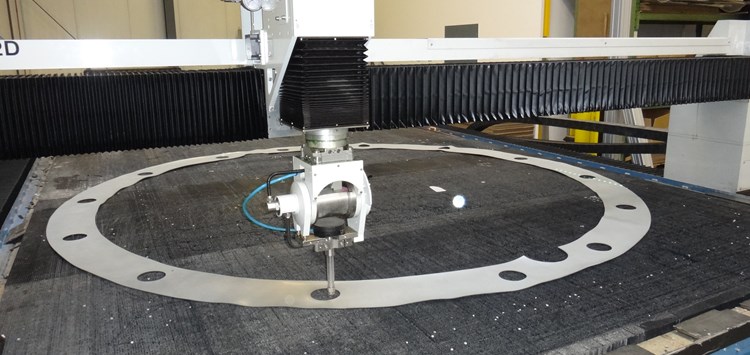
XXL-Dichtungen aus einem Stück bieten viele Vorteile (Bild: STEINBACH AG)
31.03.2018 XXL
Nahtlos Dichtungen und Membrane bis 3,2 m – Made in Germany
Trotz aller Miniaturisierungsbestrebungen in vielen Bereichen ist auch ein steigender Bedarf an Großdichtungen festzustellen. Dabei ist es von Vorteil, wenn solche Präzisionskomponenten nahtlos gefertigt werden können.
XXL-Dichtungen und Stanzteile (Bild 1) kommen in vielen Industriebereichen zum Einsatz – besonders im Maschinen- und Anlagenbau, aber auch im Schiffbau, in der Flugzeugindustrie sowie beim Rohrleitungs- und Pumpenbau werden sie – hergestellt aus verschiedensten Elastomeren – benötigt. Auch die Anwendungsmöglichkeiten für Membranen sind vielfältig. Sie eignen sich z.B. für den Einbau in der Offshore- und in der Raffineriebranche.
Nähte sind ein Problem
Dichtungen mit störenden Fügenähten haben verschiedene Nachteile: Das fängt bei der richtigen Wahl des Klebers für die Klebestelle an; Mindestmengen und Ablaufdaten erschweren teilweise Beschaffung und sichere Verarbeitung. Darüber hinaus ist die Beständigkeit des Klebers nicht immer vergleichbar mit der Beständigkeit des Dichtungsmaterials. Auch das unterschiedliche Dehnungsverhalten des Klebers im Vergleich zur Dichtungs-Rohplatte muss berücksichtigt werden. Dichtungen werden bei falscher Auswahl des Klebers anfälliger und büßen u.U. mit der Zeit ihre Druck- und Chemikalienbeständigkeit ein. Auch können Ausgasungen im Einsatzumfeld den Kleber angreifen und zur Zerstörung der Naht führen. Darüber hinaus sind teilweise Stufen- bzw. Stärkentoleranzen innerhalb der Platten/Dichtungen (je nach Stärke und Materialauswahl) vorhanden, die angeschliffen werden müssen. Der erforderliche Zeitaufwand bei der Nahtherstellung ist nicht zu unterschätzen. In Summe ist bei großformatigen Flachdichtungen also eine nahtlose Lösung vorteilhaft, da sie zudem i.d.R. leichter zu montieren und zu handeln ist.
Spezielle Maschinentechnik für XXL-Formate
Fertigungsanlagen für Großdichtungen, die den wachsenden Anforderungen an Dichtungen Rechnung tragen, gibt es nicht von der Stange. Die Steinbach AG hat deshalb eine Vulkanisieranlage entwickeln lassen, die nahtlose Elastomerplatten in Übergröße herstellt. Bisher wurden solche Anlagen für ähnliche Dichtungs- und Membrangrößen nur in China hergestellt. Nach zwei Jahren Entwicklungs- und Aufbauzeit ist die Anlage »2 seit letztem Jahr in Betrieb. Seitdem wurden zahlreiche Spezialprodukte mit eng gefassten Parametern vulkanisiert. Bisherige Vulkanisierungsanlagen produzierten Elastomerplatten bis zu einer Breite von 1,6 bis 1,8 m. Zwangsläufig mussten größere Dichtungen geklebt werden – und das mit den genannten Nachteilen. Mit der Rotocure D320 kann auf Nähte bei einer Membranbreite und Dichtungsdurchmessern von bis zu 3,2 m verzichtet werden. Ergänzend können auf eigenen 3D-Purwasserstrahlanlagen und Plottern großformatige Geometrien kundenspezifisch realisiert werden. Mit dieser Vulkanisierungsanlage lassen sich verschiedenste Elastomere bis zu einer Materialstärke von 0,5 bis 6 mm bearbeiten. Das Material-Portfolio umfasst Silikon, NR, EPDM, CR und NBR sowie FKM. Die eingesetzten Elastomere erfüllen höchste Qualitätsansprüche, z.B. die Siemens-Norm SN 53145-1. Darüber hinaus sind sie beständig gegen Trafoöl, Biogas und Biodiesel. Da für die Performance von Dichtungen und Membranen heute vielfach der eingesetzte Werkstoff entscheidend ist, wird derzeit an neuen Mischungen gearbeitet, um das Material-Portfolio mit Blick auf immer speziellere Kundenbedürfnisse zu erweitern.
