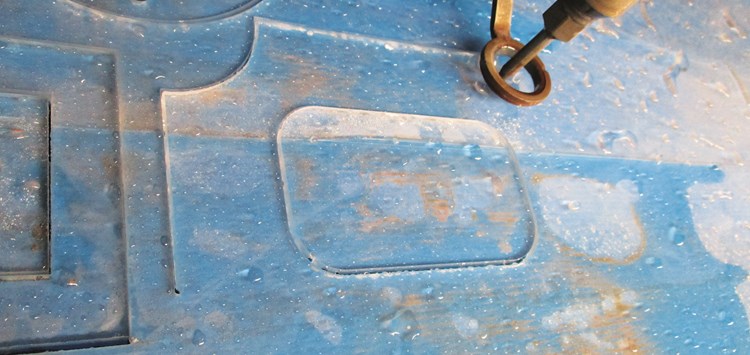
Das Wasserstrahlschneidesystem von STM erleichtert die Wartung und Entwicklung neuer Anlagen für die Umwelttechnik mit geringen Losgrößen (Bild: Geltz Umwelttechnologie GmbH)
17.09.2018 „Dichtungen selbst zu schneiden, hat viele Vorteile für uns“
Wasserstrahlschneidetechnik im Einsatz bei einem Sondermaschinenbauer
Dichtungen beschafft man. Diese Aussage würden viele Maschinenbauer bestätigen. Nicht so Ulrich Geltz, Geschäftsführer der Geltz Umwelttechnologie GmbH, der sich aus verschiedenen Gründen entschieden hat, u.a. seine Dichtungen per Wasserstrahlschneidetechnologie selber herzustellen.
Warum fertigen Sie Ihre Dichtungen überwiegend selbst, anstatt sie zu kaufen?
Geltz: Wir sind Sonderanlagenbauer, d.h. die von uns hergestellten Anlagen sind normalerweise Einzelstücke. Und das bringt auch für Dichtungen ganz unterschiedliche Anforderungen und geringe Stückzahlen mit sich. Unsere Umwelttechnikanlagen sind für unterschiedliche Flüssigkeiten und/oder Gase ausgelegt und arbeiten mit unterschiedlichsten Temperaturen und Drücken. Zudem müssen wir – je nach Anlage – werkstoffseitig umfangreiche Vorgaben erfüllen. Wir haben z.B. gerade eine Anlage ausgeliefert, in der ein (weltweit) standardisiertes Fischwasser hergestellt wird. Diesem Wasser werden in verschiedenen Konzentrationen Testchemikalien präzise automatisiert beigemischt, um in Langzeitversuchen die Auswirkungen auf Fische zu erforschen. Wir durften keine Materialien verwenden, die selbst endokrin wirksame Stoffe abgeben, also, wie z.B. Weichmacher, den Stoffwechsel der Fische verändern oder mit den eingesetzten Chemikalien reagieren. Das würde die Versuche verfälschen. Darüber hinaus müssen wir bei der Anlagenkonstruktion – neben den Verfahrensparametern – den für die Anlage zur Verfügung stehenden Aufstellungsraum, eine möglichst kostengünstige Fertigung sowie eine gute Zugänglichkeit für die Wartung berücksichtigen. Deshalb ist in vielen Fällen der Einsatz handelsüblicher Komponenten nicht möglich und das reicht bis zu Formteilen und Dichtungen.
Welchen dichtungstechnischen Trends müssen Sie in der Umwelttechnik Rechnung tragen?
Geltz: An erster Stelle steht immer die Funktionalität der Dichtung. Natürlich versuchen wir, wenn möglich, auf problematische Stoffe wie Fluorverbindungen zu verzichten. Allerdings gelingt das häufig nicht, weil uns die Einsatzstoffe in unseren Anlagen oft keine Wahl lassen.
Benötigen Sie für die Dichtungsfertigung nicht umfangreiches Werkstoff-Know-how?
