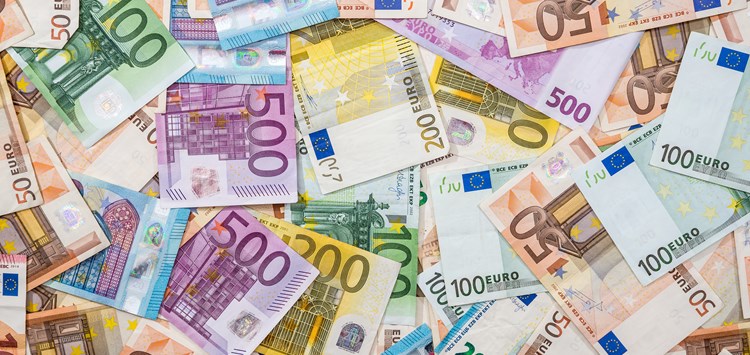
(Bild: AdobeStock_RomanR)
10.09.2024 100.000 € mit 3D-Druck einsparen
Provokante Überschrift, oder? Eigentlich nicht, denn dass es möglich ist, mit 3D-Druck viel Geld einzusparen, haben bereits mehrere branchenübergreifende Use-Cases in der Industrie bewiesen.
Aber noch eins vorweg: Es geht hier nicht darum, wie ein mittelständisches Unternehmen einfach nur das Glück hatte, eine Anwendung zu finden und diese aufgrund seiner Kenntnisse professionell so umkonstruiert hat, dass es beim ersten Testversuch Erfolg hatte und somit eine fünf- bis sechsstellige Summe eingespart werden konnte. Das wäre unrealistisch und beschönigt, wie so vieles, was die 3D-Druck-Branche unter Marketinggesichtspunkten kommuniziert.
Man muss, um genau solche „Geldbringer-Anwendungen“ zu finden, weder additiv konstruieren können, noch alle Technologien und Materialien kennen. Bei der komplexen 3D-Druck Technik ist es sowieso sinnvoll, den Rat von Expert:innen einzuholen. Man muss nicht alles alleine machen.
Beim Finden von kostensenkenden 3D-Druck- Anwendungen ist ein konsequentes Rethink eines Produktes wichtig. Das vermeidet, dass man – wie so oft der Fall – nur in Abwandlungen denkt. Welche Fähigkeit braucht man also, um beim Rethink genau dort hinzusehen, wo aktuell sonst niemand hinschaut? Soviel vorweg: Es sind meist die einfachsten und banalsten Anwendungen, die den größten Einsparungseffekt erzeugen. Und der Einsparprozess an sich ist überall der gleiche – wie auch bei üblichen Verbesserungsprozessen, in denen etwas weggelassen wird, etwas hinzukommt oder grundlegend verändert wird. Die Vorteile bzw. Einsparungen – etwa beim 3D-Druck von Dichtungen, Formteilen oder Bauteilen mit Dichtungsfunktion – können sowohl bei Konstruktion und Entwicklung, in Fertigung, Montage, Ersatzteilmanagement etc. realisiert werden, an die man oft gar nicht gedacht hat oder die bei einer Potenzialanalyse links liegen gelassen wurden. So haben z.B. eine automatische Montage, eine Elektromontage, das Laserbeschriften, die Verwaltung und auch die Lagerhaltung erstmal grundsätzlich nichts mit 3D-Druck zu tun.
In Projekten entscheidet sich an dieser Stelle, wer nur die Anwendungen im Fokus hat oder wer gedanklich bei Fragestellungen oder zu lösenden Problemen im Produktkontext beginnt. Mit letzterer Sichtweise trifft man eher auf Probleme, die eigentlich gar nicht als solche wahrgenommen werden, da man es ja „schon immer so gemacht hat“. Es ist vielleicht etwas umständlich und auch die Prozesskette löst an verschiedenen Stellen schnell mal Stress aus – aber so ist das halt, oder? Muss es aber nicht: Wenn Kolleg:innen aus der Abteilung entlang der Prozesskette aus irgendeinem Grund laut fluchen, einen Auftrag bis zur Deadline liegen lassen oder sich bei Vorgesetzten aufregen und ihre Sorgen mitteilen, sollte man hellhörig werden. Hieraus resultieren u.U. schon erste Impulse, über eine 3D-Druck-Anwendung nachzudenken.
Ein Beispiel aus dem Umfeld der Betriebs- und Hilfsmittel, z.B. zur Herstellung von Dichtungen oder für den Klebstoffauftrag: Die Einsparung liegt nicht darin, eine Vorrichtung komplett neu zu drucken und zu hoffen, dass diese dann günstiger ist, sondern darin, nur die notwendigsten Änderungen vorzunehmen. Es sind genau die Änderungen, die Kolleg:innen benötigen, um stressfreier, effizienter und qualitätssicherer zu arbeiten. 3D-gedruckte Sonderdüsen und -mischer bieten hier, z.B. für den Dicht- und Klebstoffauftrag, ein interessantes Potenzial. Eine Lösung, die die Qualität nachhaltig steigert (weniger Reklamationen), eigene Basteleien verhindert oder die die dritte Hand von Kolleg:innen überflüssig macht, kann unter Vollkostenbetrachtungen schnell hohe Kosten einsparen. Wenn das bereits bei einer Anwendung der Fall ist, sollte man mal hochrechnen, wie sich das bei Hunderten von Anwendungen in einem Unternehmen potenziert.
Kosten lassen sich also nicht nur bei „Raketenteilen“ einsparen, wie es vielfach immer noch angenommen wird, sondern schon bei den einfachsten Teilen. Und, sind wir ehrlich, ob das benötigte Bauteil, das für die Verbesserung sorgt, konventionell oder per 3D-Druck hergestellt wird, ist erstmal gar nicht die Frage. Am schnellsten, günstigsten und einfachsten geht es jedoch bei immer mehr Bauteilen mit dem 3D-Druck. Gedruckte Klebdüsen und -mischer beweisen hier gerade ihr Potenzial.
Das Finden von geeigneten 3D-Druck-Anwendungen ist kein Glücksspiel oder Zufall, sondern eine systematisierte Methode, die einfach in acht Schritten in jeder Abteilung im Unternehmen angewendet werden und im Jahr mehr als eine sechsstellige Summe einsparen kann. Diese von mir entwickelte K3A-Methode (Kommunikative 3D-Druck-Anwendungsfindung) ist auf Basis vieler Potenzialanalysen bei Unternehmen im deutschen Mittelstand entwickelt worden.
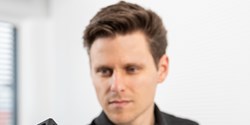
„Einsparpotenziale lassen sich systematisch ermitteln, der 3D-Druck ist dann meist nur der Enabler.“ Johannes Lutz, Geschäftsführer, 3D Industrie GmbH