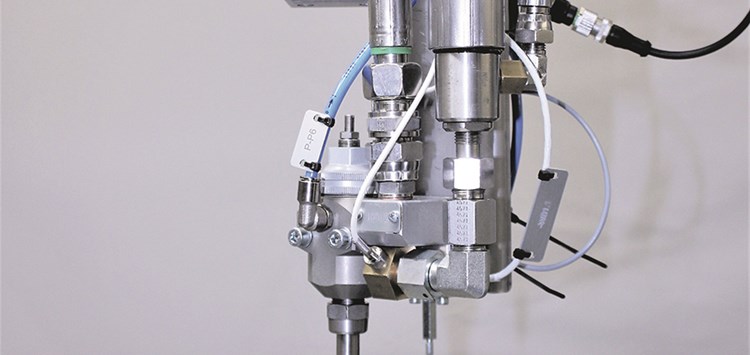
Klimatisiertes Dosiersystem (Bild: DoBoTech AG)
17.09.2018 Effizienz ist überall was anderes
Global effizient dosieren und angepasst automatisieren
Die Automobilbranche fertigt global und mit einem hohen Automatisierungsgrad. Effizienz beim Dosieren entsteht aber erst mit einer auf den jeweiligen Produktionsstandort abgestimmten Technik.
Prozessübergreifende Technologiekombinationen, projektangepasste Automatisierungslösungen sowie eine qualifizierte Abbildung aller Prozesse nach Kundenstandards gehören in dieser Branche zum Alltagsgeschäft. Die geforderten Lösungen bewegen sich dabei in einem Spannungsfeld zwischen immer kürzer werdenden Produktentwicklungszyklen, z.B. bei der E-Mobilität, sich ändernden Produkt-, System- und Qualitätsanforderungen sowie dem Trend zu mehr Varianten, die eine Flexibilisierung der Montagelinien bedingen. Die Globalisierung bringt es zudem mit sich, dass die Systeme den klimatischen Anforderungen einer Region oder den unterschiedlichen Automatisierungsgraden in Schwellen- und Industrieländern gerecht werden müssen.
Ein weiterer Aspekt ist die Qualitätsüberwachung des Dichtmittelauftrags, denn Dichtungen tragen erheblich zur Qualität eines Fahrzeuges und zu seiner Funktionalität bei. Vor dem Hintergrund der unterschiedlichen klimatischen Verhältnisse, aber auch hinsichtlich der zunehmenden Anzahl einzusetzender Dichtmittel mit z.B. extrem hohen Extrusionsraten-Toleranzen gilt es, schwankende Dichtmittel-Prozessparameter zu kompensieren, um die geforderte Qualität der Dichtungen sicherzustellen.
Angepasste Technik
Dies hat zur Entwicklung spezieller Dosiersysteme geführt, die den genannten unterschiedlichen Anforderungen Rechnung tragen (Bild 1). So kommen z.B. in klimatisch „heißen“, zumeist Low-Tech-Regionen, klimatisierte Dosiersysteme zum Einsatz. Hinsichtlich des Dosierverfahrens sind bei der DoBoTech AG inzwischen volumetrische Dosiersysteme die bevorzugte Standard-Dosiertechnik. Das Problem der stark variierenden Dichtraupenbreiten bedingt durch die Extrusionsraten-Toleranz, wurde mit einem proportional regelnden Volumen-Dosiersystem gelöst (Bild 2). Der entscheidende Vorteil ist, dass ein zur Vorschubgeschwindigkeit proportional konstantes Dosiervolumen appliziert werden kann. Zusätzlich werden mit diesem System die unerwünschten „Kleckse“ an Start- und Endpunkten eliminiert. Einstellbare Öffnungs- und Schließgeschwindigkeiten des Ventils erlauben die Überlappungen der Dichtmittelraupe auf konstante Breiten- und Höhenmaße. Dies ist – im Vergleich zum Nassverbau – insbesondere bei der Herstellung von CIPG- (Cured-In-Place-Gasket) Dichtungen – eine unabdingbare Voraussetzung.
Die Qualitäts- und Prozessüberwachung erfolgt durch maßgeschneiderte, auf den Anwendungsfall abgestimmte Systeme. Angefangen bei einer druckbasierten Dosierkontrolle DQM (Dosing Quality Measurement), kommen u.a. klassische stationäreund InProcess-Kamerasysteme sowie 3D-Lasertriangulations-Überwachungssysteme unterschiedlicher bzw. durch den OEM vorgegebener Anbieter zum Einsatz.
