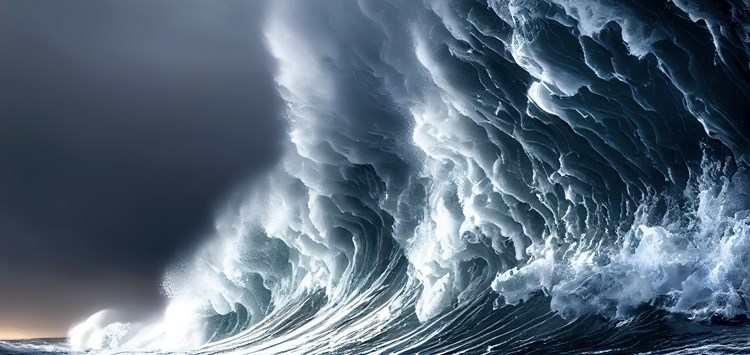
(Bild: AdobeStock_Viks_jin)
17.06.2025 Prozesstechnik: Frühwarnsystem gegen „regulatorische Tsunamis“
Mit einem flexiblen Monitoring die „Regulierungswut“ beherrschen
Regulierungen sind eines unserer zentralen Themen und betreffen zahlreiche Industrie- und Lebensbereiche. Was sicher in vielen Fällen einen sinnvollen Hintergrund hat, verkehrt sich durch regulatorische Herangehensweisen und Marktdynamiken oft ins Gegenteil. Für Julia Kletschke, Manager Kompetenz & Strategie der meweo GmbH, ist damit eines klar: Nur ein effektives Regulierungsmonitoring hilft der Prozessindustrie, knappe Ressourcen effektiv einzusetzen und – z.B. rund um die PFAS-Thematik – die richtigen Entscheidungen für die Zukunft zu treffen.
Neue Gesetze und Regularien führen aktuell zu hohen Unsicherheiten bei Dichtungsauswahl und -einsatz in der Prozessindustrie. Was ist der Hintergrund?
Kletschke: Die Dichtungsbranche und besonders der Markt der Prozesstechnik sind die letzten Jahre massiv von der „Regulierungswut“ aus Brüssel und Berlin betroffen. Hintergrund ist die Umsetzung des Europäischen Green Deal, der förmlich zu einem „regulatorischen Tsunami“ führte. Ein Beispiel ist das Gesetzesvorhaben, das ein allgemeines PFAS-Verbot zum Ziel hat. Danach sollen alle PFAS, welche unter aktueller Definition Fluorpolymere beinhalten, aus industriellen Anlagen verbannt werden. Die Analyse der Auswirkungen, die Su- Prozesstechnik: Frühwarnsystem gegen „regulatorische Tsunamis“ Mit einem flexiblen Monitoring die „Regulierungswut“ beherrschen che nach Alternativen und die damit verbundenen Kosten sind demnach enorm. Darüber hinaus führen regulatorische Änderungen bei der Überarbeitung der REACH- und der Lebensmittel- Verordnung zu einem neuen gesetzlichen Rahmen und damit zu Veränderungsdruck für die Prozesstechnik.
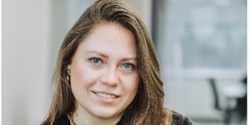
"Unsere Dienstleistung meweKomp liefert KMU – neben Informationen über gesetzliche Neuerungen – das Know-how, wie der regulatorische Prozess funktioniert, wer die besten Ansprechpartner im Politikapparat sind oder an welcher Stelle im Prozess man am besten eingreift, um sich Gehör zu verschaffen.“ Julia Kletschke, Manager Kompetenz & Strategie der meweo GmbH