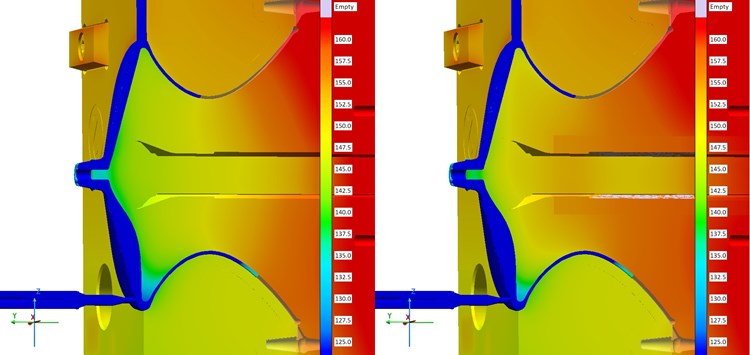
Optimierung der Temperaturverteilung durch den Einsatz eins CuBe-Kerns. Berechnung für das ursprüngliche Werkzeugdesign (links) und für das verbesserte Design (rechts) (Bild: SIGMA Engineering)
26.06.2024 Simulieren oder nicht simulieren?
Die zehn wichtigsten Gründe für die Verwendung von modernen Simulationssystemen
Simulation ist in der Kunststoff- und Elastomerverarbeitung weiter auf dem Vormarsch. Moderne Systeme liefern beeindruckende Übereinstimmungen zwischen Vorhersage und Realität für die vielfältigsten Aspekte in Prozess- und Anwendungstechnik. Das typische Einsatzgebiet gibt es allerdings genauso wenig wie typische Anwendungsbereiche – vom Entwicklungsbüro über mittelständische Unternehmen bis hin zu multinationalen Konzernen. Genutzt werden die Systeme von Materiallieferanten, Verarbeitung, Dienstleistung und Universitäten, Formenbau und auch Endkunden/OEMs. Natürlich muss die Investition in ein kostspieliges System mit Hardware, Software und Arbeitsplatz gut begründet sein und sich schnell amortisieren. Die Einsparungen durch den Einsatz moderner Systeme sind vielfältig und bei jedem erfolgreichen Anwendenden etwas anders verteilt.
1. Zeiteinsparung
Die Aussage: „Ohne Simulation geht es schneller, aber es dauert länger“, fasst zahlreich gemachte Erfahrungen gut zusammen. Zwei Wochen vor dem Termin fertig zu sein, weil der Prozess von Anfang an rund läuft, lässt sich schwer in Mannstunden und Maschinenzeit quantifizieren (Bild 1). Das Gleiche gilt für den Wert des Vertrauens, welches der Lieferant gewinnt, wenn Termine und Kostenrahmen immer sicher eingehalten werden. Die Sicherheit wird höher, wenn alles im Vorfeld optimiert wurde, noch bevor die Form gebaut wird. Beim Einfahren einer neuen Form ist es hilfreich, wenn diese im Rechner schon für zahlreiche Zyklen „gelaufen“ ist. Damit sind Prozessparameter wie Einspritzgeschwindigkeit, Heiz- und Kühlzeiten und statische Betriebsbedingungen schon bekannt.