Geltz: Natürlich, und das geht weit über die Dichtungen hinaus. Wir müssen alle verwendeten Materialien in Bezug auf Beständigkeit, chemische und physikalische Reaktion mit den Einsatzstoffen, wechselnde Prozesstemperaturen, Alterung, Verschleiß und viele weitere mögliche Versagensfaktoren überprüfen. Häufig haben wir es mit Stoffen und Stoffgemischen zu tun, die in keiner „Beständigkeitsliste“ zu finden sind. Dann stellen wir in unserem Labor die Prozessbedingungen nach und setzen die Materialien den jeweiligen Rahmenbedingungen aus. Auf dieser Basis treffen wir die Materialauswahl und haben so inzwischen auch ein umfangreiches „Dichtungswissen“ aufgebaut.
Wie ist die Qualität Ihrer Dichtungen – verglichen mit zu kaufenden Produkten?
Geltz: Da wir unsere Dichtungen aus zugekaufter Platten- oder Rollenware schneiden, unterscheidet sich die Qualität höchstens in einer etwas größeren Rauheit der Schnittfläche. Bei kritischen Anwendungen arbeiten wir manuell etwas nach. Die Passgenauigkeit unserer Dichtungen ist allerdings häufig besser als die zugekaufter Ware, da wir das gleiche Schnittprogramm für den Sonderflansch und die Dichtung verwenden können. Lediglich die Schneideparameter (Druck, Vorschub etc.) passen wir an das jeweilige Material an.
Warum haben Sie sich für die Wasserstrahlschneidetechnik entschieden – standen andere Verarbeitungstechniken zur Auswahl?
Geltz: Die Wasserstrahltechnik ist für uns das optimale Schneidverfahren, weil wir neben Stahl auch Kunststoffe und wasserfeste Holzplatten verarbeiten. Selbst Magnesium, das sich mit anderen Verfahren nur schwer gefahrlos verarbeiten lässt, schneiden wir.
Welche Anlage setzen Sie ein und was gab den Ausschlag für diese Konfiguration?
Geltz: Wir haben eine 2D-Wasserstrahlanlage von STM mit einer Bearbeitungsfläche von 3 x 1,5 m im Einsatz. Als einzigen Luxus haben wir der Maschine einen Positionierungslaser gegönnt, der uns die Ausrichtung der Werkstücke erleichtert. Damit können wir auch leichter Reststücke aus anderen Schnitten verwenden.
Welche Optionen eröffnen sich durch die eigene Dichtungsfertigung für Ihr Kerngeschäft?
Geltz: Wir sind viel flexibler und in einigen Bereichen unserer Wertschöpfungskette wirtschaftlicher als vorher. Wir haben z.B. praktisch keine Lagerhaltung an Sonderdichtungen mehr. Wenn ein Monteur zum Kunden geht, hat er die Dichtungen, die er im Rahmen der Wartung oder Reparatur austauscht, dabei. Sie wurden vorher in wenigen Minuten gemäß Zeichnungsnummer aus dem definierten Material von seinen Kollegen angefertigt. Parallel dazu holt er das weitere benötigte Material aus dem Lager und erledigt die anderen Vorbereitungen. Müssten wir die Dichtungen beschaffen, bräuchten wir ein Lager, da bei externer Beschaffung – gerade in der heutigen Zeit – manchmal Lieferzeiten von mehreren Wochen üblich sind. Bei neuen Anlagen zahlt es sich aus, dass wir in der Formgebung unserer Anschlüsse viel weniger Beschränkungen haben und so besser auf individuelle Anforderungen eingehen können.
Vielen Dank für das Gespräch.
