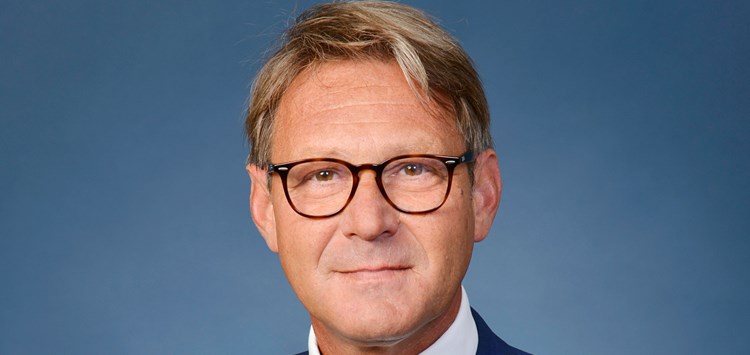
Geschäftsführer ab 1. Dezember 2021 – Dr. Victor Roman (Bild: privat)
09.11.2021 Arburg stärkt die additive Fertigung
Mit der neuen Tochtergesellschaft Arburg Additive GmbH + Co KG mit Sitz in Loßburg bündelt die Arburg GmbH + Co KG alle Aktivitäten der additiven Fertigung.
Mit der Gründung der neuen Gesellschaft unterstreicht Arburg die Bedeutung und das zukünftige Potenzial, die das Unternehmen in der additiven Fertigung als wichtiges und ergänzendes Fertigungsverfahren in der Kunststoffverarbeitung sieht. Nach der Entwicklung und Markteinführung des Freeformers und dem Kauf von innovatiQ war nun die Bündelung aller Aktivitäten unter einem Dach der nächste konsequente Schritt, um dieses Geschäftsfeld zu stärken. Mit Dr. Victor Roman übernimmt ein Branchen-Experte die Geschäftsführung der Tochtergesellschaft. Der 52-Jährige hat Maschinenbau und Physik studiert und war danach mehr als zwei Jahrzehnte in einer internationalen Technologie-Unternehmensgruppe tätig. Dadurch verfügt er über umfangreiche Erfahrungen in den Bereichen Entwicklung, Vertrieb und additive Fertigung.
Im Laufe des Jahres 2022 wird der komplette Bereich Arburg Kunststoff-Freiformen in die neue Gesellschaft wechseln. Dieser umfasst mittlerweile rd. 40 Mitarbeitende aus Vertrieb, Entwicklung, Anwendungstechnik und Montage. Die innovatiQ GmbH + Co KG, die derzeit rd. 25 Mitarbeitende beschäftigt, bleibt ein selbstständiges Unternehmen mit Sitz in Feldkirchen bei München, wird jedoch an die Arburg Additive GmbH + Co KG angegliedert. innovatiQ Geschäftsführer Florian Bautz wird künftig an Dr. Victor Roman berichten.
Zum Produktportfolio der neuen Gesellschaft gehören der Freeformer und die 3D-Systeme von innovatiQ. Das Arburg Kunststoff-Freiformen (AKF) mit dem Freeformer ist als offenes System konzipiert. Demzufolge lässt sich der Herstellprozess der Bauteile individuell einstellen, verarbeitet werden qualifizierte Standardgranulate, wie sie beim Spritzgießen eingesetzt werden. Die 3D-Drucksysteme innovatiQ arbeiten von auf Basis der FFF-Technologie (Fused Filament Fabrication). Hinzu kommt das LiQ 320-Drucksystem, das Flüssigsilikon (LSR) im besonderen LAM-Verfahren (Liquid Additive Manufacturing) verarbeitet. Die unterschiedlichen Maschinen ergänzen sich und decken so ein sehr breites Spektrum an additiven Anwendungen ab.