Praxis High-Tech-Standort – Serie vs. Prototyp
Ein E-Mobility-Projekt aus Deutschland eignet sich gut, die Unterschiede im Automatisierungsgrad zwischen Serien- oder Volumen-Montagelinien aufzuzeigen, die mit sehr kurzen Taktzeiten arbeiten. Ihnen werden Dosieranlagen für Entwicklungs- oder Prototypen-Abteilungen gegenübergestellt, die – aufgrund anderer Aufgabenstellungen – nicht so eng getaktet sein müssen.
Bei dem Projekt kommen CNC-Dosieranlagen sowie Roboter-Dosier- und Lagerzellen für die Elektromotoren-Montage zum Einsatz. Die Serien- oder Volumenlinien sind aufgrund der zu produzierenden Stückzahlen und der Variantenvielzahl mit Runddrehtischen ausgestattet. Sie erlauben eine simultane, taktzeitoptimierte Be- und Entladung der Anlage während der Dosierung. Das Bauteilhandling und die Fügeprozesse sind voll automatisiert. Mit den Lager-, Speicherzellen werden per Linienverkettung die Varianten just in time gesteuert. Die Bauteilaufnahmen sind aufgrund der vielen Varianten, die mit jeder Anlage verarbeitet werden, spezifisch gestaltet. Die Dosiersysteme sind als volumetrische Hochdrucksysteme ausgeführt und die Überwachung übernehmen stationäre Kamerasysteme.
Im Gegensatz hierzu wurde im Vorfeld des Projektes eine Dosieranlage für die Entwicklungs- und Prototypenfertigung gezielt auf Flexibilität ausgelegt. Zentrales Kennzeichen dieser Station ist eine multifunktionale Bauteilaufnahme (Flex-BTA) (Bild 3). Dieses Konzept ermöglicht die Dosierung aller Bauteilvarianten und unterschiedlichster Motortypen mit minimalem Rüstaufwand auf einer Bauteilaufnahme. Aufgrund der geringeren Stückzahlen und des damit verbundenen geringen Materialverbrauchs übernimmt ein volumetrisches Kartuschendosiersystem die Dosierung. Eine visuelle Werker-Eigenprüfung ersetzt die Kameraprüfung.
Praxis Dosiertechnik & Automatisierung – High- vs. Low-Tech-Region
Da Pkw- und Motorrad-OEM-Kunden im Powertrain Segment immer häufiger eine CKD-(Completely Knocked Down) Strategie verfolgen, um die vorgeschriebenen Local-Content-Vorgaben in Wachstums- und Schwellenländern zu erfüllen, etablieren sie dort eigene Produktions- und Montagestandorte. Die Unterschiede in der Fertigung liegen hier z.B. im angepassten Automatisierungsgrad, aber auch weiteren, standortbezogenen Besonderheiten.
Das bedeutete bei diesem Projekt, teilautomatisierte CKD-Maschinen, im Vergleich zu vollautomatisierten Serienproduktionsanlagen, aus Prozessqualitätsgründen so seriennah wie möglich auszuführen. Für die benötigte Variabilität werden multifunktionale Bauteilaufnahmen verwendet, die man aus ergonomischen Gründen mit Handling-Tools bestückt. Diese Hilfsmittel (Bild 4) reduzieren zudem das Risiko, die Dichtmittelraupe beim manuellen Fügen zu beschädigen. Darüber hinaus müssen die Bauteile hier gegen einen Festanschlag ausgehoben und ausgerichtet werden, um die geforderte Ebenheitstoleranz für die Dichtmittelapplikation zu gewährleisten.
Der Faktor „Klima“ (die Systeme werden bei Temperaturen > 40 °C eingesetzt) führt dazu, dass die erlaubte Temperatur hinsichtlich der Dichtmittel-Lagerstabilität überschritten wird. Deshalb kommt ein klimatisiertes Dosiersystem zum Einsatz. Das Dichtmittel wird über die gesamte materialführende Strecke, vom Produktspeicher bis zum Dosierventil, mit einem autarken Klimasystem auf die max. zulässige Temperatur klimatisiert. Der Einfluss der Temperatur auf die Viskosität des Dichtmittels ist somit eliminiert.
