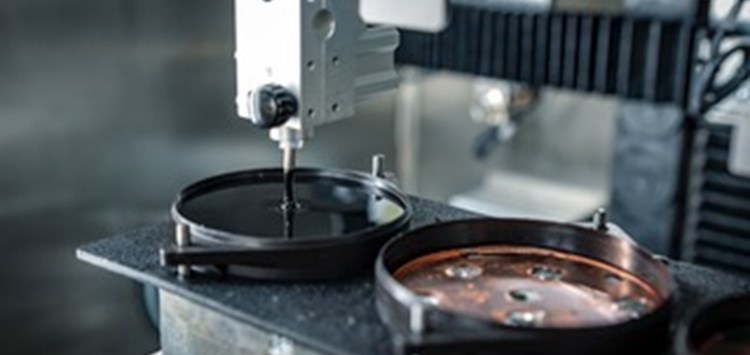
Vergusslösungen für eine effiziente Elektromobilität gibt es noch nicht von der Stange (Bild: Demak Group)
17.11.2020 Probieren geht über studieren
Flüssigdicht- und Vergusssysteme im Spagat zwischen bewährten Lösungen und Pionierarbeiten
Insbesondere der Markt für Elektromobilität fordert eine immer stärkere Miniaturisierung von Bauteilen bei gleichzeitig höherer Stromerzeugung.
Die Kombination aus weniger Platz und mehr Leistung erfordert daher unbedingt eine höhere Wärmeleitfähigkeit, was in diesem Fall die Vergusstechnologie stark miteinbezieht. Um die beste Wärmeableitung zu erreichen, und somit bis zu 80 % der im Betrieb erzeugten Wärme abzuleiten, muss eine gute Wärmeleitfähigkeit des beteiligten Harzsystems vorhanden sein, aber noch wichtiger ist eine perfekte Imprägnierung der Endkomponente. Die Hauptherausforderung der Vergusstechnologie besteht darin, die höchste Prozessqualität zu erreichen, also eine perfekte Kombination zwischen dem Harzsystem, das manchmal sehr viskos und abrasiv ist, und der eingesetzten Dosieranlage.
In der Praxis gibt es hier ein Hauptmissverständnis: Das ist die Annahme, dass eine sehr hohe Wärmeleitfähigkeit des Harzsystems ohne Berücksichtigung seiner Viskosität und Abrasivität eine drastisch höhere Wärmeableitungsrate und damit eine niedrigere Arbeitstemperatur des elektrischen Bauteils ergibt. Es ist absolut richtig, dass eine große Differenz in der Arbeitstemperatur entsteht, z.B. bei Verwendung von 1,4 W/m*K im Verhältnis zu 0,6 W/m*K. Gleichzeitig liefert ein sehr hoher Imprägnierungsgrad mit einem niedrigviskosen 1,2 bis 1,4 W/m*K-Harzsystem viel bessere Ergebnisse im Vergleich zu einer schlechten Imprägnierungsqualität unter Verwendung eines viskoseren Harzsystems mit höherem Wärmeleitfähigkeitswert, da seine sehr hohe Viskosität Hohlräume und damit mangelnde Wärmeableitung verursacht. Da der Imprägnierungsgrad der wichtigste Faktor ist, ist es immer das Ziel, das beste Gleichgewicht zwischen der Wärmeleitfähigkeit (je höher, desto besser) und der Viskosität des Materials zu erreichen, das natürlich aufgrund des höheren Gehalts an mineralischen Füllstoffen zunimmt.
Als Hersteller von Harzsystemen und Dosiermaschinen sind wir bestrebt, die beste Lösung zu finden, wobei stets die perfekte Kombination aus chemischen und mechanischen Aspekten im Auge zu behalten ist, um dann den bestmöglichen Vergussprozess für Batterien, E-Motoren, Kondensatoren und vieles andere zu erzielen.
Nicht nur hier spielen dann Technologiezentren, Forschungs- und Entwicklungslabors sowie Kundenschulungen eine entscheidende Rolle, um ein zufriedenstellendes Gesamtergebnis des Projekts zu erzielen. Diese Einrichtungen werden zudem benötigt, um die Parameter eines Vergussprozesses festzulegen und Machbarkeitsaspekte zu bewerten. Aus diesem Grund konzentrieren wir uns auf die Einrichtung von Technologiezentren sowie Forschungs- und Entwicklungsabteilungen auf der ganzen Welt, insbesondere des in diesem Jahr gegründeten Demak Germany-Centers, welches in Zusammenarbeit mit der LED Protect GmbH entstanden ist. Vor Ort kümmert sich ein Expertenteam insbesondere um LED-Verkapselungstechnologien sowie den Verguss aller möglichen elektrischen Komponenten. An unserem Hauptsitz in Italien verfügen wir ebenfalls über ein umfangreiches Vergusslabor, in dem Prozessingenieure Vergussprüfungen an Kundenbauteilen mit festgelegten Prozessparametern durchführen. Von dort erhält das technische Büro die Daten, um dann die entsprechenden Dosiermaschinen herzustellen. Zusätzlich zu den Vergusslabors haben wir zwei chemische Labors in der Harzherstellungsanlage in Turin eingerichtet, in denen Forschungs- und Entwicklungs- sowie Analysetests stattfinden. Diese Ressourcen sind wichtig, um eine entsprechende Beratung des Kunden bei seinen Projekten sicherzustellen. Hier ist derzeit mehr Flexibilität und Agilität als sonst gefragt, da einige Produktionstechnologien für die Elektromobilität erst im Entstehen sind. Es hat sich hier bewährt, dass ein Team aus Kundenspezialisten und unseren Technikern und Ingenieuren gemeinsam Lösungen erarbeitet und dabei immer auf unsere 40-jährige Erfahrung zurückgreifen kann. Dank unseres chemischen und mechanischen Wissens sind wir in der Lage, unseren Kunden mit einem 360°-Service im Vergussprozess zu unterstützen.
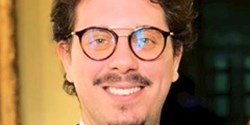
„Für ein effektives Wärmemanagement sind verschiedene Aspekte zu berücksichtigen. Hier wird oft zu kurz gedacht.“ Pietro Colombotto, Sales Manager, Demak Group