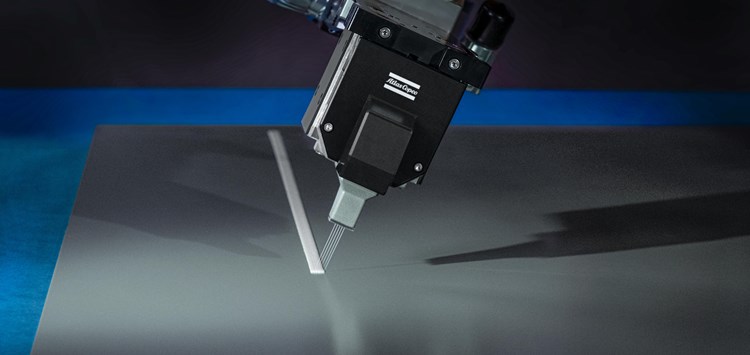
Die neu entwickelte Applikationstechnologie von Atlas Copco für Nahtabdichtungen im Karosseriebau. (Bild: Atlas Copco)
18.12.2019 Dichten wie gedruckt
Für die Abdichtung in der Lackiererei hat Atlas Copco die Applikationstechnologie IDDA.Seal entwickelt, bei dem einzelne PVC-Tropfen mit hoher Frequenz auf die abzudichtenden Bauteile aufgetragen werden.
Mit dem neuen Verfahren werden zahlreiche Probleme gelöst, die Anwender in der Automobilindustrie bislang mit bestimmten Nahtabdichtungen in der Lackiererei hatten. Denn mit IDDA.Seal (Intelligent Dynamic Drop Application) wird das PVC Punkt für Punkt statt mit konstantem Materialfluss aufgetragen. Jeder Punkt wird genau dort gesetzt, wo er hingehört. Konkret geht es um PVC-Plastisole, die im Automobilbau häufig für kosmetische Sichtnähte, Nahtabdichtungen oder den Unterbodenschutz verwendet werden. Das Material, das noch vor der Lackierung auf Schweißnähte oder Schnittkanten einer Karosserie aufgetragen wird, schützt vor Korrosion, verbessert die Fahrzeugakustik und dichtet den Innenraum ab. In der Regel hatte die Branche die Anwendungen mit konventioneller Technik gut im Griff. Aber durch immer komplexere Geometrien sind in den letzten Jahren ganz neue Herausforderungen aufgetaucht. Bisher setzen die meisten Automobilhersteller in den Lackierstraßen für kosmetische Nähte und die Nahtabdichtung die Dünnstrahl-, die Swirl- oder die Flatstream-Technologie ein. Dabei muss die Düse rechtwinklig zum Bauteil stehen, um einen optimalen Auftrag zu erreichen. Der Applikationsabstand zwischen Düse und Bauteil beträgt nur wenige Millimeter, was bereits einige Einschränkungen mit sich bringt. Denn nicht alle Stellen sind mit dem Roboter gut zu erreichen. Außerdem ist es bei einem automatisierten Auftrag, insbesondere bei hohen Robotergeschwindigkeiten, schwierig, eine definierte Höhe der PVC-Naht beizubehalten. Mit der bisherigen Applikationstechnologie kann es zu Materialanhäufungen an den Wendestellen kommen oder spitze Winkel werden nicht richtig erreicht. Das macht manuelle Nacharbeit erforderlich, um Undichtigkeiten zu vermeiden und überschüssiges Material zu verstreichen. Diese Punkte waren auch für einen Hersteller von Premium-Automobilen ein Thema. So entstand die Idee, für den Dichtstoffauftrag an komplexen Geometrien eine noch präzisere und flexiblere, automatisierte Technologie zu entwickeln. Ziel war es, insbesondere in der Feinnahtabdichtung, unzugängliche Stellen möglichst optimal automatisiert per Roboter abzudichten. So wollte der Entwicklungspartner Audi vor allem die Ergonomie für die Mitarbeiter verbessern, PVC-Material einsparen und Verschwendung vermeiden. Atlas Copco entwickelte daraufhin ein neues Verfahren für die Abdichtung in der Lackiererei, das in absehbarer Zeit auch anderen Herstellern zur Verfügung stehen wird. Das PVC wird in ultrafeinen Tropfen über fünf Nadeln aufgebracht, die einzeln angesteuert werden können. Dadurch lassen sich das Öffnen und Schließen der Nadeln, das Tropfenvolumen und der Tropfenabstand individuell einstellen und an die gewünschte Nahtgeometrie anpassen. Das erhöht die Flexibilität deutlich. Dafür wurde ein neuer Applikator entwickelt und die besseren Steuerungsmöglichkeiten auch über eine neue Software abgebildet. Klassische Steuerungen konnten dem Applikator bislang nur den Befehl zum pneumatischen Öffnen oder Schließen erteilen. Ein robotergeführter Applikator trägt die Tropfen in variablen Größen von 1 bis 1,5 mm in hoher Frequenz auf das Bauteil auf. Daraus resultiert eine sehr kurze Reaktionszeit von nur 1 ms. Bei dynamischen Robotergeschwindigkeiten von 50 bis 600 mm/s sind Richtungsänderungen nun kein Problem mehr. Auch in diesen Grenzbereichen ist eine präzise Applikation mit randscharfen Konturen möglich. Während bei konventionellem Materialauftrag in Kurven oft zu wenig PVC an die Außenseite und zu viel an die Innenseite gelangt, wird das Material mit dem neuen Verfahren auch bei Richtungsänderungen gleichmäßig aufgetragen. Selbst komplexe Nahtgeometrien mit Einschnürungen, Lücken und Nahtüberlappungen werden qualitativ und optisch hochwertig ausgeführt. Vor allem bei komplexen Bauteilgeometrien spielt das neue Verfahren seine Vorteile aus. Der Abstand zwischen Applikator und Bauteil kann 5 bis 80 mm betragen, in Sonderfällen sogar mehr als 100 mm – und nicht nur 3 bis 5 mm, wie es bei konventionellem Dichtstoff-Auftrag der Fall ist. Der wesentlich größere - und vor allem variable - Abstand vereinfacht die Roboterprogrammierung und auch die Zugänglichkeit zum Bauteil. Dabei ist ferner hilfreich, dass die Düsen vergleichsweise schräg zur Applikationsfläche stehen können, um die Tropfen in verschiedenen Winkeln, ziehend oder stechend, aufzubringen.
Und IDDA.Seal bringt noch weitere Pluspunkte mit sich: Die randscharfe Applikation macht viele Schablonen überflüssig, der hochpräzise Auftrag mit kontrollierter Schichtdicke kann die manuelle Nacharbeit um bis zu 40% reduzieren. Und das eingesparte PVC senkt den Materialverbrauch um bis zu 50%, wodurch auch das Fahrzeug leichter wird. Atlas Copco hat das neue Verfahren zum Patent angemeldet. Seit kurzem läuft die intelligente, dynamische Tropfenapplikation für das automatisierte Abdichten in der Audi-Serienfertigung in der Lackiererei am Standort Győr in Ungarn. Das Verfahren soll zukünftig an weiteren Audi-Standorten und neben der Feinnahtabdichtung kosmetischer Nähte auch für Grobnahtabdichtungen eingesetzt werden.