Ausblick
Aktuell lassen sich zwei Trends feststellen. In hoch industrialisierten, zumeist westeuropäischen Ländern, geht die Entwicklung vom klassischen Dosiertechnik–Sondermaschinenbauer, oftmals als Unterlieferant eines GU (Generalunternehmers), hin zum Systemlieferanten für voll automatisierte und verkettete Dosierstationen. Diese Zellen-Konzepte beinhalten u.a. die komplette Bauteilhandling-Automatisierung, inkl. der Varianten-Lagerverwaltung mit Speicherregalen und einer linienverketteten Kommunikation. In Asien werden die Konzepte für OEM-Volumen-Montagelinien im Regelfall nur geringfügig angepasst, z.B. an andere Klimabedingungen.
In ostasiatischen und südamerikanischen Low-Tech- und Schwellenländern tendiert man zur CKD-Fertigung, bei der die Herausforderung eher darin liegt, mit einem angemessenen Automatisierungsgrad die bewährten Prozesse seriennah abzubilden. In der Praxis bedeutet dies letztendlich, dass heute jede Dosieranlage ein Unikat ist.
Beide Vorgehensweisen führen zunehmend zu individualisierten Anlagen und erfordern eine partnerschaftliche, vertrauensvolle und interaktive Zusammenarbeit zwischen Anwendern, Lieferanten und Kunden.
Fakten für Konstrukteure
• Der globale Einsatz eines Produktes mit all seinen Aspekten ist