Fakten für Konstrukteure/Instandhalter
• Geklebte Dichtungen können an der Nahtstelle unterschiedlichste Probleme verursachen
Fakten für Einkäufer
• „Made in Germany“ vereinfacht die Beschaffung erheblich
Fakten für Qualitätsmanager
• Die vorhandenen Elastomer-Werkstoffe und Mischungen erfüllen höchste Anforderungen und teilweise Unternehmensnormen
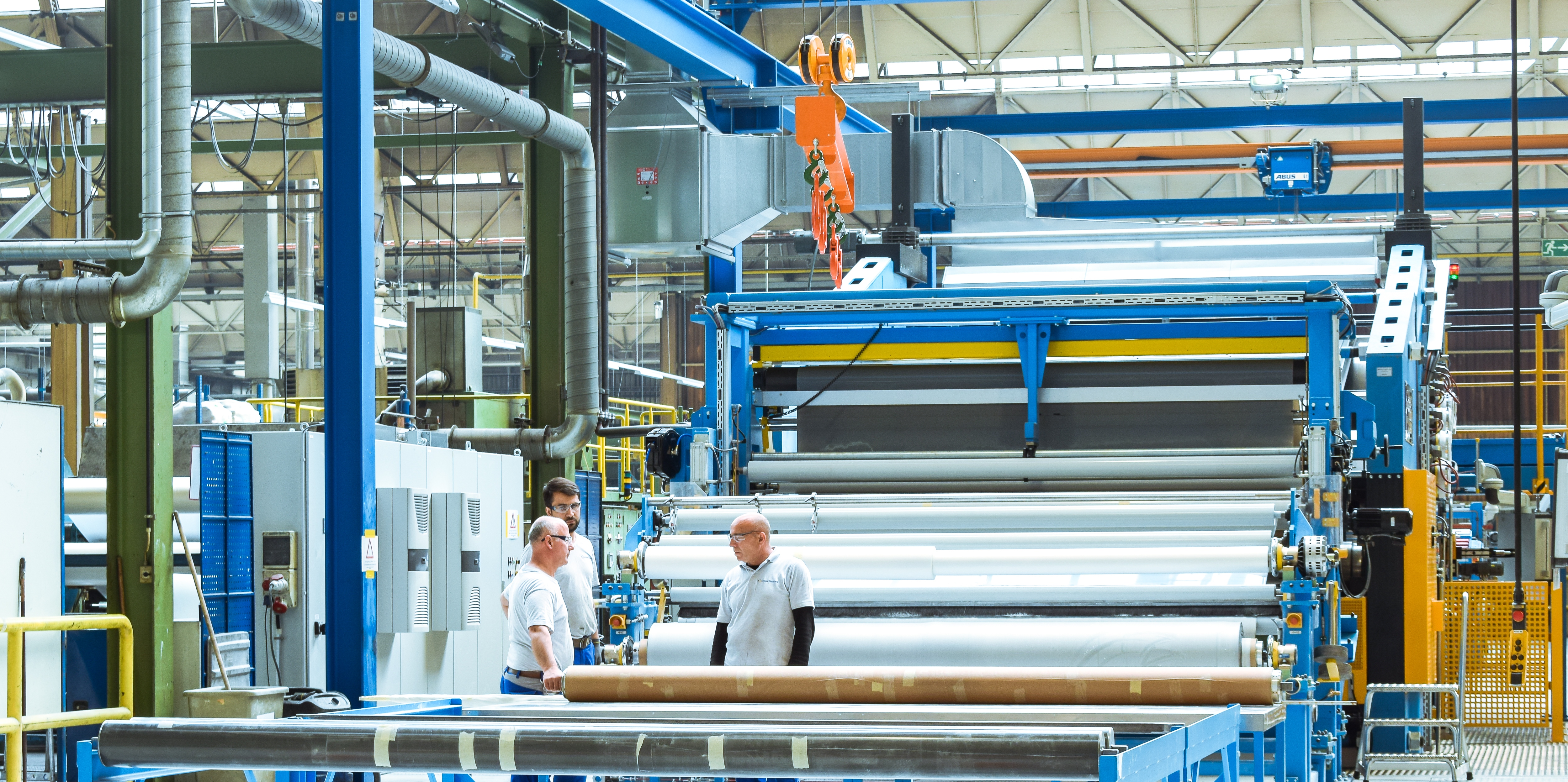
