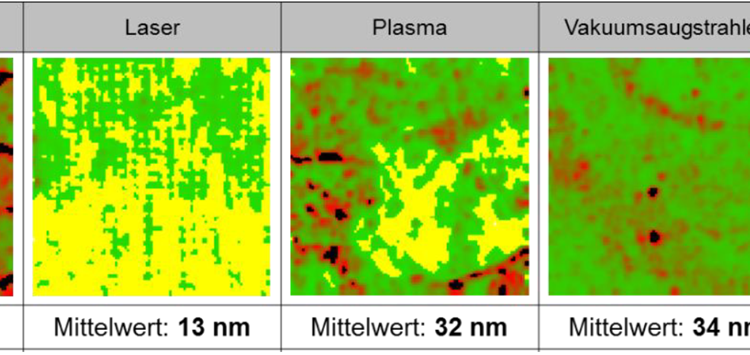
Kohlenstoffbelegung einer Aluminiumprobe – Vergleich von Ausgangszustand und verschiedenen Vorbehandlungen (Bild: [2])
29.10.2021 Metalle für das prozesssichere Abdichten und Dichtkleben vorbereiten
Entfernen von Verschmutzungen bei optimierter Korrosionsstabilisierung
Für eine qualitativ hochwertige Fügestelle ist die Reinigung und Vorbehandlung der Oberfläche eine wichtige Voraussetzung. Durch die Laservorbehandlung ist die metallische Oberfläche kontaminationsfrei und optimal für die Verbindung vorbereitet. In der Deckschicht aus Rückständen aus dem Herstellungsprozess, Verschmutzungen und Oxiden wird die Laserstrahlung einer Wellenlänge von ~ 1 μm absorbiert. Die darunterliegende metallische Oberfläche reflektiert einen großen Anteil der Strahlung und bleibt bei niedrigen Intensitäten unverändert.
Die Wirkweise der Lasertechnologie hängt von ihrer Einstellung ab. Wenn die Laserparameter entsprechend intensiver eingestellt werden, lassen sich metallische Materialien auch gezielt in der obersten Grenzschicht modifizieren. Durch die Applikation kurzer Pulse mit hoher Energiedichte können Kristallstruktur, Oberflächenchemie und Morphologie gezielt verändert werden. Dabei ist es z. B. möglich, die Substratoberfläche zu vergrößern bzw. sie den Verbindungsmechanismen anzupassen.
Die Wechselwirkung der Laserpulse im Nanosekundenbereich mit der metallischen Oberfläche erfolgt nach dem photothermischen Mechanismus, d.h. die absorbierte photonische Energie wird in Wärme umgewandelt. Durch die Absorption innerhalb eines sehr kleinen Volumens an der Oberfläche – typische optische Eindringtiefen bei Metallen liegen im Bereich weniger nm – steigt die Temperatur innerhalb kürzester Zeit stark an. Die oberflächennahe Zone wird im Bereich von typischerweise ~1 bis 3 μm in wenigen Nanosekunden umgeschmolzen und teilweise verdampft. Durch die schnelle Wärmeabfuhr über das Substratvolumen wird die Schmelze gleichzeitig schnell wieder abgekühlt. Diese Selbstabschreckung kann mit hohen Geschwindigkeiten von einigen m/s zur Erstarrung des Materials führen und „friert“ die Oberfläche in seinem momentanen Zustand ein, sodass sich eine veränderte Kristallstruktur mit neuen Korngrenzen bildet. Eine neue, mikrokristalline bzw. amorphe und zugleich raue Grenzschicht (Adaptionsschicht) entsteht, die eine deutlich geringere Elementkorrosion aufweist [2].
Der Modifikationsprozess läuft an der Luft ohne Schutzgasatmosphäre ab. Durch den hohen lokalen Energieeintrag des Lasers wird die Reaktion mit dem Sauerstoff aus der Atmosphäre beschleunigt und verstärkt, sodass eine durchgehende und beständige Oxidschicht aufgebaut wird. Die neue Passivierungsschicht auf der Schmelze bildet eine sehr stabile Brücke zum Kleb- oder Dichtstoff. In Kombination mit der Absenkung des elektrochemischen Potenzials bei gängigen Aluminium- und Magnesiumlegierungen resultiert daraus das langzeit- und alterungsbeständige Kleben.
Bei unbehandelten Oberflächen werden insbesondere Mikroseigerungen in einer dünnen Oberflächenschicht von Aluminiumlegierungen als Ursache für Lochfraß und als Ausgangspunkt für Korrosion festgestellt. Die verbesserte Korrosionsstabilität nach der Laservorbehandlung wird auf die Homogenisierung und Verfeinerung der Mikrostruktur zurückgeführt, die mit der Umschmelzung und Auflösung von Unregelmäßigkeiten und Einschlüssen zusammenwirkt. Die chemisch stabile Oxidschicht bildet dabei eine wirksame Barriere und schützt das Substrat vor korrosiven Einflüssen.
Durch das kurzzeitige Umschmelzen entstehen darüber hinaus „Mikrokrater“, die zu einer signifikanten Oberflächenvergrößerung in Verbindung mit einer besseren Benetzbarkeit und somit – insbesondere unter Scherbelastung – zu einer höheren Kräfteübertragung führen (Bild 1). Die Laserparameter wie Intensität, Pulsdauer und Scangeschwindigkeit beeinflussen direkt die neu entstehende Mikrostruktur und spielen für den Prozess eine entscheidende Rolle.
Analysiert man die gelaserte Oberfläche, z.B. mittels Rasterelektronenmikroskop (REM), wird eine deutlich angereicherte Oxidschicht im Vergleich zu einer Referenzoberfläche, die nur chemisch gereinigt wurde, erkennbar. REM-Aufnahmen einer Aluminiumprobe sind in Bild 2 dargestellt. Die unbehandelte stranggepresste Oberfläche ist von einer etwa 50 nm dicken Oxidschicht bedeckt. Eine undefinierte inhomogene Morphologie zeichnet die Oberfläche aus. Durch den Laser wird eine oberflächennahe Schicht zu einer definiert strukturierten Morphologie umgeschmolzen. Die entstandene Oxidschicht ist um ein Vielfaches dicker und weist eine nanoporöse Struktur auf, die eine optimale Anbindungsfläche für Klebstoffe bietet.