auch bei der Konstruktion von Dichtstellen zu berücksichtigen
Fakten für Einkäufer
• Weltweite Standorte und zeitzonen-unabhängige Ansprechpartner, für den Telefon- und Remote-Service, sind ebenso wichtig, wie ausgereifte technische Konzepte und Lösungen, Sondermaschinenbau und eine hohe Fertigungsqualität
Fakten für Qualitätsmanager
• Garanten für Qualität sind Versuche und Tests im eigenen Labor für Entwicklung & Anwendungstechnik sowie ergänzende Workshops und Schulungen
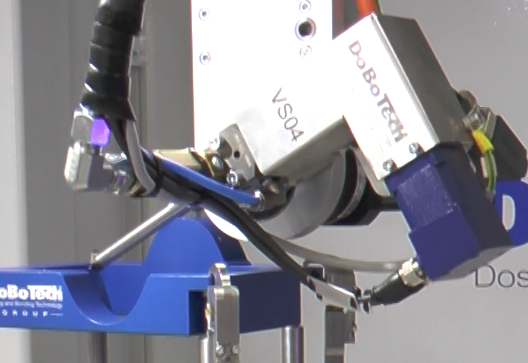
Bild 2: Proportional-Dosiersystem, zusätzlich an 4. Achse, zur 3D-Dosierung (Bild: DoBoTech AG)
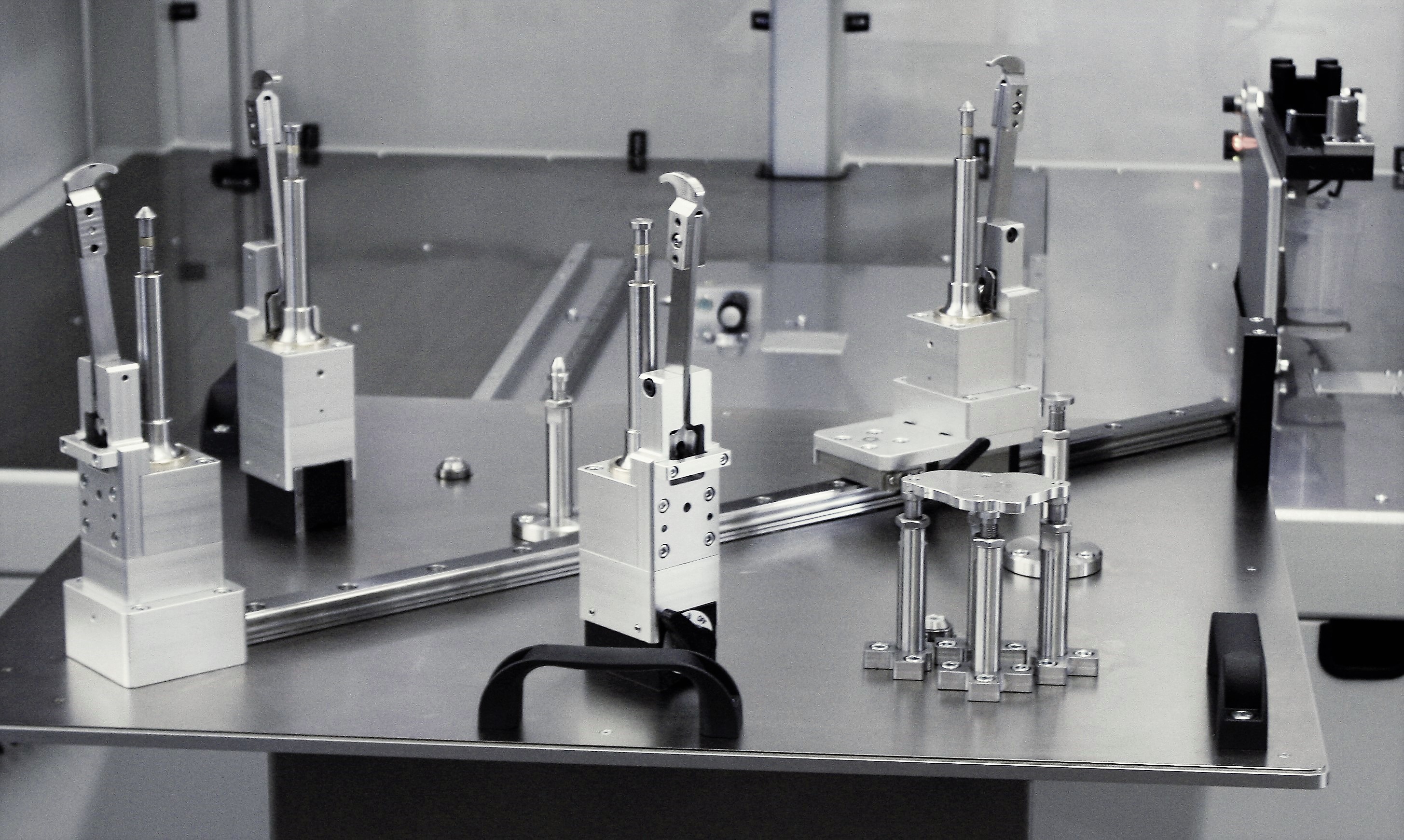
Bild 3: Flex-BTA zur Aufnahme aller benötigen Bauteile (Bild: DoBoTech AG)
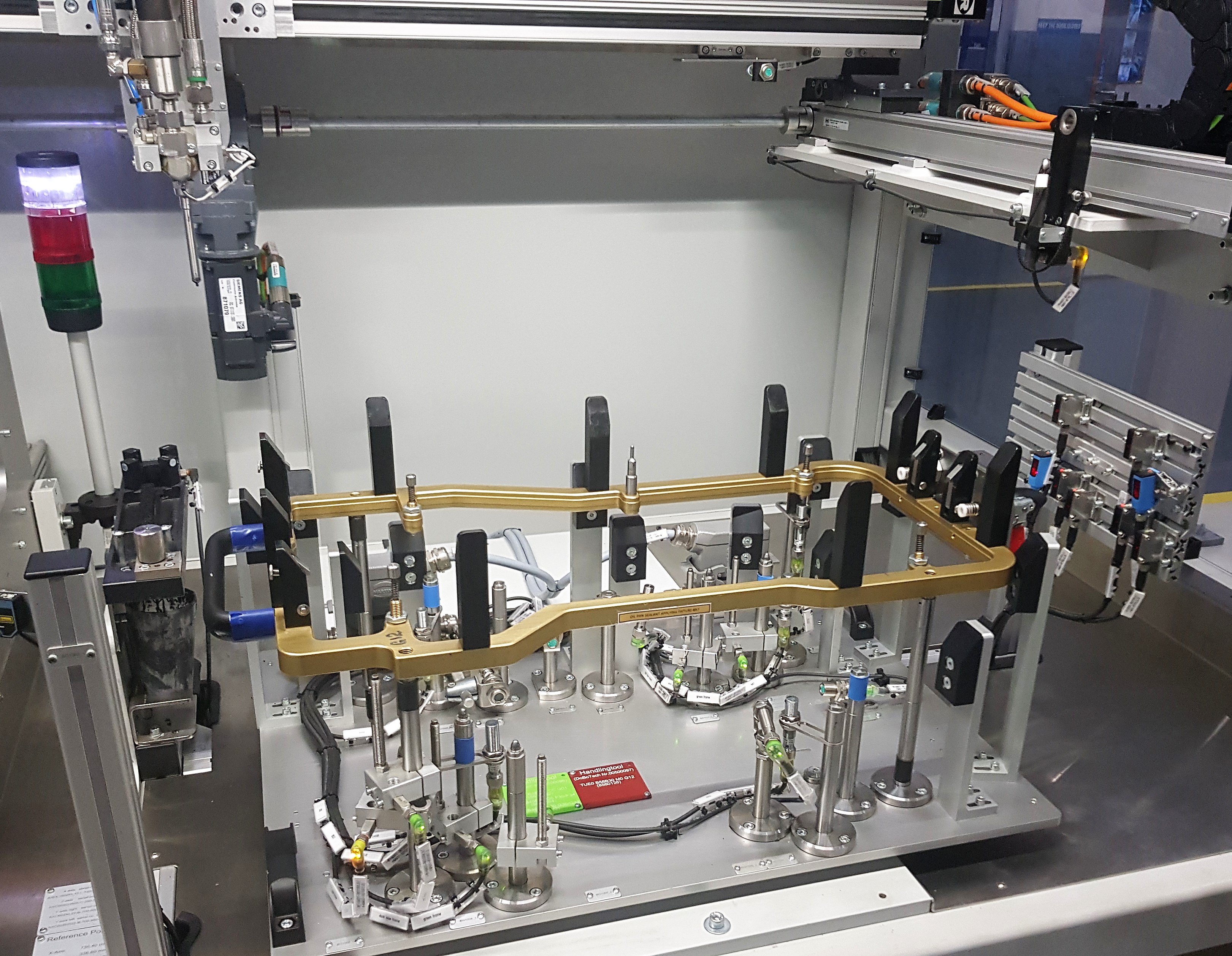
Bild 4: Handling-Tool, für Ergonomie und zum Schutz der Dichtraupe (Bild: DoBoTech AG)
