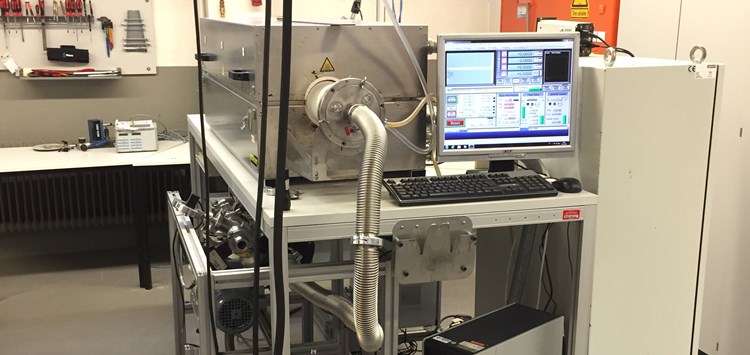
Simulationsanlage (Bild: Gemeinnützige KIMW Forschungs-GmbH)
11.10.2022 Neuer Verschleißschutz für Spritzguss-Werkzeuge
Hartstoffschichten aus MOCVD
Spritzgießwerkzeuge werden durch ständig wachsende Anforderungen immer komplexer. Diese sind abrasiven Materialien und Umgebungen ausgesetzt, was den Werkzeugen zusetzt. In der Folge kommt es zu Ausfällen sensibler Bauteile, ungewollten Stillstandszeiten bis hin zu kompletten Produktionsausfällen. Zu den lebensverlängernden und kostensenkenden Maßnahmen gehören Beschichtungen. Dehalb hat man sich mit dem Projekt AbraCoat der Entwicklung von Hartstoffschichten mittels MOCVD für abrasive Anwendungen auf komplexen Geometrien gewidmet.
Beschichtungen von Werkzeugen sorgen für eine höhere Verfügbarkeit in einem Spritzgießprozess. Die meisten heute im Markt eingesetzten Beschichtungen für einen Verschleißschutz in Spritzgießwerkzeugen werden in der Physikalischen Gasphase (PVD) appliziert. Erreicht werden gute Schichteigenschaften, charakterisiert durch die Schichthärte, die Haftung und die Verschleißfestigkeit. Da es sich bei der PVD (Physical Vapour Deposition) um ein gerichtetes Verfahren handelt, können Bereiche, die bauartbedingt verdeckt sind, kaum oder gar nicht beschichtet werden.
Alternativ bietet die Chemische Gasphasenabscheidung (Chemical Vapour Deposition, kurz CVD) (Bild 1) den signifikanten Vorteil einer 3D-Fähigkeit, durch die auch die Beschichtung hinterschnittiger Konturen möglich ist. Mithilfe eines Heißwandreaktors wird das gesamte Reaktorvolumen durch eine externe Heizquelle auf die benötigte Prozesstemperatur erhitzt. Für metallorganische Hartstoffschichten, wie z.B. Wolframcarbid, werden nur geringe Temperaturen von etwa 350 °C benötigt. In einem Verdampfer werden die Precursoren bzw. die Vorläuferverbindungen in die Gasphase überführt. Im Reaktorinneren reagieren sie dann ab und zersetzen sich dabei.