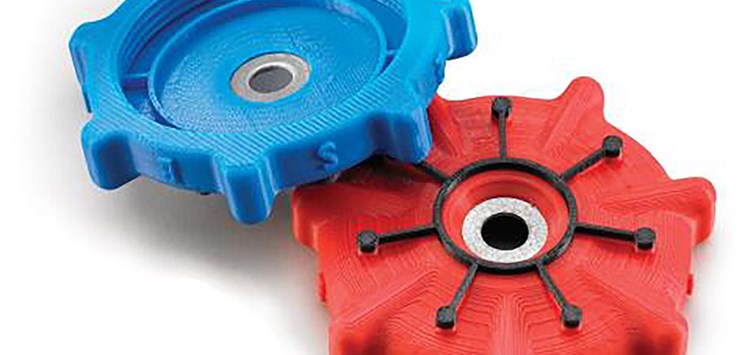
Per 3D-Druck hergestellte Teile (Bild: Karl Späh GmbH & Co. KG)
03.06.2019 Zerspanende Nacharbeit macht den 3D-Druck rund
Variables Fertigungskonzept für Hochleistungsbauteile
Die (additive) Fertigung per 3D-Druck ist seit Jahren zu Recht in aller Munde. Nicht nur, weil es immer mehr druckbare Materialien und Druckverfahren gibt, sondern weil sich die Qualität der so gefertigten Teile und die Maßhaltigkeit laufend verbessern. Das Vorurteil, dass Bauteile lediglich als Vorserienprodukte mit schlechten Eigenschaften zu hohen Kosten gedruckt werden können, ist falsch. Bei fertigungsorientierter Konstruktion und mit den richtigen Materialien und Druckverfahren lassen sich oft günstigere Teile mit deutlich verbesserten Eigenschaften produzieren.
Um die Vorteile dieser Technologie optimal zu nutzen, sollte schon bei der Konstruktion der zu fertigenden Bauteile das Fertigungsverfahren beachtet werden. Oft macht es Sinn, dass die Produktion von Artikeln, die bisher zerspanend hergestellt wurden, auf 3D-Druck umgestellt wird. Dabei lohnt es sich in jedem Fall, die Konstruktion dem Fertigungsverfahren anzupassen. Schon zu diesem Zeitpunkt sind „Sparringspartner“ mitdem entsprechenden Know-how sinnvoll, die Anwender über die unterschiedlichen Möglichkeiten und Chancen im 3D-Druck informieren, um dann gemeinsam die richtige Entscheidung zu erarbeiten (Bild 1). Oftmals ist es auch ein Zusammenspiel von zwei Fertigungsmöglichkeiten, das zum optimalen Ergebnis für den Kunden führt.
Beratungs-Kompetenz über viele Fertigungsverfahren hinweg ist dabei ein wichtiges Kriterium und macht einen Unterschied zu Lösungsanbietern, die sich ausschließlich mit einem Verfahren wie 3D-Druck beschäftigen. Die Firma Späh besitzt einen umfassenden Maschinenpark zur Gummi- und Kunststoffbearbeitung direkt im Haus und verfügt über das entsprechende Know-how nicht nur im Stanzbereich, sondern auch in der zerspanenden Fertigung.
Das zum Einsatz kommende Fertigungsverfahren wird dabei immer anhand der entsprechenden Kundenanforderungen im Hinblick auf gewünschtes Material, Geometrie, Stückzahl und Toleranzen ausgewählt. Kann das Produkt anhand der gewünschten Geometrie und Oberflächenbeschaffenheit im 3D-Druck hergestellt und können die geforderten Toleranzen mit der additiven Fertigung eingehalten werden, kommen die fertigen Produkte direkt aus dem Drucker.
Sind bei dem Kundenprodukt aber sehr enge Toleranzen gewünscht, werden die Teile nach dem Druckprozess zerspanend nachbearbeitet. Dabei können Fertigungsverfahren wie Fräsen, Drehen, Bohren, Reiben, Senken oder Gleitschleifen zum Einsatz kommen.
Ist der 3D-Druck für die Herstellung des Produktes für den Kunden unwirtschaftlich, wird ein geeigneteres Fertigungsverfahren gewählt. Vorteilhaft ist dabei, dass alle möglichen Fertigungsprozesse direkt im Hause zur Verfügung stehen und der Anwender dadurch nur einen einzigen Ansprechpartner hat – egal wie die Bauteile, Dichtungen und/oder Formteile nachher gefertigt werden.