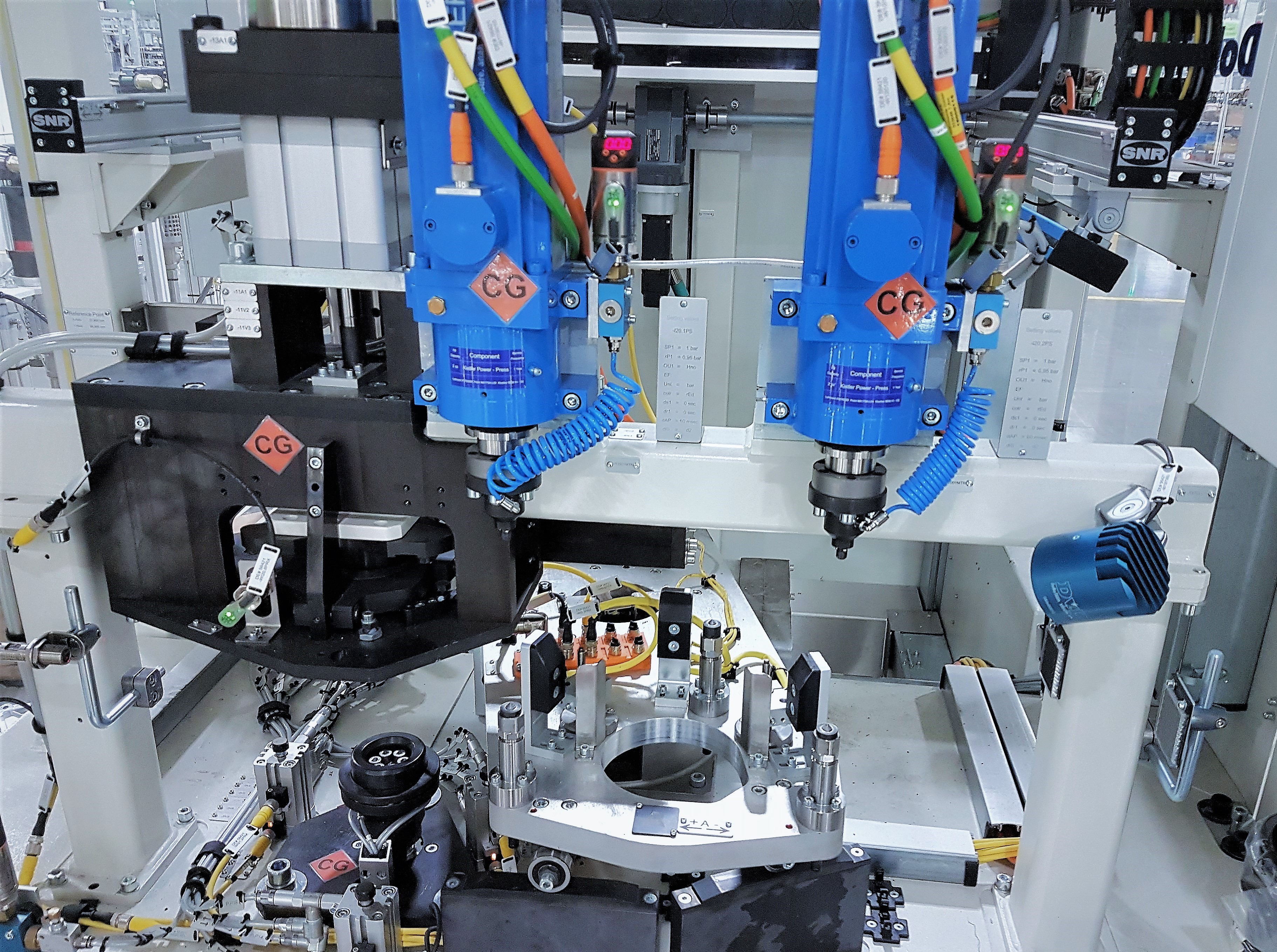
Serienfertigung am High-Tech-Standort (Bild: DoBoTech AG)
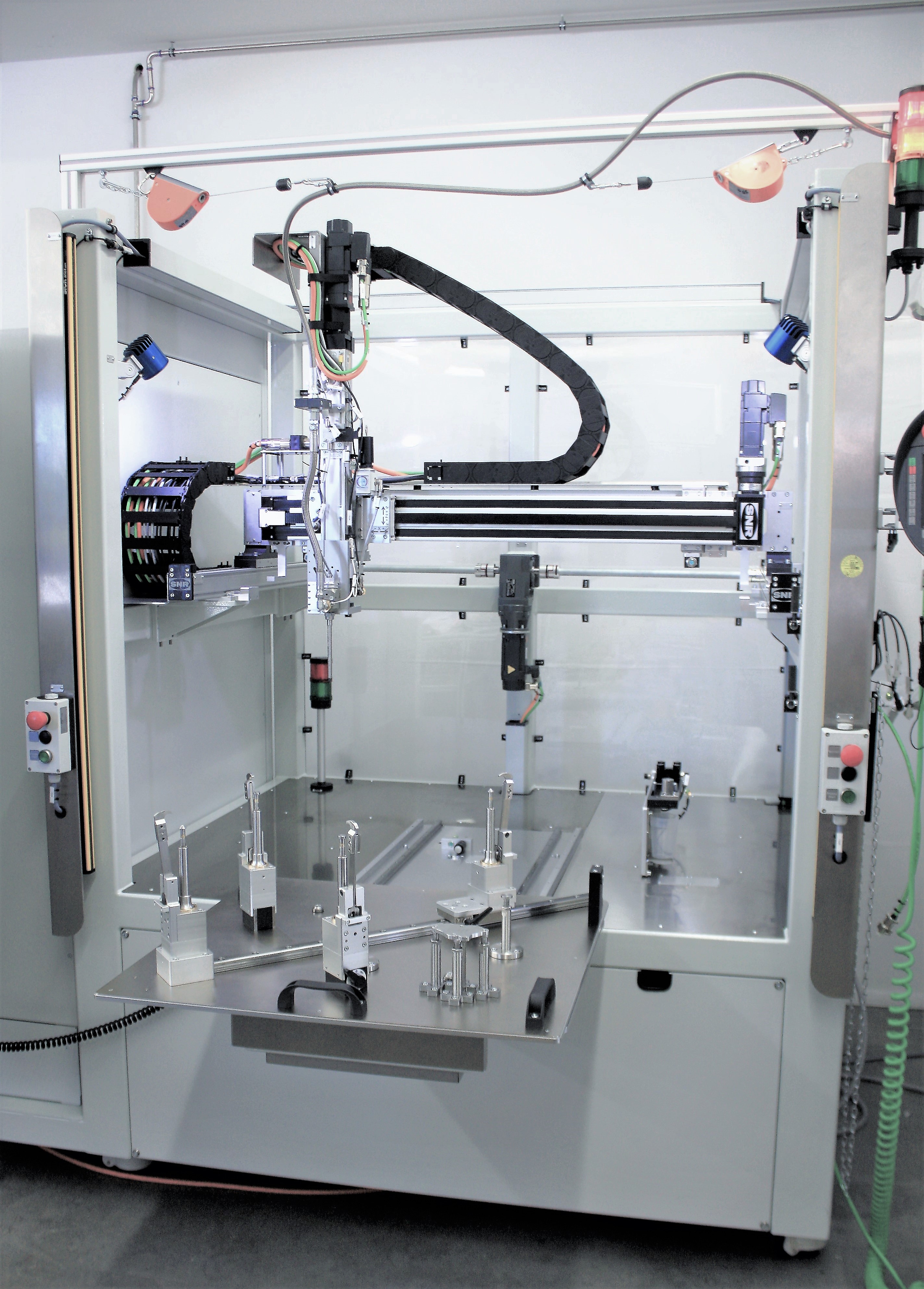
Prototypenfertigung am High-Tech-Standort (Bild: DoBoTech AG)
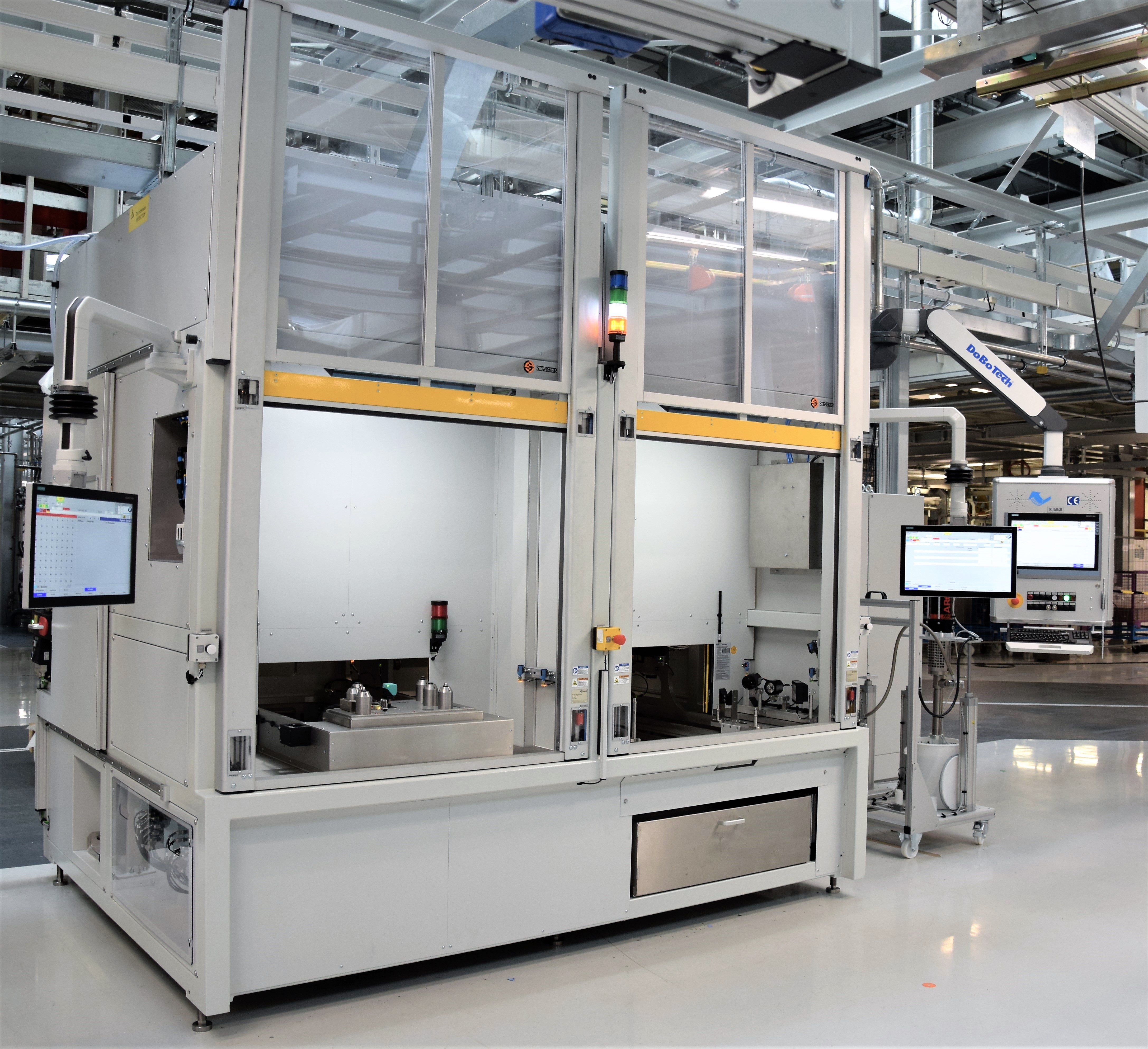
Flex-Linie-CNC-Portal (Bild: DoBoTech AG)
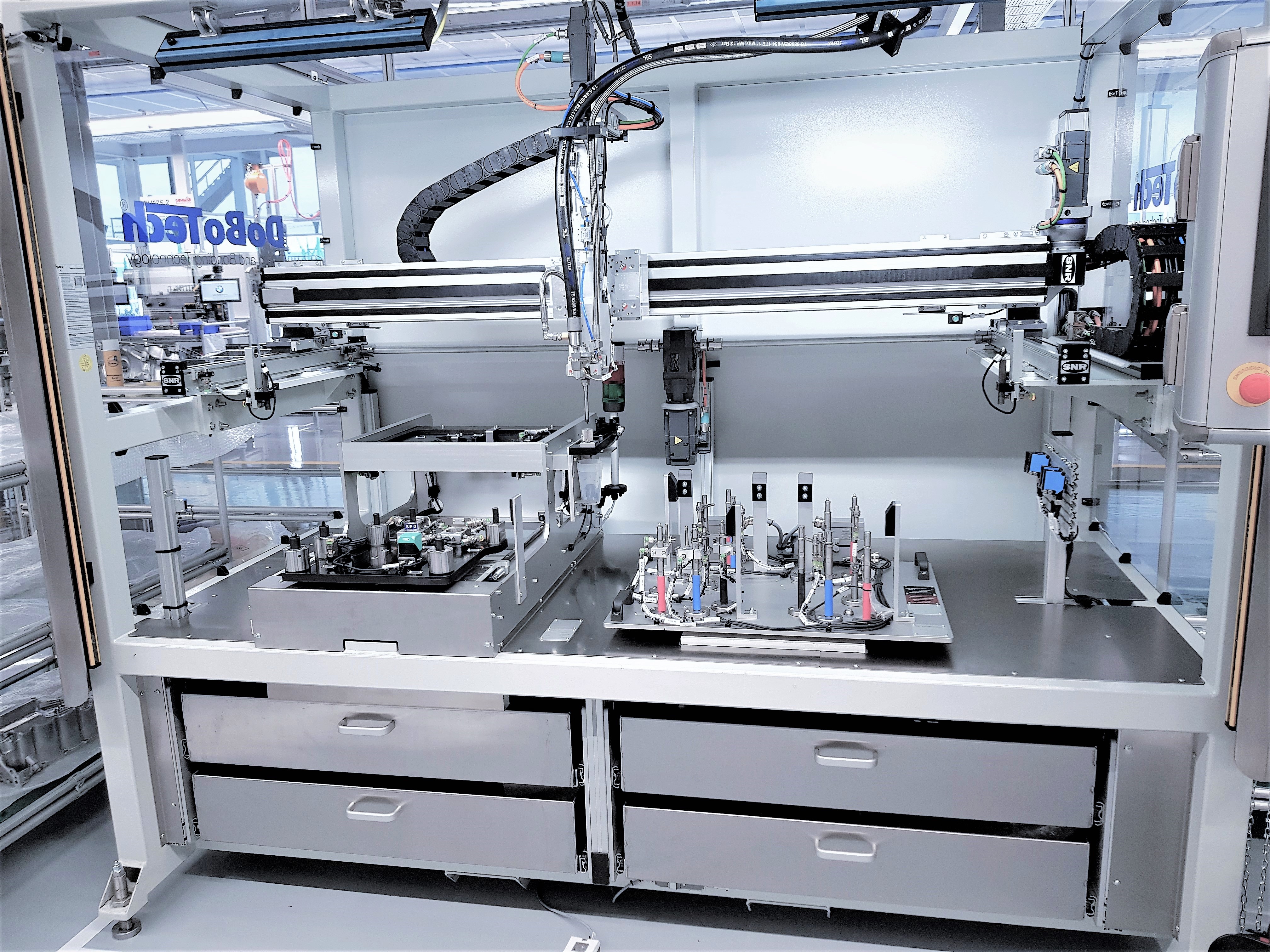
Serienfertigung mit teilautomatisierten CKD-Systemen (Bild: DoBoTech AG)