»2 Die Rotocure D320 fertigt nahtlose Dichtungen bis 3,2 m Durchmesser (Bild: Steinbach AG)
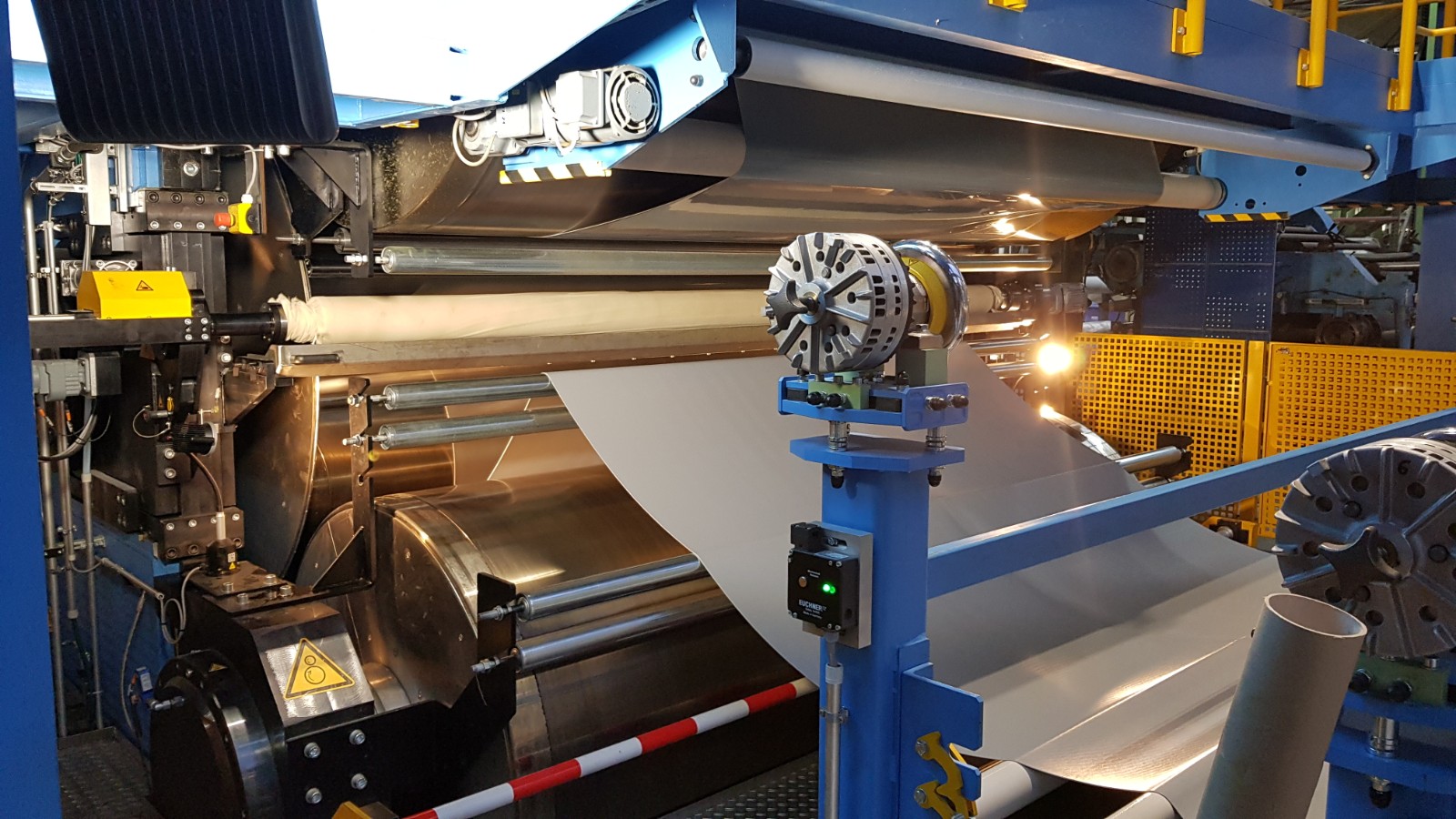
Dichtungsplatte aus Silikon vor der Vulkanisation (Bild: Steinbach AG)
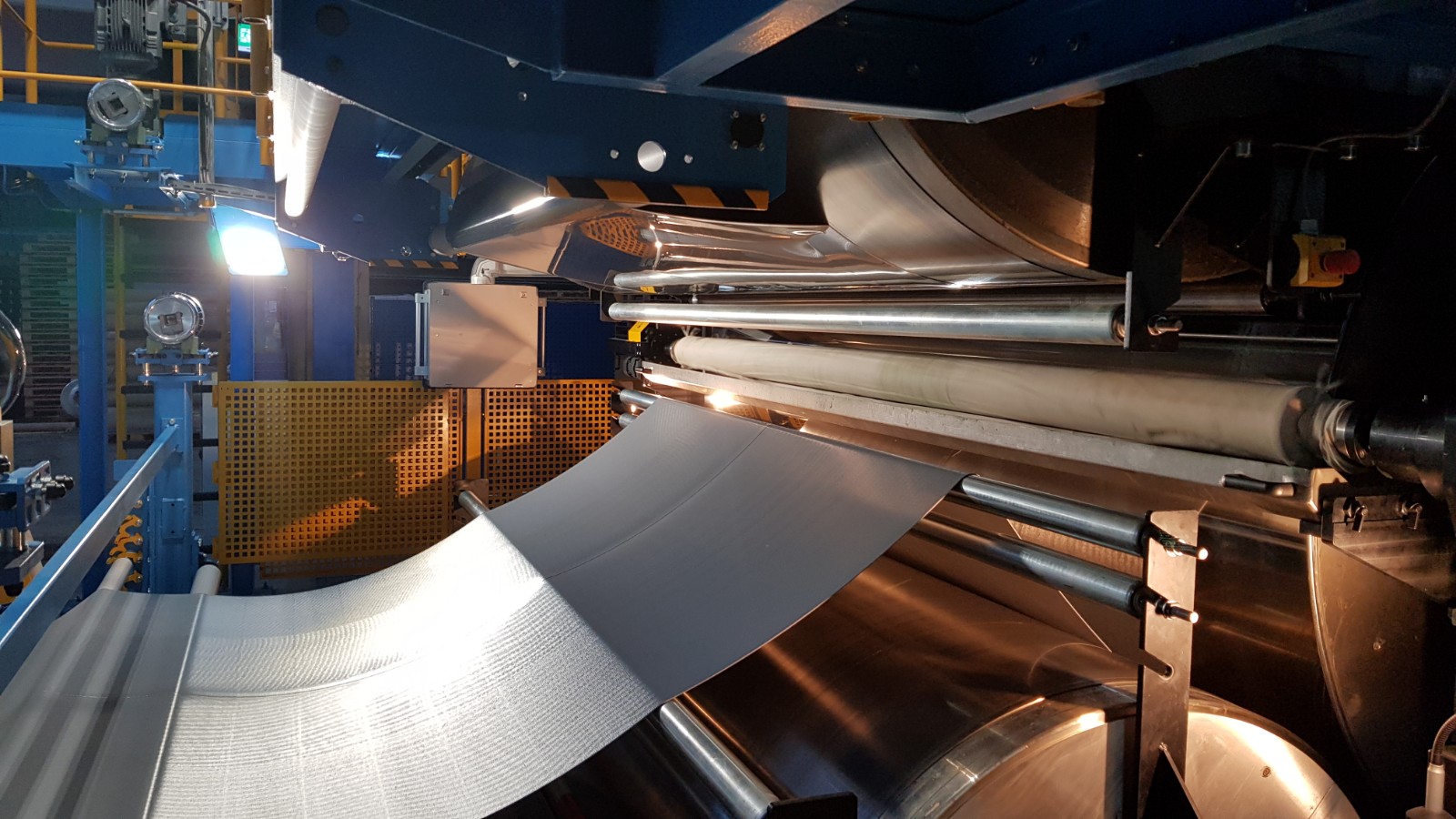