Das Konzept in der Praxis
Die Vorteile dieser Vorgehensweise zeigen Projekte in Zusammenarbeit mit der Wörner Automatisierungstechnik GmbH. Dieser, einer der international führenden Anbieter von Anhalte- und Positioniermodulen in der Automatisierungstechnik, ist mit Produkten „Made in Germany“ rund um den Globus vertreten und legt großen Wert auf die Qualität der Zulieferer. Angefragt wurde zunächst eine Werkzeugträgerplatte für eine Graviermaschine aus dem Werkstoff ABS (Bild 2). Anhand des 3D-Modells des gewünschten Produkts und in ständigem Austausch wurde ein enormes Optimierungs- und Einsparpotenzial erarbeitet. Dabei konnten sowohl der Materialeinsatz als auch die Bearbeitungszeit verringert werden.
Alternativ hierzu wurde aufgrund der besseren Verarbeitbarkeit das alternative Material PLA angeboten. Da bei der Werkzeugträgerplatte die Toleranz von DIN ISO 2768-M vorlag, musste keine zusätzliche zerspanende Nacharbeit angewendet werden. In Zusammenarbeit mit dem Kunden wurden die Teile dann nach weiteren Konstruktionsanpassungen im FDM-Verfahren gedruckt.
Nach diesem erfolgreichen Projekt wurde ein weiteres angefragt – eine Schiebeführung für die Montagehilfe, bei deren Innendurchmesser eine Toleranz von + 0,05/+ 0,1 mm gefordert wurde. Zusätzlich dazu sollte der Werkstoff verschleißfest und die Oberfläche des Innendurchmessers möglichst fein sein. Wegen der benötigten Verschleißfestigkeit wurde dann das SLS-Verfahren mit dem Werkstoff PA12 mit einem 30 %igen Glasfaseranteil als Produktionsverfahren ausgewählt. Durch Konstruktionsanpassungen entstanden dann in der weiteren Zusammenarbeit z.B. Aussparungen am Außendurchmesser, um nicht verschmolzene Materialreste einfacher entfernen zu können. Dies brachte eine deutliche Prozessverbesserung. Nachträglich wurde an der Schiebeführung eine zerspanende Nacharbeit durchgeführt, wodurch die angeforderten engen Toleranzen des Durchmessers eingehalten werden konnten (Bild 3).
Fazit
Diese Beispiele zeigen, wie sich der 3D-Druck heute sinnvoll mit anderen Fertigungsverfahren kombinieren lässt, wenn diese Technik allein an ihre Grenzen stößt. Vorgehensweise und Know-how lassen sich dabei problemlos auf viele Bauteile, wie z.B. Dichtungen und Formteile, übertragen.
