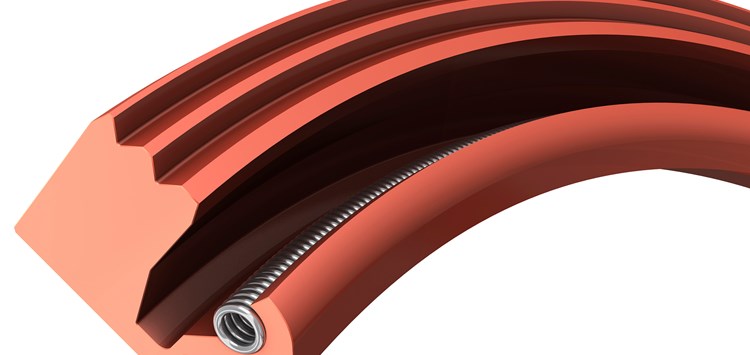
HRS1 - Basisausführung für Standardeinsatz (Bild: SKF Sealing Solutions Austria GmbH)
31.10.2016 Verbesserter Schutz von Windenergieanlagen
Neue Optionen durch leistungsstarke HRS-Dichtungen
Der Wind hat sich als Energiequelle inzwischen fest etabliert. Angesichts der weiter wachsenden Zahl von Windkraftanlagen werden deren Betrieb und Instandhaltung zu einem immer bedeutenderen Geschäftszweig. Dieses ressourcenschonende Business bringt allerdings auch viele Herausforderungen mit sich – erst recht, wenn die Windkraftanlagen in abgelegenen Gebieten wie z.B. im Gebirge oder auf See installiert werden. Dort kommt es umso mehr darauf an, dass die Anlagen ein Höchstmaß an Zuverlässigkeit und Verfügbarkeit aufweisen. Neue HRS-Wellendichtungen tragen zu einer höheren Turbinenzuverlässigkeit bei reduziertem Instandhaltungsaufwand bei. Zudem ist die neue Generation von Hochleistungs-Hauptwellendichtungen in jeder beliebigen Dichtungsgröße schnell verfügbar und erlaubt den vereinfachten Austausch direkt an der Turbine, sodass auch bestehende Anlagen mit HRS-Dichtungen bestückt werden können.
Dem Schutz moderner Windkraftanlagen dienen in erster Linie die Hauptwellendichtungen, die äußere Einflüsse vom Hauptlager und den Getriebekomponenten fernhalten. Außerdem verhindern sie das Austreten von Schmierstoffen. Eine neue Generation radialer Wellendichtringe aus G-ECOPUR® erfüllt das extreme Anforderungsprofil der Windenergiegewinnung (Bild 1).
Die Entwicklung
Die Weiterentwicklung und Optimierung von Windturbinen sowie der Trend zu größeren Anlagen mit höherer Energieausbeute führten zu deutlich gestiegenen Anforderungen an die Abdichtung. Während für kleine, zweifach gelagerte Hauptwellen handelsübliche Wellendichtringe oft noch ausreichen, treten bei modernen Anlagen mit hoher Leistung und teils einfach gelagertem Rotor deutlich höhere Lasten, Verformungen und Geschwindigkeiten auf, bei denen bisherige Standarddichtungen an ihre Grenzen stoßen.
Begleitend zu den steigenden Anforderungen wurde die Entwicklung einer speziell auf die Windindustrie zugeschnittenen Dichtungslösung gestartet, die für bestehende und neue Anlagen eingesetzt werden kann. Als erste größere Herausforderung erwies sich das Zusammenfassen der technischen Anforderungen, da es unzählige unterschiedliche Konzepte des Antriebsstranges gibt. Dichtungsdurchmesser von 350 bis 3.600 mm, stehende und rotierende Gehäuse, verschiedene Zugänglichkeiten der Dichtungsträger und diverse Schmierfette sowie mögliche Einsatzorte auf der ganzen Welt mit all ihren Umweltbedingungen waren zu berücksichtigen.