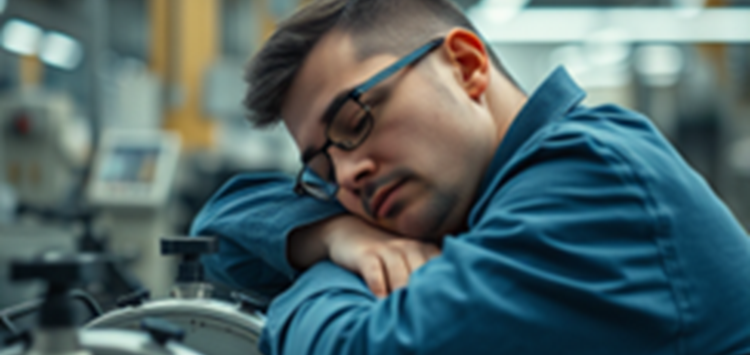
(Bild: KI generiert aus OpenAI.org)
11.03.2025 Simulieren lässt sich (fast) alles
Eine Simulation muss immer die Praxis abbilden! Diese Forderung ist absolut korrekt, wenn sie auf dem richtigen Verständnis basiert, was eine Simulation im Kern bedeutet.
Simuliert wird ein Prozess nämlich dann, wenn sich sein Ergebnis aufgrund der zahlreichen Einflussparameter und ihrer Zusammenhänge durch eine mathematische Formel nicht „einfach ausrechnen“ lässt.
Viele Produktionsprozesse können heute durch sehr gut zutreffende Rechenmodelle digital abgebildet werden. Die verwendete Rechnertechnik ist hoch leistungsfähig – lange Wartezeiten sind Vergangenheit. Prozessänderungen, Produkt- oder Werkstoffvarianten können einfach und schnell durchgespielt werden, ohne dass dafür Versuche auf einer teuren Produktionsmaschine nötig werden. Die durchgeführten Simulationen können unterschiedlich komplex sein. Je detaillierter ihre Aussagekraft sein soll, desto genauer müssen auch ihre Eingabewerte sein. Wer verlangt, dass eine Simulation alle relevanten Gegebenheiten in der eigenen Produktion auf das Bauteil vorhersagt, muss diese auch bei der Simulation berücksichtigen. Nehmen wir das Spritzgießen als Beispiel.
Bei einer Grobsimulation wird zunächst die Lage von Bindenähten aufgezeigt oder die grundsätzliche Position möglicher Anbindungspunkte variiert. Schon in einer solchen, ganz allgemeinen, Fließanalyse steckt eine Menge Erkenntnis: wie breitet sich die Schmelze aus, wo fließt sie langsamer oder eilt vor, wo treffen Fronten zusammen und wo enden sie? Das daraus entstehende Verständnis für den Prozess sollte nicht unterschätzt werden. Es prägt maßgeblich unser Bild vom Ablauf in der Maschine. Aus diesen ersten Erkenntnissen werden bei der fortschreitenden Entwicklung Änderungen und Anpassungen abgeleitet. Schritt für Schritt werden Konstruktion, Material und Prozess immer feiner aufeinander abgestimmt und detailliert.
Der nächste Entwicklungsschritt bedeutet ein ganz anderes, grundsätzliches Verständnis: Die Bauteileigenschaften sind nicht die Materialeigenschaften! Das gilt für Festigkeit ebenso wie für Farbe, Funktion und andere speziellen Eignungen. Alle uns zur Verfügung stehenden Materialien werden anhand standardisierter Methoden hergestellt und geprüft. Die Ergebnisse der Prüfungen werden im Datenblatt, im Zertifikat oder als
„digitaler Zwilling“ abgebildet. Doch zwischen der Performance des eigenen Bauteils und denen des Prüfkörpers stehen Verarbeitungsprozess, spezifische Geometrie sowie die auftretenden Lasten beim Betrieb. Die Verarbeitung bestimmt die späteren Bauteileigenschaften ganz wesentlich! Um diese frühzeitig abschätzen zu können, helfen Struktursimulationen („FEM“), bei denen die Prozessergebnisse als Rechenbasis dienen. Mechanisch hoch belastete Bereiche müssen durch den Verarbeitungsprozess auch das maximale Potenzial des Werkstoffs ausschöpfen. Passende Scherraten, gleichmäßige Fließfronten, gezieltes Erstarren oder die optimierte Faserlage bei verstärkten Materialien sind Ergebnisse der Optimierung, basierend auf der Simulation.
Sind die erfolgversprechendsten Varianten bestimmt, werden sie in der Feinsimulation durchgespielt. Alle Randbedingungen wie hochwertige Materialdaten, Werkzeugkonstruktion, Maschinendaten und andere, ergebnisbestimmende Einflüsse (Entlüftung, Leistung des Kühlsystems, Werkzeugstahl-Sorten, Einsätze etc.) werden berücksichtigt. Ein solches Vorgehen erlaubt in der Praxis, dass bereits Teile aus der ersten Abmusterung die Spezifikationen zum Verkauf erfüllen. Werkzeugänderungen sind nicht nötig.
Laufende Prozesse werden, wenn sie digital abgebildet sind, sehr effektiv durch Optimierungsschleifen mittels Simulation verbessert. Werden datenbankbasierte Plattformen mit solchen Ergebnissen gefüttert, können Ähnlichkeitsanalysen auch dem Vertrieb bei Neuanfragen wertvolle Hilfe leisten.
Angewiesen ist die Simulation immer auf das Feedback aus der Produktion. Die virtuelle Produktentwicklung muss wissen, welche Einflüsse das Produkt maßgeblich mitbestimmen. Was sich digital als Einfluss abbilden und berücksichtigen lässt, kann auch mit simuliert werden. Davon sind jedoch bestimmte Sonderfälle ausgenommen – siehe obiges Bild.
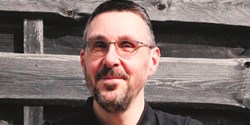
„Varianten, Optimierungen und Neuentwicklungen sind Resultate der Simulation.“ Dr.-Ing. Michael Bosse, Technical Sales Material- und Prozess-Experte, SimpaTec GmbH