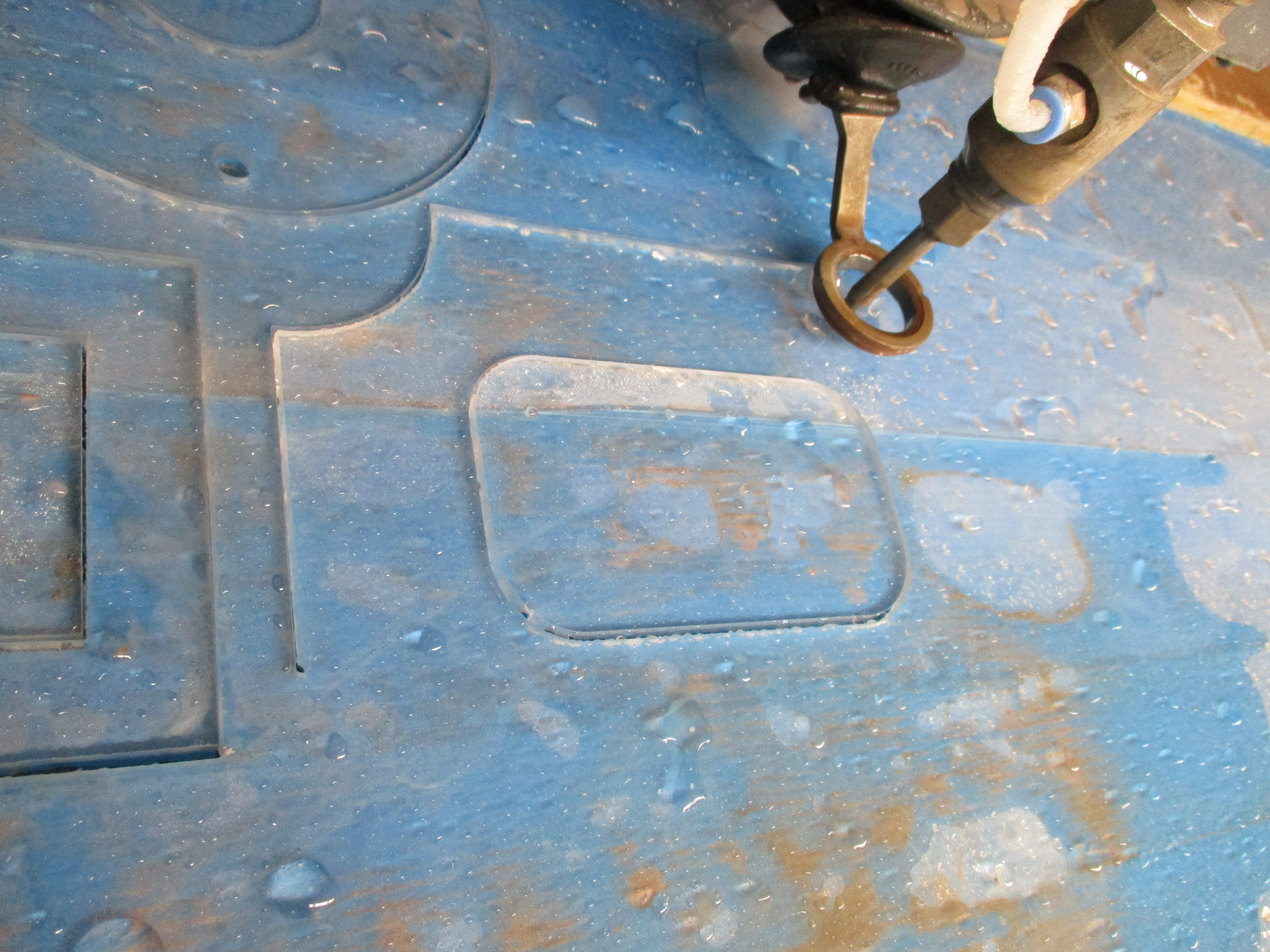
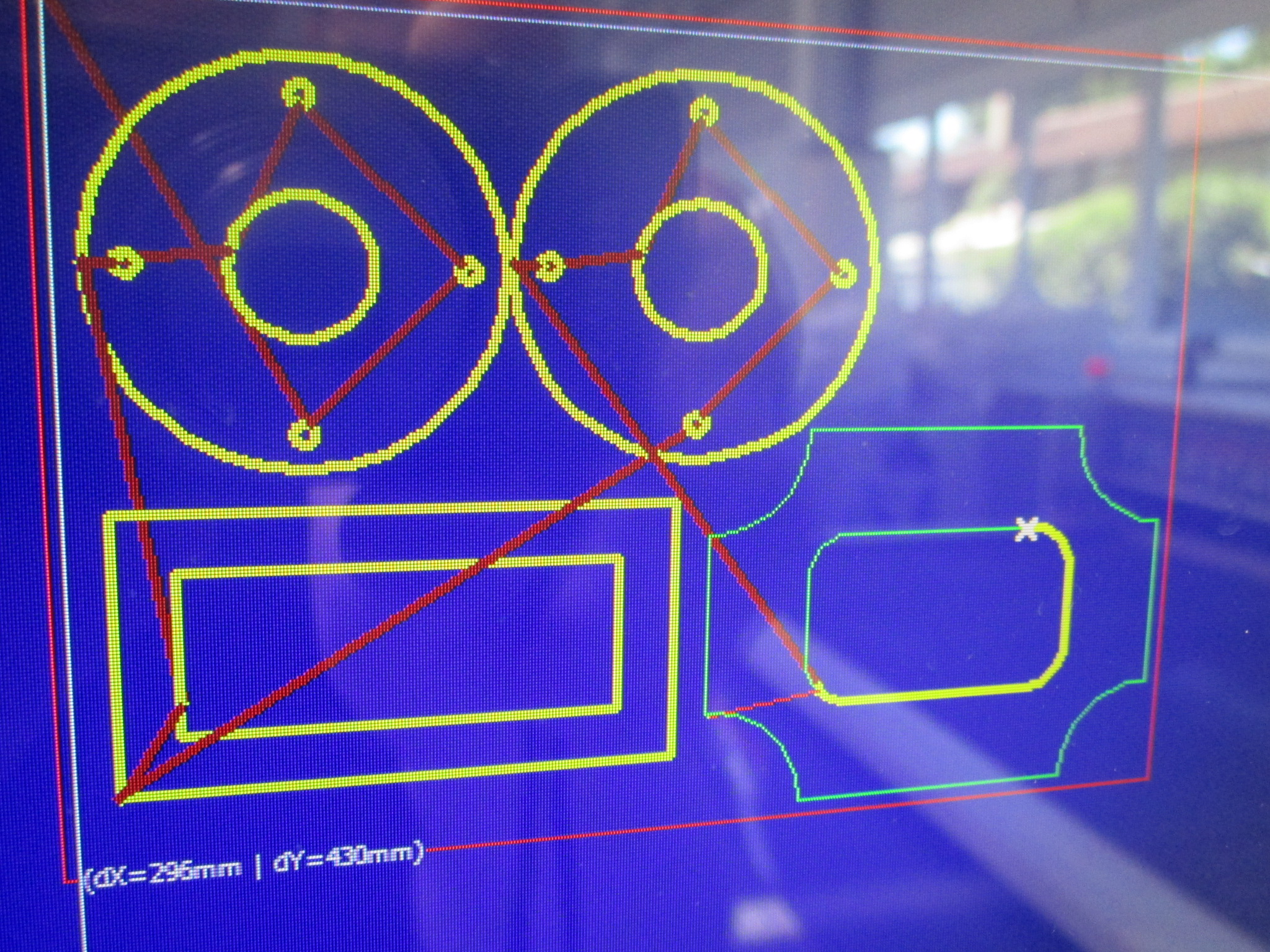
Das Wasserstrahlschneidesystem von STM erleichtert die Wartung und Entwicklung neuer Anlagen für die Umwelttechnik mit geringen Losgrößen (Bild: Geltz Umwelttechnologie GmbH)
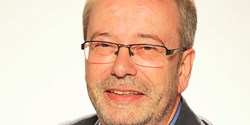
Da wir viele Bauteile aus den unterschiedlichsten Materialien selbst fertigen, ist ein modernes Wasserstrahlschneidesystem optimal für uns.“ Ulrich Geltz, Geschäftsführer, Geltz Umwelttechnologie GmbH