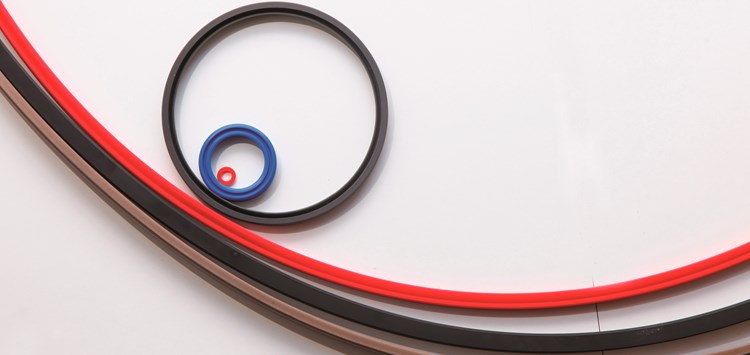
Von groß bis klein – mit der CNC-Technik lassen sich schnell die richtigen Dichtungen fertigen, bei Bedarf in Losgröße 1 für Erstausrüstung und Instandhaltung (Bild: xpress seals GmbH)
18.03.2019 Großdichtungen stellen besondere Anforderungen
Bewährte und neue Verabeitungstechniken und neue Materialien sinnvoll kombinieren
Viele Maschinen werden größer und laufen unter extremen Bedingungen. Für Großdichtungen bedeutet diese Entwicklung größere Durchmesser und eine größere Werkstoffvielfalt. Mit dem entsprechenden Know-how lassen sich die anstehenden Aufgabenstellungen allerdings lösen.
Dichtungen mit einem Durchmesser von > 600 mm werden nomalerweise als Großdichtungen (Bild 1) bezeichnet. Für diese gelten andere Rahmenbedingungen als für Dichtungen mit kleineren Durchmessern. Bei Erstausrüstern (OEM-Bereich) kommen sie meist im Groß- und Schwermaschinenbau zum Einsatz. Da es sich dabei meist um Sondermaschinenbau andelt, werden die Dichtungen in der Losgröße 1 oder als Kleinserie benötigt. Darüber hinaus kommen kaum standardisierte Dichtungen zur Anwendung. Eine weitere Besonderheit ist, dass die großen Maschinen, in denen solche Dichtungen zum Einsatz kommen, im Schadensfall aus Kostengründen meist nicht ersetzt, sondern repariert und dabei i.d.R. nachbearbeitet werden. Dies erfordert eine hohe Anpassungsfähigkeit des Dichtungslieferanten. Durch die Nachbearbeitung entstehen veränderte, vom Standard abweichende Einbauräume, die mit Normmaßdichtungen nicht wirksam gefüllt werden können. So ist beinahe jeder Anwendungsfall ein anderer: Es müssen auf die neuen Gegebenheiten zugeschnittene Dichtungen her – im wahrsten Sinne des Wortes.
Breites Einsatzspektrum
Die Einsatzgebiete von Großdichtungen reichen vom Schiffsbau über die Stahlindustrie, chemische Industrie, Wasserkraft, Schwerhydraulik bis zu Windkrafträdern. Sie kommen in vielen Anlagen und Komponenten zum Einsatz, z.B. in Leitschaufeln bei Kaplan- und Francisturbinen, Laufschaufeln bei Kaplanturbinen, Düsenregelungen bei Peltonturbinen, Servomotoren, Schiebern über die Öl- und Wasserhydraulik sowie in Scheren, Schreddern von Metall-Recyclinganlagen („Schrottplätzen“), Manipulatoren, Karosseriepressen, Pfannenkippzylindern, Stopfzylindern, Walzen- und Walzenanstellzylindern, Stripperkränen, Schmiedepressen und Schmiedehämmern, Ruderschäften, Schiffstabilisatoren, Rudermaschinen, Azimutbremsen, Pitchzylindern, Pulse Encoder, Haupt- und Nebengetrieben, Bremsen, Akkumulatoren, Verriegelungsdichtungen von Windkraftanlagen etc.
