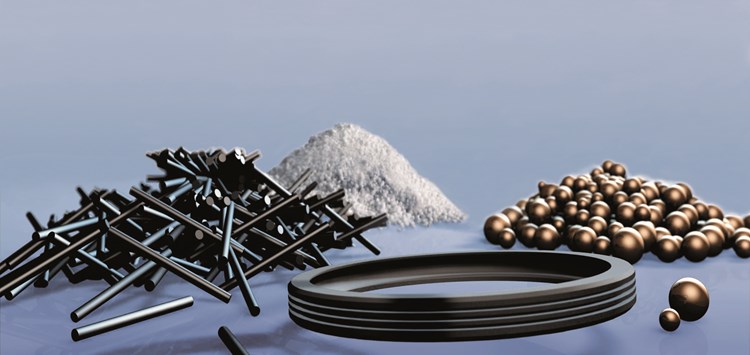
Moderne PTFE-Compounds lassen sich gut an die jeweilige Anforderung anpassen – hier die Kombination verschiedener Füllstoffe für einen Radialwellendichtring (Bild: Dyneon GmbH)
15.09.2017 Ausreichend Lösungspotenzial
Aktuelle Trends bei Rohstoffen und Mischungen
Wirtschaftlichere Systemlösungen, Sicherheit in der Anwendung und Vermeidung von Teileversagen im Einsatz sind häufig gestellte Anforderungen an eine Dichtungslösung.
Insbesondere bei dynamischen Dichtungen, z.B. dem Radialwellendichtring, müssen bei der konstruktiven Auslegung Lösungen für verschiedene Anforderungen umgesetzt werden: Elastisches, abriebarmes Verhalten im Bereich der Lippenausführung, Druckresistenz und hohe Festigkeit im Einspannbereich. Zur Umsetzung dieses breiten, teilweise gegenläufigen Anforderungsprofils wird bei herkömmlichen Dichtungsausführungen üblicherweise eine Mehrzahl von Komponenten aus Metall, Elastomeren und Thermoplasten eingesetzt. Die dabei zusätzlich erforderliche Verbundtechnologie stellt eine weitere Herausforderung für den sicheren Betrieb dar.
Die Reduzierung der Anzahl erforderlicher Komponenten für eine Gesamtlösung ist nicht nur die wesentliche Stellgröße zur Kostenreduzierung, sondern erleichtert auch die Logistik in der Herstellung und erhöht die Betriebssicherheit im Einsatz. Durch ein breites Spektrum an Compounds basiered auf unserem PTFE und Modified PTFE Produktportfolio lassen sich die unterschiedlichen Anforderungen in nur einem Bauteil umsetzen. Das günstige Abriebverhalten einer elastisch-federnden Dichtlippe wird durch eine Füllstoffkombination erzielt, die einen niederen Reibungskoeffizient mit hohem Widerstand gegen Abrieb verbindet, wobei der Gewichtsanteil der Füllstoffe insgesamt nieder sein sollte. Der Gesamtbereich der möglichen Füllstoffbeladung hingegen sollte im „statischen Einspannbereich“ der Dichtungskonstruktion ausgenutzt werden, um dadurch, noch zusätzlich verstärkt durch den Matrixwerkstoff 3MTM DyneonTM TFMTM Modified PTFE, maximale Druckresistenz zur Erzielung konstant hoher Einspannkräfte umzusetzen.
Zur Vermeidung aufwändiger Fügetechnik, wie z.B. Schweißen, wird die Verbindung der Werkstoffe durch gemeinsames Verpressen der als rieselfähige Pulver vorliegenden Compounds empfohlen. Als Technik bieten sich hierzu die schichtweise Befüllung von Pressformen, in Analogie zu den additiven Fertigungsverfahren, oder die separate Befüllung der in Kammern unterteilten Presskavitäten an. Gute Rieseleigenschaften und homogenes Schüttgewicht der Compounds sind unbedingte Voraussetzung für eine hohe Fertigungsqualität. Anschließend erfolgt dann die Verdichtung der Pulver in einem einzigen Pressvorgang. Dem Pressvorgang schließt sich ein Sinterprozess an, durch den der Aufbau des Werkstoffverbundes erfolgt. Durch gezielte Variation der Compound-Kornhärte sowie die Verwendung von sowohl Standard als auch TFM Modified PTFE als Matrixwerkstoff werden die Eigenschaften der verschiedenen Compounds für den Press- und den Sinterprozess entsprechend angeglichen. Unsere PTFE Compounds mit guter Rieselfähigkeit und homogenem Schüttgewicht ermöglichen das Automatisieren des Produktionsprozesses, eine weitere wichtige Voraussetzung zur Steigerung von Wirtschaftlichkeit und Qualitätskonstanz.
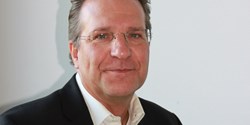
„Moderne PTFE-Compounds erlauben einfachere Dichtstellenkonstruktionen und tragen damit zur Komplexitätsreduktion des Bauteils, Kostensenkung und Erhöhung der Anlagenverfügbarkeit bei.“ Gerd Beul, Product Manager PTFE and PTFE Compounds Europe, Dyneon GmbH
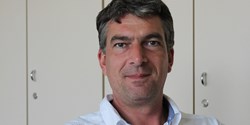
„Moderne PTFE-Compounds erlauben einfachere Dichtstellenkonstruktionen und tragen damit zur Komplexitätsreduktion des Bauteils, Kostensenkung und Erhöhung der Anlagenverfügbarkeit bei.“ Robert Veenendaal, Application and Product Development PTFE Compounds Europe, Dyneon GmbH