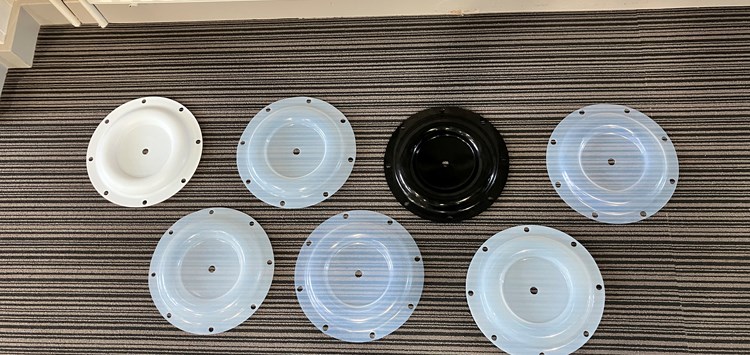
Pumpenmembranen aus PTFE, auch in antistatischer Ausführung, eignen sich für das Upcycling-Verfahren. Sie sind uneingeschränkt SIP- und CIP-fähig. Dank innovativem Fertigungsverfahren werden bisher übliche Laufzeiten um bis zu Faktor Fünf übertroffen – ein Garant für sicheren Betrieb und hohe Anlagenverfügbarkeit zwischen den Wartungsintervallen (Bild: FPS GmbH)
10.09.2024 Nachhaltige Werkstoff- und Dichtungslösungen – wir sind dabei
Ein Überblick über aktuelle Ansätze
Obwohl bei Dichtungslösungen als Voraussetzung für eine sichere Funktion das Eigenschaftsprofil der Dichtungen im Vordergrund steht, wird immer öfter die Frage nach der Nachhaltigkeit der Dichtungslösung gestellt.
Insbesondere im Bereich des Anlagenbaus der chemischen und pharmazeutischen, der ölfördernden und verarbeitenden Industrie, der Halbleiterindustrie oder in Anwendungen mit wiederholtem Kontakt mit Lebensmitteln werden in regelmäßigen Abständen, z.B. alle zwei Jahre, Wartungsarbeiten an der Komplettanlage durchgeführt. Dabei werden üblicherweise die gebrauchten Dichtungen durch neue ersetzt, um dadurch die Verfügbarkeit der Anlage bis zur nächsten Wartung sicherzustellen.
Doch wohin mit den gebrauchten Dichtungen? Bei PTFE-Dichtungen haben neueste Entwicklungen die Überführung der bisherigen „linearen Wirtschaft“ in eine Kreislaufwirtschaft ermöglicht. Dank des von 3M/Dyneon, gefördert durch die DBU (Deutsche Bundesstiftung Umwelt) und das Bundesministerium für Umwelt, Naturschutz und Reaktorsicherheit, entwickelten Upcycling-Verfahrens können nun gebrauchte Dichtungen auf Basis von PTFE in einem chemischen Recyclingverfahren in die Monomere zurückgespalten werden. Hierzu geeignet ist ein Pyrolyseverfahren, in dem bei Temperaturen oberhalb der „Ceiling-Temperatur“ – hier lassen sich Polymere wieder in die Monomere zerlegen – die eingesetzten Fluorpolymere in die Monomere, insbesondere Tetrafluorethylen (TFE) und Hexafluorpropylen (HFP), zurückgespalten werden. Aus diesen können dann, nach Durchlaufen eines Reinigungsprozesses, neue Fluorpolymere hergestellt werden. Dabei müssen keine Kompromisse hinsichtlich der Qualität eingegangen werden, wie das bei anderen Recyclingverfahren der Fall ist. In einem fünfjährigen Probebetrieb der Pilotanlage am Standort Gendorf, Oberbayern, wurde nachgewiesen, dass keine Qualitätsunterschiede der recycelten Neuprodukte im Vergleich zu den Ursprungspolymeren bestehen.
Im Vergleich zum bisher üblichen Verfahren für die Herstellung von Fluorpolymeren aus dem Mineral Kalziumfluorid, CaF2, werden dabei ca. 75% der sonst üblichen CO2-Emissionen eingespart, weil die Monomere nicht mehr in mehrstufiger, aufwändiger Synthese hergestellt werden müssen, sondern aus „fertigen Polymeren“ gewonnen werden. Eine signifikante Absenkung des Carbon Footprints ist die unmittelbare Folge, und die endliche Ressource CaF2 wird geschont.
Für das Verfahren geeignet sind Dichtungen und andere Bauteile aus den Werkstoffen PTFE, aus modifiziertem PTFE, PFA und FEP. Auch hinsichtlich der Füllstoffe ist das Verfahren tolerant, sofern diese aus Kohle oder Glas bestehen. Damit sind mindestens 75% der Compounds aus den genannten Werkstoffen für das Upcycling-Verfahren geeignet.
Wie kann man sich den neu geschaffenen Stoffkreislauf vorstellen, um sowohl Verarbeitungsabfälle als auch Dichtungen und andere Fluorpolymerbauteile nach dem Erreichen ihres „End-of-Life“ dem chemischen Recycling zuzuführen? Geplant ist der Aufbau eines Erfassungssystems von vollfluorierten Sekundärrohstoffen, im Rahmen dessen diese direkt am Entstehungsort, also durch die Verarbeitungsbetriebe für Fluorpolymere oder bei der Anlagenwartung bzw. deren Rückbau, erfasst werden. Nach Sortierung und ggf. Trennung von Metallkomponenten können diese direkt dem Upcycling-Verfahren zugeführt werden.
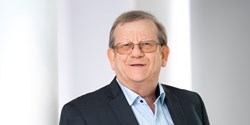
„Bei vollfluorierten Fluorpolymeren, auch mit den Füllstoffen Glas und Kohle, wird zukünftig eine Kreislaufwirtschaft möglich sein. Das Upcycling-Verfahren ist ökonomisch sinnvoll und ‚rechnet’ sich für alle Beteiligten.“ Dr. Michael Schlipf, Geschäftsführer, FPS GmbH