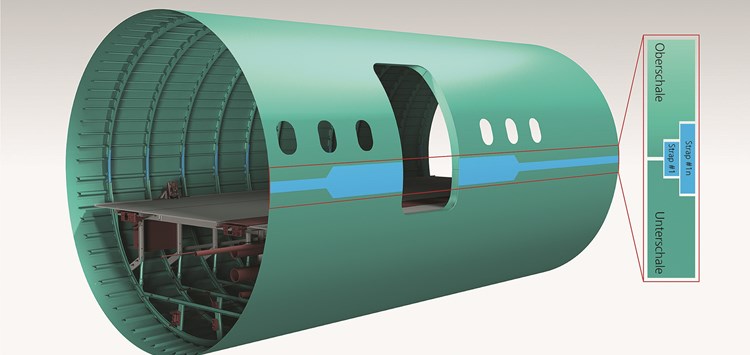
Visualisierung des „Multifunctional Fuselage Demonstrator“ („MFFD“) und der Fügezone des CO2 Laserschweißverfahrens. In Blau dargestellt sind die aufgeschweißten CFK-Laminatstreifen, in Grün die beiden Schalenhälften. Die Schnittdarstellung auf der rechten Seite zeigt das Prinzip der zueinander positionierten, gestuften Flugzeugrumpfschalen und wie die Streifen in den Stufen liegen (Bild: Fraunhofer IFAM)
31.10.2024 Automatisiertes dynamisches Dichten mit Thermoplasten
Automatisiertes Spaltfüllen an thermoplastischen CFK-Flugzeugrumpfschalen zur Vermeidung von Feuchtigkeits- und Gaseinschlüssen
Die stetige Weiterentwicklung der Luftfahrtindustrie erfordert permanente Anpassungen, um die Leistungsfähigkeit von Flugzeugen zu optimieren und gleichzeitig ihr Gewicht zu minimieren. In dem Zusammenhang gewinnen thermoplastische carbonfaserverstärkte Kunststoff-(CFK-)Strukturen, kombiniert mit fortschrittlichen Fügekonzepten, an Relevanz. Trotz hochentwickelter Fügeverfahren entstehen aufgrund fertigungsbedingter Toleranzen gelegentlich Spalte und Hohlräume, die im Anschluss gezielt aufgefüllt werden müssen. Die Versiegelung der Fügezonen und Spalte – zum Schutz vor externen Einflüssen wie Witterung und somit zur Gewährleistung der vielfältigen Vorteile der thermoplastischen CFK-Strukturen – kann durch die Entwicklung automatisierter Spaltfüllprozesse realisiert werden. Dies zeigen die Ergebnisse des 2024 abgeschlossenen Clean Sky 2/Clean Aviation „Large Passenger Aircraft“ („LPA“) -Projekts „BUSTI“.
Ein Schritt in Richtung klimaneutrale Zukunft in der Luftfahrt war bereits die Substitution von Aluminiumlegierungen durch Faserverbundkunststoffe (FVK) in Luftfahrzeugstrukturen. Technologisch bewährt haben sich besonders FVK auf duroplastischer Basis. Die Implementierung wiederaufschmelzbarer, thermoplastischer Polymermatrices bringt eine Menge Vorteile gegenüber einer duroplastischen Matrix mit sich: kürzere Zykluszeiten, unbegrenzte Lagerzeit der Halbzeuge sowie bessere mechanische Eigenschaften und Recyclingmöglichkeiten. Thermoplastische Faserkunststoffverbunde verfügen zudem über ein höheres Automatisierungspotenzial, was eine wirtschaftliche Fertigung von Bauteilen in großen Stückzahlen ermöglicht. Zudem werden völlig neue Fügeprozesse realisierbar, die eine stoffschlüssige Verbindung der Fügepartner ohne zusätzliche Anwendung von Verbindungselementen oder Klebstoffen gewährleisten. Allerdings treten beim Fügen einzelner FVK-Bauteile zu einer Gesamtstruktur fertigungs- und montagebedingt Spalte und Fugen (Gaps) variierender Breite und Länge auf. Solche Gaps lassen Flüssigkeiten und Gase einbzw. austreten, was zur Beeinträchtigung der Strukturfestigkeit führen kann. Besonders in der Luftfahrt müssen Fügestellen dicht gegenüber Flüssigkeiten und Gasen sein. Je nach Fügeverfahren und nachgelagerter Bearbeitung werden Spalte und Fugen heutzutage mit gängigen Dichtstoffen gefüllt („Gap-Filling“) bzw. versiegelt. Bei den Dichtstoffen handelt es sich meist um Epoxide, Polyurethane, MS-Polymere, Polysulfide und Silikone, die für Faserkunststoffverbunde mit duroplastischer Matrix von Bedeutung sind.