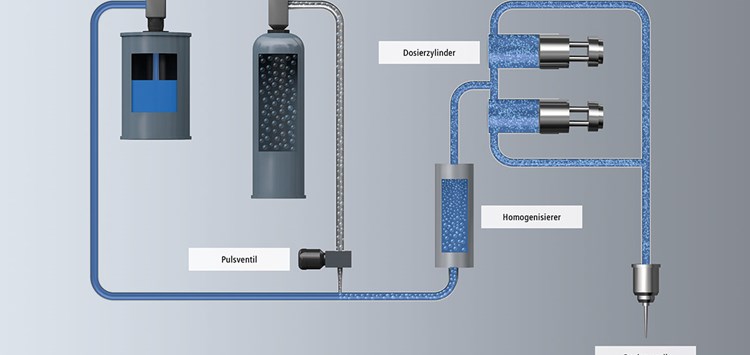
Schematische Darstellung des Anlagenprinzips der CeraFLOW®-Technologie (Bild: CeraCon GmbH)
01.11.2018 Ein Konzept für viele Anwendungen
Flexible Anlagentechnik für flexibel geschäumte 1K-PUR-Dichtungen auf Basis eines Materials
Industrielle Produktionsprozesse stellen häufig sehr unterschiedliche Anforderungen an Material und Dosieranlage. Bei Gütern, die in großen Stückzahlen hergestellt werden, steht die Produktivität mit präziser Applikation und Reproduzierbarkeit im Vordergrund. Darüber hinaus sollen aber häufig verschiedene Bauteile unterschiedlichster Geometrien und Dichtungsanforderungen auf derselben Anlage produziert werden. Stillstandszeiten durch Umrüsten der Anlage sollen dabei selbstverständlich möglichst gering gehalten werden. Ein 1K-PUR-Dichtungskonzept aus Schaumdosieranlage und dem entsprechenden Material zeigt einen Lösungsansatz auf.
Innerhalb der Verfahren zum In-situ-Auftrag flüssiger, geschäumter Dichtungen (FIPFG=Formed In-Place Foam Gaskets) nimmt die 1K-PUR-Technologie eine Sonderstellung ein. Hier wird das Dichtungsmaterial (Bild 1) in einem ersten Schritt mithilfe einer Schäumanlage physikalisch geschäumt und als formstabile Dichtraupe appliziert. Die Aushärtung der reaktiven Masse erfolgt im darauffolgenden Schritt per Wärmeeintrag in einem Ofen innerhalb weniger Minuten. Durch diese Trennung von Schaumgenerierung und Aushärtung ergeben sich einige Vorteile gegenüber klassischen mehrkomponentigen Dichtungssystemen:
- feinporiger Schaum mit einer überwiegend geschlossenzelligen Struktur
- hohe Präzision selbst bei kleinen Dimensionen ohne Nut (< 1,5 mm)
- 3D-Applikation möglich
- klebfrei direkt nach dem Ofen
- Verbau nach Abkühlung des Bauteils möglich
- unterschiedliche Raupendimensionen in einer Anwendung realisierbar
- schnelle Abänderung der Materialeigenschaften durch Variation des Luftanteils
- hohe Prozesssicherheit und Auslastung des Equipments (> 95 %)
- kein Spülen oder Wechseln des Dosierkopfs bei Applikationspausen
- kein Anfall von Sondermüll
Grundkonzept der Anlagentechnik
Die Aufbereitung der zähflüssigen PUR-Rohmasse zum Schaum erfolgt, insbesondere bei der CeraFLOW®-Anlagentechnik (Bild 2), nach folgendem Prinzip: Zunächst wird die Rohmasse durch eine Schöpfkolbenpumpe aus dem Materialgebinde gesaugt und über eine Leitung zur eigentlichen Schäumanlage gefördert. Hier wird eine Kolbenpumpe mit dem Rohmaterial gefüllt. Anschließend fördert diese das aufzuschäumende Material mit definiertem Druck und konstanter Fördergeschwindigkeit zu einem Hochdruck-Gasinjektionsventil. Mithilfe dieses Ventils werden in den Materialstrom kleine Gasblasen injiziert. Als Arbeitsgas kann dazu Druckluft verwendet werden. Der Luftdruck muss hierfür höher als der Materialdruck am Ort der Gasinjektion sein und in einem definierten festen Verhältnis zum Materialdruck stehen. Üblicherweise liegt der Gasdruck bei 120 bis 140 bar. Der hohe Gasdruck wird direkt in der Anlage mit einem Verdichter erzeugt, sodass eine spezielle Versorgung mit z.B. Gasflaschen entfällt. Die Prozessluft wird zudem in der Anlage über einen Lufttrockner und Feinfilter aufbereitet, sodass ein üblicher Druckluftanschluss genügt.