Für diese Anforderungen an die Dichtungsherstellung ist die CNC-Drehtechnik die richtige und zudem sehr bewährte Methode. Dieses Fertigungsverfahren besitzt die erforderliche Flexibilität, individuellen Anforderungen gerecht zu werden. Die Auswahl an vorhandenen Dichtungsprofilen lässt keine Wünsche offen und deckt ein großes Anforderungsspektum ab. Über 300 programmierte und schnell abzuändernde Dichtungsbauformen stehen zur Verfügung. Und im besonderen Bedarfsfall können Zerspanungstechniker das Profil manuell codieren. So unterliegt diese Produktionstechnik keiner Einschränkung in Bezug auf Dimension und Profil. Neben den Standarddichtungen gehört, vor allem im Bereich der Großdichtungen, die Zukunft der Drehtechnik. Sie bedient die Forderung nach qualitativ hochwertigen Einzelanfertigungen, die sehr schnell produziert und geliefert werden können. Damit erfüllt diese Technik eine zentrale Anforderung, da die Beschaffungszeitfenster immer knapper werden. Meist entstehen durch das Versagen einer Dichtung öfters teurere Maschinenstillstände und damit für den Kunden Notsituationen.
Werkstoffvielfalt
Die wichtigsten Werkstoffe für die Herstellung von Dichtungsdrehteilen bis 1.500 mm Durchmesser sind:
• wasserstabiles, qualitativ hochwertiges rotes Polyurethan mit einer Shorehärte von 95A,
• schwarzes mit Shore 70D, Nitrilkautschuk (NBR) mit 85 Shore A und 73 Shore A,
• reines weißes lebensmittelkonformes Polytretrafluorethylen (PTFE),
• ein PTFE-Compound mit 40 % Bronze,
• PTFE-Kohle-Compounds und PTFE-Glasfaser mit Molybdändisulfid. CNC-Fertiger liefern heute Dichtungsteile aus diesen hochqualitativen Standardwerkstoffen sowie aus verschiedenen PTFE-Compounds, PEEK, Compounds von Polyamiden und Polyimiden, PETP u.v.m. Dabei sind viele Werkstoffe verfügbar, die sich auch in Branchen mit speziellen Anforderungen, wie z.B. dem Lebensmittelbereich, einsetzen lassen. Aktuell werden immer mehr Lösungen für höchste Anforderungen gesucht. Dazu zählen z.B. Tieftemperaturanwendungen. Hier haben sich – abgesehen von den erwähnten PTFE und PTFE-Compounds – auch TT-NBR (Tieftemperatur-NBR) mit 85 Shore A und TT-PU (Tieftemperatur-Polyurethan) mit einer Härte von 94 Shore A bewährt, die sich bis -50 °C einsetzen lassen.
Ein weiteres Thema sind lebensmittelkonforme und für Trinkwasser-Anwendungen geeignete Elastomere. Auch hier gibt es heute Lösungen, die als Großdichtung schnell zur Verfügung stehen. Grundsätzlich ist jeder am freien Markt erhältliche und drehtechnisch zu verarbeitende Werkstoff zu nutzen. Genaue Absprachen, inkl. der chemischen Beschreibung des eingesetzten Mediums, gestalten die Suche nach der besten Lösung schnell und effizient.
Schnelles Prototyping und effiziente Lösungen
Im Zweifel kann der Konstrukteur oder Anwendungstester heute für statische Dichtungen und dynamische Dichtsysteme den schier unerschöpflichen Variantenreichtum bei der Dichtungsgestaltung nutzen, den die CNC-Technik bietet. Mithilfe der genannten Werkstoffe kann das Verhalten verschiedener Designs in Kombination mit verschiedenen Werkstoffen sehr schnell und zielführend getestet werden. Innerhalb weniger Minuten können die Prototypen einer optischen und haptischen Prüfung unterzogen werden, um sich sofort für eine Dichtung entscheiden zu können oder den einen oder anderen Typ in einem Feldversuch zu testen. Der Vorteil der CNC-Fertigung ist, dass man sofort eine Nullserie bzw. bei entsprechendem Mengenbedarf formgebundene Dichtungen herstellen lassen kann (Bild 2).