Fakten für Konstrukteure
• Das spätere Fertigungsverfahren hat Einfluss auf die Konstruktion, weshalb eine frühe Abstimmung sinnvoll ist
• Bei Partnern mit breitem Fertigungs-Know-how steht die Lösung und nicht das Fertigungsverfahren im Vordergrund
Fakten für Einkäufer
• 3D-Druck auf Vorserienprodukte zu reduzieren, ist nicht zeitgemäß – im 3D-Druck lassen sich heute, u.U. in Kombination mit anderen Fertigungsverfahren, wirtschaftliche Bauteile mit optimierten Eigenschaften fertigen
Fakten für Qualitätsmanager
• Qualitätsanforderungen, die mit dem 3D-Druck heute noch nicht erreicht werden, lassen sich durch die Kombination mit anderen Fertigungsverfahren erfüllen
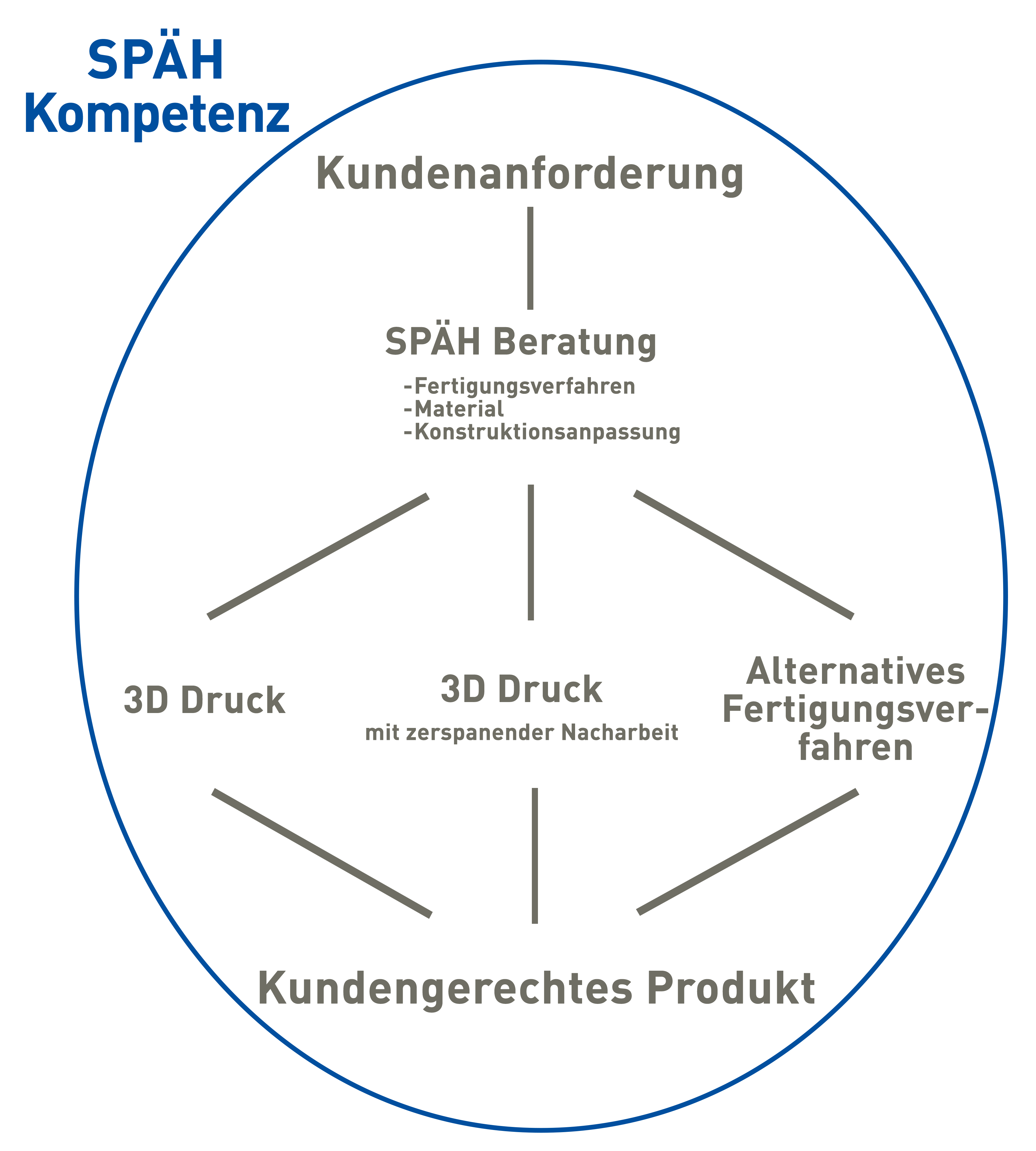
Bild 1: Beispiel einer Entscheidungsmatrix (Bild: Karl Späh GmbH & Co. KG)
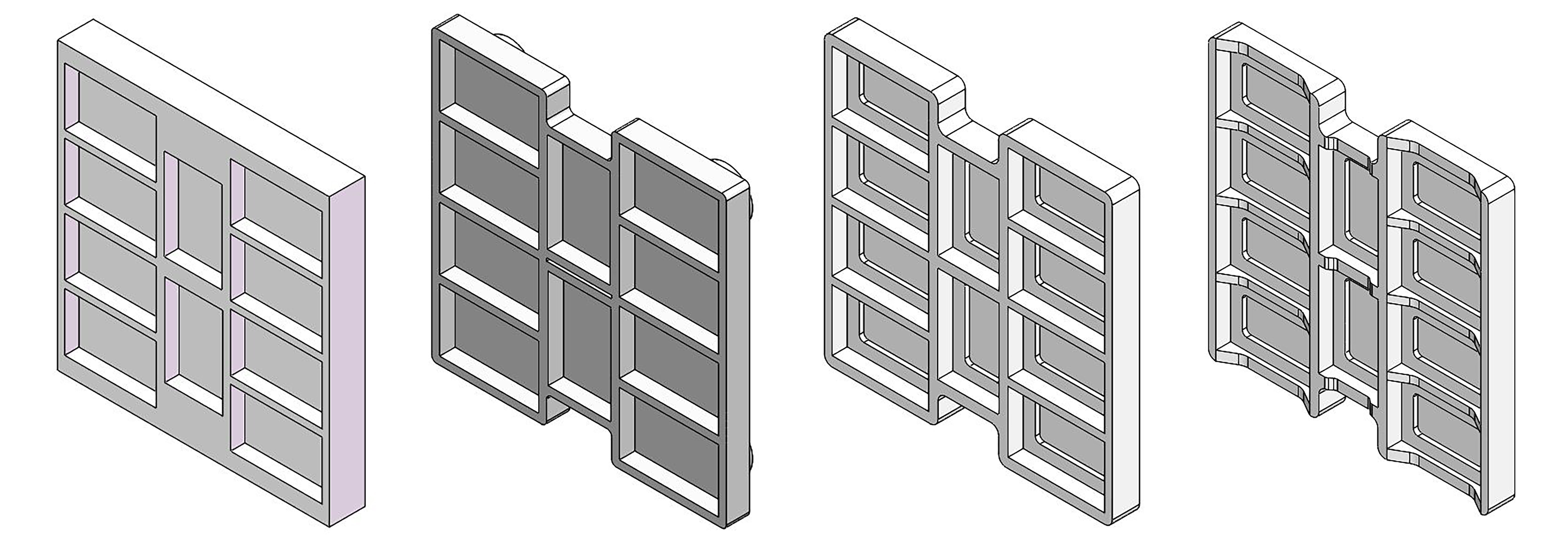
Bild 2: Werkzeugträgerplatte für den 3D-Druck optimiert
(Bild: Karl Späh GmbH & Co. KG)
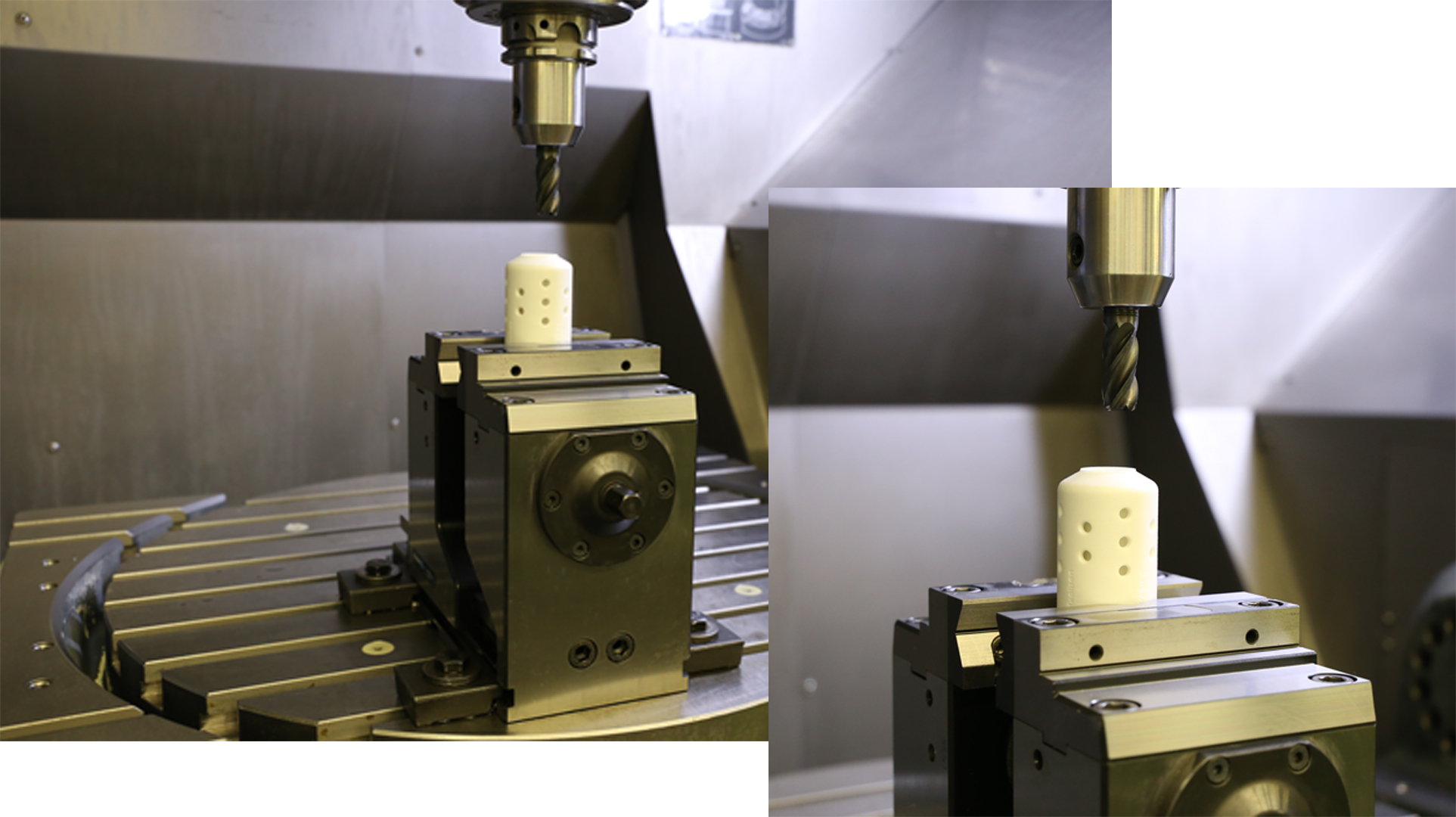
Bild 3: Zerspanende Nacharbeit – eine Option, um höhere Qualitätslevel oder engere Toleranzen zu erreichen (Bild: Karl Späh GmbH & Co. KG)