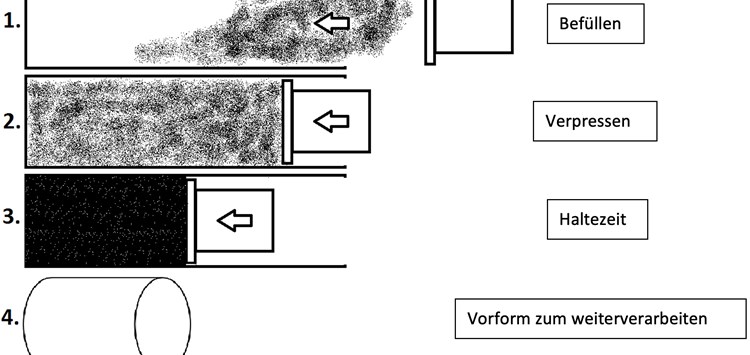
Herstellungsprozess der zylindrischen Vorform für virginales PTFE (Bild: TEADIT Group)
29.10.2021 Was bei PTFE-Flachdichtungen zu beachten ist
Besonderheiten und Vergleich verschiedener Typen und Herstellungsverfahren
Je nach Polymerisationsart, Rezeptur und Pulverbeschaffenheit und je nach Verarbeitungsverfahren eignet sich PTFE für unterschiedliche Einsatzbereiche wie Dichtungen. Hier kommen PTFE-Materialien in verschiedenen Formen und Produkten zur Anwendung. Um die jeweils beste Lösung zu ermitteln, sind
nachfolgend die gängigsten PTFE-Flachdichtungsmaterialien und deren Herstellungsverfahren beschrieben und anhand von Vergleichsuntersuchungen abgegrenzt.
Obwohl ein Thermoplast, kann PTFE aufgrund des überaus hohen Molekulargewichtes und der hohen Schmelzviskosität nicht wie andere Thermoplaste aus der Schmelze, sondern nur mittels verschiedener Press- und Sintertechniken verarbeitet werden.
Das pulverförmige Polymer sollte bei Raumtemperatur zu einem Vorformling – i.d.R. in zylindrische Form – verpresst werden (Bild 1). Hierbei wird die lockere Pulverschüttung verdichtet und mit einem bestimmten Pressdruck komprimiert. Teilweise werden beim Mischen unterschiedliche Füllstoffe, wie z.B. Glas oder Silikat, sowie Farbpigmente zugesetzt. Der Pressvorgang sollte langsam, gleichmäßig und ohne Unterbrechung erfolgen. Nach dem Erreichen des maximalen Druckes sollte darüber hinaus eine Druckhaltezeit berücksichtigt werden, um ein Partikelfließen zu ermöglichen und um interne Spannungsspitzen oder Unregelmäßigkeiten abzubauen. Nach einer langsamen Entspannung wird der Pressling idealerweise für eine bestimmte Zeit spannungsfrei gelagert, um Spannungsausgleich zu ermöglichen.
Nach dem Pressen werden die Presslinge einem definierten Sinterzyklus ausgesetzt. Hierbei erfolgt ein definiertes und dem Pressling angepasstes Aufheizen und letztendlich eine zeitgesteuerte Sinterung bei einer Temperatur von 370 °C bis 380 °C. Nach Überschreiten des Kristallisationsschmelzpunktes bei etwa 345 °C sintern die zuvor komprimierten Pulverteilchen zu einem homogenen Gefüge zusammen. Trotz Erreichen bzw. Überschreiten des Schmelz-/Gelpunktes erfolgt das Sintern der Pressteile „formfrei“, da aufgrund des hohen Molekulargewichtes die Gelstabilität von PTFE sehr hoch ist.
Nach dem vollständigen Sintern des Pressteiles wird abgekühlt. Insbesondere der Temperaturbereich zwischen der Sintertemperatur und ca. 260 °C sollte langsam durchfahren werden. Je gleichmäßiger der Presskörper abgekühlt wird, umso geringer das Spannungsniveau und umso unwahrscheinlicher treten Risse auf. Nach dem vollständigen Abkühlen der Pressteile (Bild 2) werden diese zumeist einer weiteren spanabhebenden Formgebung wie dem Schälen zu Platten, bzw. Drehen, Bohren, Fräsen bei direkter Dichtungsherstellung unterzogen.