Die xpress seals GmbH ist auf die Anwendung von drehtechnisch hergestellten Artikeln spezialisiert. Bis zu einem Durchmesser von 1.500 mm sind die genannten Werkstoffe lagernd, was eine Auslieferung am Tag der Bestellung erlaubt. Zusammen mit Lieferanten werden Werkstoffe, die sich im Laufe der Jahre als Standardwerkstoffe entwickelt haben, wie z.B. ein PTFE-Compound, gefüllt mit 23 % Kohle und 2% Grafit, vorgehalten. Die CNC-Technik für Dichtungen ist immer nur so gut wie das Fachpersonal, das die Maschinen bedient. Entscheidend ist hier, mit viel Knowhow die richtigen CNC-Programme für Dichtungsprofile zu erstellen. Neben modernsten CNC-Drehmaschinen stehen als qualitätsstützende Maßnahmen metallische Messdorne zur Verfügung. Ein bildgestütztes Messsystem und ein modernes Werkzeugvoreinstellgerät sichern ebenfalls das passgenaue Arbeiten, genauso wie Messschieber und Umfangsmaßbänder für die Qualitätskontrolle. Aktuell werden die Möglichkeiten um ein mobiles Mikroskop zur Beurteilung der Oberflächenqualität erweitert. Sofern erforderlich, wird für jede Dichtung ein Werkszeugnis ausgestellt. Dies umfasst die verwendeten Werkstoffe, die Bauform und die exakten Abmessungen. Bei Bedarf werden spezifische Abnahmen der Produkte durch die Kunden durchgeführt.
Fazit und Ausblick
Da auch Anlagen immer größer werden, ist geplant, die bestehenden Anlagen auf größere Durchmesser zu erweitern. Derzeit können über einen Produktionspartner Großdichtungen mit Durchmessern bis von 16.000 mm gefertigt werden. Dabei kommt allerdings nicht die CNC-Drehtechnik zum Einsatz und es wird auch mehr als ein Tag bis zur Auslieferung benötigt. Parallel dazu wird die sofort verfügbare Werkstoffpalette kontinuierlich ausgebaut, da immer mehr Dichtungsanforderungen heute werkstoffseitig und weniger häufig konstruktiv gelöst werden.
Fakten für Konstrukteure
• Für Großdichtungen bis 16.000 mm Durchmesser stehen heute immer mehr Werkstoffe zur Verfügung, mit denen sich steigende Anforderungen lösen lassen
Fakten für Einkäufer
• CNC-gedrehte Dichtungen können meist am selben Tag ausgeliefert werden, was die Anlagenstillstände minimiert
Fakten für Instandhalter
• Bei nachbearbeiteten Dichtstellen empfiehlt sich die enge Abstimmung mit dem Lieferanten, da Normmaßdichtungen selten die neuen Einbauräume zuverlässig abdichten
Werkstoffübersicht für Großdichtungen
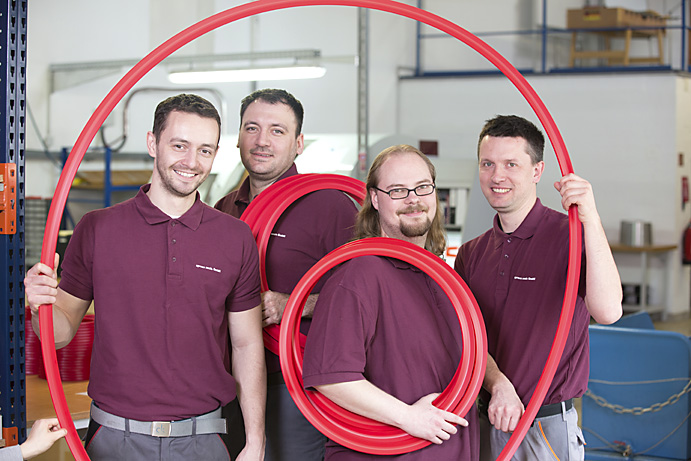
Bild 1: Großdichtungen erfordern viel Know-how in allen Bereichen (Bild: xpress seals gmbh)