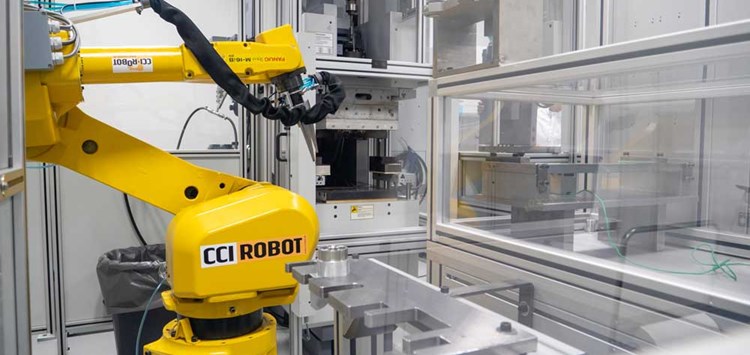
Bild 1: Die Entwicklung von PFAS-freien Dichtungswerkstoffen erfordert viel Know-how in Forschung und Entwicklung sowie die vertrauensvolle Zusammenarbeit mit Anwendenden (Bild: AVK GUMMI)
11.03.2025 Den Übergang zu einer PFAS-freien Zukunft gemeinsam gestalten
Neue Wege in der Polymertechnologie
Die durch PFAS (Perflouralkylsubstanzen) entstandenen Herausforderungen verlangen der Polymertechnologie viel ab. Dabei können neue Lösungen den Weg zu einer umweltfreundlicheren Zukunft ebnen. Der Weg wird idealerweise gemeinsam beschritten.
Seitdem die Europäische Chemikalienagentur (ECHA) im Februar 2023 den Vorschlag zur Beschränkung von PFAS veröffentlicht hat, gibt es eine lebhafte Debatte über die PFAS-Substanzen und wie die Emissionen von diesen persistenten Substanzen (auch „Ewigkeitschemikalien“ genannt) effektiv vermieden werden können. Die unumkehrbare Anreicherung der Umwelt mit PFAS und die damit verbundenen Gesundheitsrisiken machen die Notwendigkeit eines umfassenden Chemikalienverbots deutlich. Diese Erkenntnis steckt hinter dem Vorschlag der fünf EU-Mitgliedstaaten (Dänemark, Deutschland, die Niederlande, Norwegen und Schweden). Die Tragweite der Problematik und die Folgen für die Industrie abzuschätzen, ist aufgrund der vielen Einsatzbereiche solcher Stoffe und der Komplexität des Themas äußerst schwierig. Ebenso herausfordernd ist die Einschätzung aktueller und zukünftiger Gesetzesvorschriften und Ausnahmeregelungen. Die EU-Gesetzgebung wird mehrere Stufen der PFAS-Emissionen umfassen, u.a. den Produktions- und Herstellungsprozess sowie die Nutzung und Entsorgung.