Unvulkanisierte Silikonplatte, die in die Maschine gegeben wird (Bild: Steinbach AG)
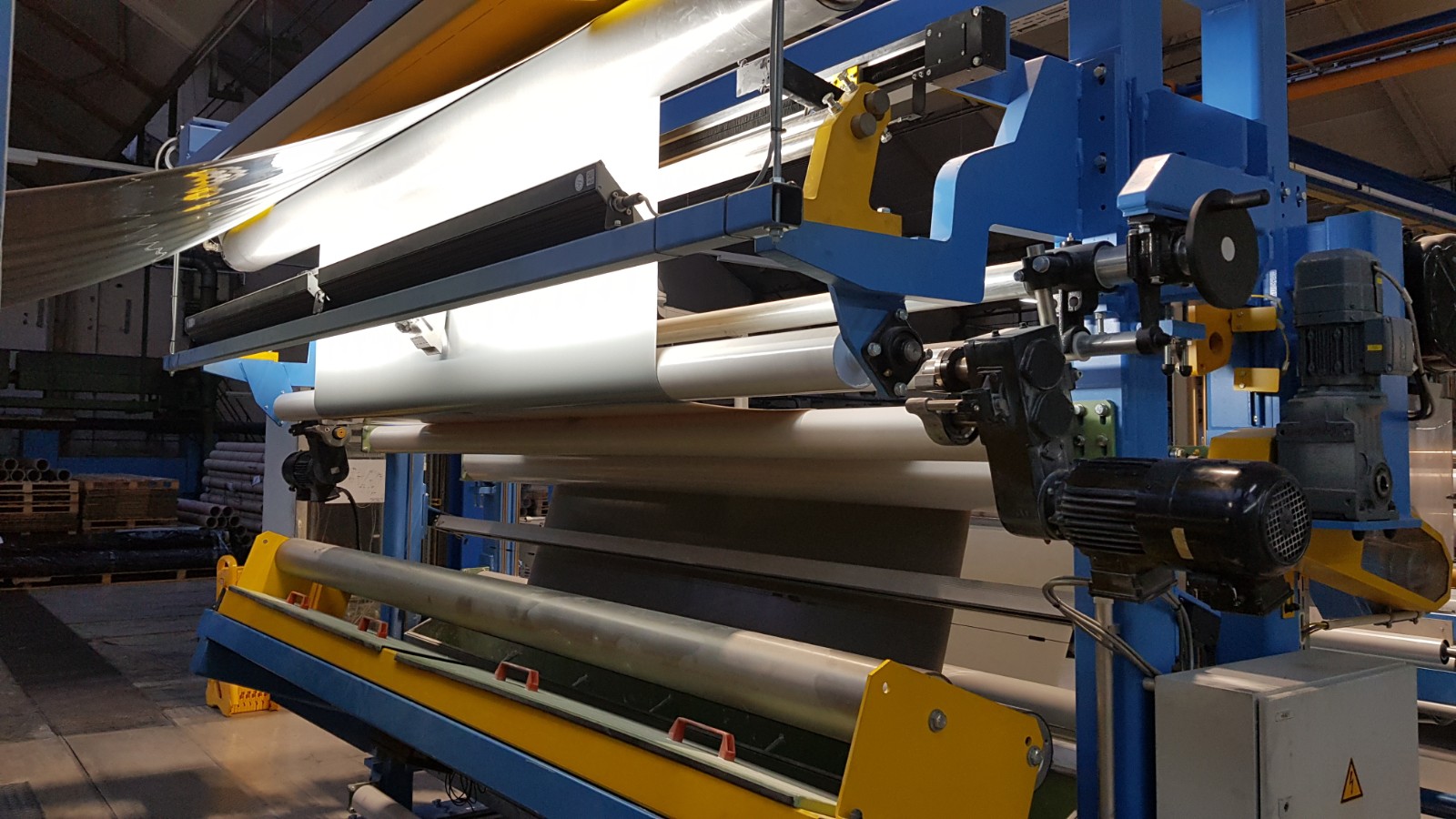
Dichtungsplatte aus Silikon nach der Vulkanisation (Bild: Steinbach AG)