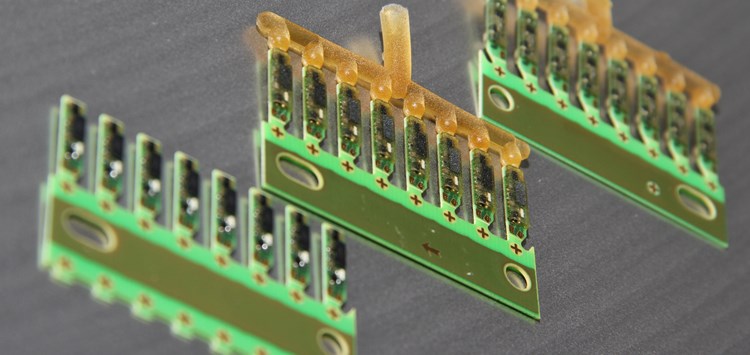
(Bild: OptiMel)
12.07.2024 LPM: Projektspezifisch das optimale System auswählen
Leitfaden zur Auswahl eines Low Pressure Moulding Systems
Mit dem Low Pressure Moulding (LPM) einem Verfahren zum Verguss und Schutz elektrischer und elektronischer Bauteile, lassen sich z.B. Leiterplatten oder Sensoren vor äußeren Einflüssen wie Vibrationen, Stößen und Erschütterungen schützen. LPM isoliert gegen Wärme, Kälte, Feuchtigkeit, Witterung im Allgemeinen sowie elektrische Energie. Die Formgebung ist platzsparend, kostengünstig und individuell designbar. Die Technik eignet sich auch zum Formen von Tüllen und Zugentlastungen, z.B. bei Steckverbindern. Entscheidend ist, dass die Anlage zu den Projektanforderungen passt.
Im LPM kommen überwiegend amorphe thermoplastische Polyamide und Polyolefine zum Einsatz. Sie verbinden ein günstiges Viskositätsspektrum mit einem breiten Anwendungstemperaturbereich von -50 bis 150 °C. Das zu schützende Bauteil wird in ein speziell für dieses Projekt konzipiertes Vergusswerkzeug eingelegt und mit dem Vergussmaterial ummantelt. Dafür wird das Vergussmaterial typischerweise bei 180 bis 240 °C erhitzt, bis es flüssig ist. Dieses Material wird anschließend bei sehr niedrigem Druck, typischerweise zwischen 5 und 25 bar, in ein relativ kaltes Formwerkzeug eingebracht. Je nach Equipment und Anforderung lässt sich ein Einspritzdruck bis zu 40 bar bzw. 60 bar, aber auch unter 5 bar realisieren. Die Werkzeugtemperatur sollte abhängig von den Prozessanforderungen zwischen Raumtemperatur und ca. 60 °C betragen. Unter diesen Voraussetzungen fließt das Material in die Vergusskavität und umschließt die zu schützende Elektronik. Ist die Kavität gefüllt, wird durch nachfließendes Material der voreingestellte Druck erzeugt und der Materialschrumpf reduziert. Sobald das Material auf die Außenwände der formgebenden Vergusskavität trifft, beginnt gleichzeitig der Kühlprozess. Ein typischer vollständiger Formgebungszyklus dauert zwischen 10 und 60 s. Anschließend ist die direkte Weiterverarbeitung ohne zusätzliche Kühl- oder Reaktivierungszeiten möglich.